電爐煉鋅法
(1)方法簡(jiǎn)介
電爐煉鋅是利用電能直接加熱爐料連續(xù)蒸餾生產(chǎn)鋅的方法,其主要工序包括混料、制粒干燥、電爐還原熔煉和冷凝四部分。將細(xì)磨的高品質(zhì)氧化鋅礦和相應(yīng)的焦炭混合、制粒、干燥后加入還原電爐內(nèi)熔化還原,在高溫和強(qiáng)還原氣氛下,物料中的鋅被還原并以鋅蒸氣的形態(tài)產(chǎn)出,含鋅和CO的氣體再經(jīng)凈化、急冷,并以鋅粉形態(tài)產(chǎn)出。也有在電爐后端接鋅雨冷凝器,使鋅以粗鋅形態(tài)產(chǎn)出。
(2)技術(shù)特點(diǎn)
電爐煉鋅法對(duì)原料成分要求不嚴(yán),隨著直流電爐的成功應(yīng)用,電爐電耗也大幅下降。由于電耗高,電爐煉鋅的應(yīng)用受到很大限制,目前僅在我國(guó)部分邊遠(yuǎn)省區(qū)如云南、貴州等氧化鋅資源豐富、電力供應(yīng)充足的地方有所發(fā)展,總裝機(jī)功率約120000 kVA,年產(chǎn)鋅量10~15萬(wàn)t,其中最大的會(huì)澤縣滇北工貿(mào)有限公司,年產(chǎn)量為2萬(wàn)t。
常規(guī)浸出法
(1)方法簡(jiǎn)介
浮選硫化鋅精礦經(jīng)過(guò)配料、干燥、破碎、篩分后,用皮帶拋料機(jī)拋入沸騰熔燒爐中進(jìn)行焙燒,得到焙砂和SO煙氣。煙氣經(jīng)冷卻、除塵和凈化后,送硫酸系統(tǒng)采用兩轉(zhuǎn)兩吸工藝生產(chǎn)硫酸。
焙砂送浸出系統(tǒng)用稀硫酸進(jìn)行中性浸出,同時(shí)用水解法除去中性浸出液中的鐵和大部分砷、銻、鍺等雜質(zhì)。中性浸出渣再用稍濃的硫酸進(jìn)行低酸性浸出,以盡量把中浸渣中的可溶鋅溶解出來(lái)。酸性浸出液返回中性浸出。酸性浸出渣進(jìn)入銀浮選系統(tǒng)回收銀,得到的銀精礦送鉛冶煉系統(tǒng)。浮選尾渣送揮發(fā)窯系統(tǒng)回收次氧化鋅,渣中鉛、銦、鍺、鎘、銀大部分或部分進(jìn)入次氧化鋅而得到富集回收。
中性浸出的上清液送往凈化系統(tǒng)。凈化工藝一般采用三段鋅粉置換法,第一段加鋅粉除銅鎘,得到的銅鎘渣送鎘系統(tǒng)生產(chǎn)金屬鎘,提鎘后的銅渣再送銅系統(tǒng)回收銅;第二段將溶液升溫加鋅粉和活化劑銻鹽或砷鹽除鈷鎳,得到的鈷渣送鈷系統(tǒng)回收鈷鎳;第三段加鋅粉除復(fù)熔鎘,得到的純凈硫酸鋅溶液送電解新液罐冷卻沉淀后再配送鋅電積槽,得到的凈化渣返回第一段凈化。
在電解槽內(nèi),通直流電,純凈的鋅在陰極板上析出,陽(yáng)極放出氧氣。析出鋅自陰極剝離后熔鑄成鋅錠或配制成合金錠。廢電解液返回浸出工序循環(huán)使用。
