國(guó)內(nèi)外鋁冶金工藝比較與現(xiàn)狀評(píng)價(jià)
國(guó)外氧化鋁生產(chǎn)方法主要是傳統(tǒng)的拜耳法,大約占國(guó)外氧化鋁總產(chǎn)量的96%;其余約4%的產(chǎn)量由拜耳-燒結(jié)聯(lián)合法生產(chǎn),主要來(lái)自于俄羅斯和哈薩克斯坦的氧化鋁廠,俄羅斯采用聯(lián)合法處理霞石礦,生產(chǎn)氧化鋁和副產(chǎn)硫酸鉀,而哈薩克斯坦采用串聯(lián)法從低品位三水鋁石礦中生產(chǎn)氧化鋁。
由于國(guó)內(nèi)外鋁土礦資源的性質(zhì)和品位不同,雜質(zhì)含量也相差較遠(yuǎn),因此難于比較。國(guó)外傳統(tǒng)的拜耳法流程基本與中國(guó)的拜耳法流程相似。中國(guó)氧化鋁企業(yè)除了山東省企業(yè)采用低溫拜耳法處理進(jìn)口三水鋁石礦外,其他中國(guó)氧化鋁企業(yè)全部采用了高溫拜耳法技術(shù),同時(shí)為了解決鋁土礦品位較低的難題,中國(guó)還開(kāi)發(fā)出選礦拜耳法和石灰拜耳法技術(shù),這與國(guó)外拜耳法有所不同。
中國(guó)的拜耳-燒結(jié)聯(lián)合法也與俄羅斯和哈薩克斯坦的不同,中國(guó)主要采用了混聯(lián)法技術(shù),目前正在向串聯(lián)法過(guò)渡,但仍然在燒結(jié)法配料中加入少量鋁土礦。因此中國(guó)的能耗總體上比國(guó)外氧化鋁生產(chǎn)平均水平高,石灰消耗和堿耗也偏高。
但中國(guó)鋁土礦氧化鋁含量較高,礦耗和赤泥產(chǎn)出量較低,見(jiàn)表3-32。
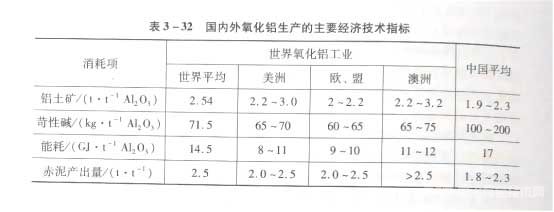
鋁電解工藝比較與評(píng)價(jià)
國(guó)外典型電解鋁生產(chǎn)方法與中國(guó)無(wú)大差異,自焙槽技術(shù)也因?yàn)榄h(huán)境污染問(wèn)題正在逐步淘汰,大部分都應(yīng)用大型預(yù)焙槽技術(shù)。但電解槽電流容量的多樣性與中國(guó)有所不同,國(guó)外電解鋁廠通常采用少數(shù)規(guī)格電流容量電解槽,如200kA、300 kA、350 kA等槽型。而中國(guó)幾乎采用了更多的槽型,從160 kA 到500 kA,大約有十多種。國(guó)內(nèi)外電解鋁企業(yè)主要技術(shù)經(jīng)濟(jì)指標(biāo)比較見(jiàn)表3-33。