常規(guī)浸出法的原則工藝流程見(jiàn)圖3-47。常規(guī)浸出法仍然是我國(guó)濕法煉鋅的主要生產(chǎn)方法,其產(chǎn)量占濕法煉鋅總產(chǎn)量的60%以上。由于歷史的原因,老的生產(chǎn)系統(tǒng)在生產(chǎn)規(guī)模、資源綜合利用、環(huán)境保護(hù)、節(jié)能減排、勞動(dòng)生產(chǎn)率等諸多方面存在明顯的缺陷。小型的道爾型沸騰焙燒爐,低空污染較大,床能力低,余熱利用差。浸出過(guò)程現(xiàn)場(chǎng)環(huán)境差,車(chē)間廢水零排放壓力大。溶液凈化深度不高,鋅粉消耗高,自動(dòng)化控制手段幾乎沒(méi)有。電積基本上是采用小極板,人工剝鋅,酸霧重。鋅熔鑄是用能耗高、效率低的小型電爐。特別是浸出渣采用威爾茲爐揮發(fā)處理,能耗很高,不僅不經(jīng)濟(jì),而且低濃度SO污染嚴(yán)重。
典型的濕法煉鋅的化學(xué)反應(yīng)過(guò)程如圖3-48所示。

(2)技術(shù)特點(diǎn)
常規(guī)浸出方法工藝成熟,生產(chǎn)穩(wěn)定,但由于焙砂中的鐵酸鋅不能被稀硫酸浸出,因而其浸出渣中通常含有20%左右的鋅,并由此導(dǎo)致了以下一些主要問(wèn)題:
①浸出渣量大,噸鋅產(chǎn)出的浸出渣0.8~0.9t;
②浸出渣含鋅高,通常在20%~22%;
③浸出渣須采用揮發(fā)窯處理,能耗高,耐火材料消耗大;
④金屬回收率低,揮發(fā)窯渣中仍含有200~300g/t的銀和2%~5%的鋅;
⑤揮發(fā)窯尾氣SO含量超標(biāo)嚴(yán)重,治理成本很高;
⑥凈化過(guò)程,鋅粉消耗較高;
⑦鋅直接回收率低;
⑧鋅電解及熔鑄的勞動(dòng)強(qiáng)度大。
我國(guó)的常規(guī)浸出法在金屬回收水平、能耗水平、二次資源開(kāi)發(fā)利用水平等方面,與國(guó)外先進(jìn)水平相比仍有較大差距。以株洲冶煉廠為例,其每年產(chǎn)出的約20萬(wàn)t揮發(fā)窯渣中仍含有1.5%~2%的銅、3%~7%的鋅、0.5~1.0g/t的金、200~300 g/t的銀、150~300 g/t的錮、30%~40%的鐵,即約有3000 t銅、40~60 t銀,約200 kg金,6000~14000 t鋅。目前采用物理分選方法回收處理,但效果較差。與國(guó)外先進(jìn)企業(yè)的差距情況列于表3-24。
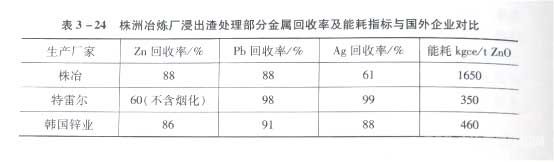
浸出渣回轉(zhuǎn)窯揮發(fā)的主要缺陷如下:
①能耗高。生產(chǎn)1t ZnO需要消耗1.7t焦粉,還需要消耗大量的水、電、壓縮風(fēng)等;
②金屬回收率低。統(tǒng)計(jì)數(shù)據(jù)表明,揮發(fā)窯金屬揮發(fā)率分別為Zn 88.03%,Pb 88.76%,In 76.11%;Ag 61%;
③加工費(fèi)高。窯內(nèi)襯耐火材料消耗較高,導(dǎo)致加工費(fèi)高,每噸 ZnO加工費(fèi)達(dá)2700元;
④環(huán)境污染重。浸出渣中的硫在揮發(fā)過(guò)程進(jìn)入氣相,因濃度低無(wú)法回收,采用液堿吸收的處理成本很高;
⑤廢渣產(chǎn)生量大。每處理1t浸出渣產(chǎn)生0.8t廢渣,未回收的有價(jià)金屬進(jìn)入廢渣中很難進(jìn)行回收處理,存在嚴(yán)重的污染隱患。
鋅冶煉過(guò)程主要雜質(zhì)元素的分布及對(duì)流程的影響情況見(jiàn)表3-25。

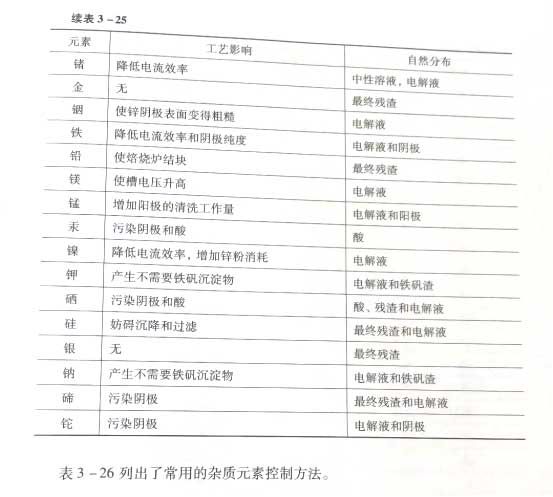
表3-26列出了常用的雜質(zhì)元素控制方法。

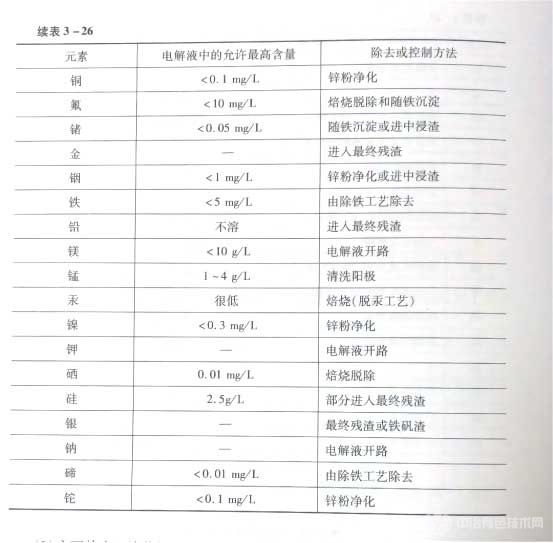
(3)主要技術(shù)經(jīng)濟(jì)指標(biāo)
(4)常規(guī)浸出法各工序技術(shù)經(jīng)濟(jì)指標(biāo)見(jiàn)3-27.
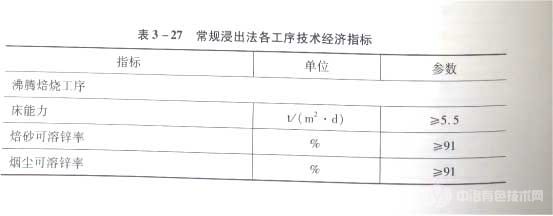

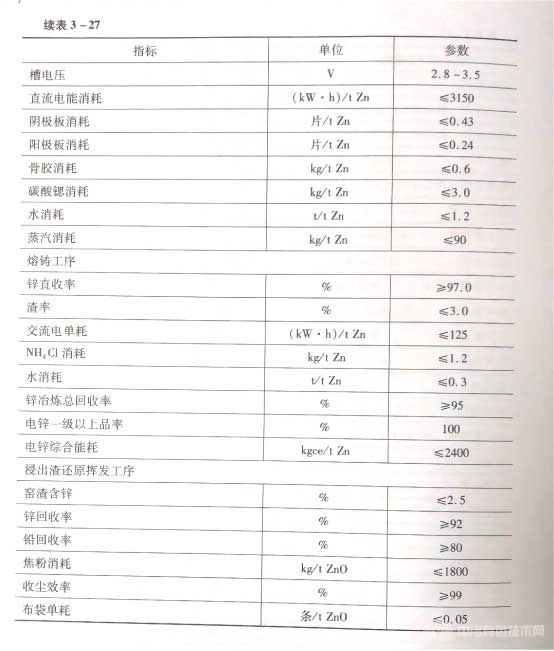
(4)國(guó)內(nèi)應(yīng)用廠家及產(chǎn)能
除株洲冶煉廠外,采用常規(guī)浸出法的冶煉企業(yè)主要有:葫蘆島鋅業(yè)股份有限公司(13萬(wàn)t/a)、永春福源鋅業(yè)有限公司(10.5萬(wàn)t/a)、保靖縣鋅業(yè)開(kāi)發(fā)有限責(zé)任公司(3萬(wàn)t/a)、南丹縣金山銦鍺冶金化工有限公司(10萬(wàn)t/a)、云南馳宏鋅鍺股份有限公司(20萬(wàn)t/a)、湖南金石鋅業(yè)有限責(zé)任公司(5萬(wàn)t/a)、云南云銅鋅業(yè)股份有限公司(3萬(wàn)t/a)、云錫集團(tuán)鋅業(yè)有限責(zé)任公司(3萬(wàn)t/a)、云南馬關(guān)鋅業(yè)有限公司(5萬(wàn)t/a)等。
(5)總體評(píng)價(jià)
常規(guī)浸出方法工藝成熟,生產(chǎn)穩(wěn)定,是目前我國(guó)濕法煉鋅的主要生產(chǎn)方法。但由于其在資源綜合利用、環(huán)境保護(hù)、節(jié)能減排、勞動(dòng)生產(chǎn)率等方面存在諸多明顯缺陷,新建的濕法煉鋅廠已很少采用。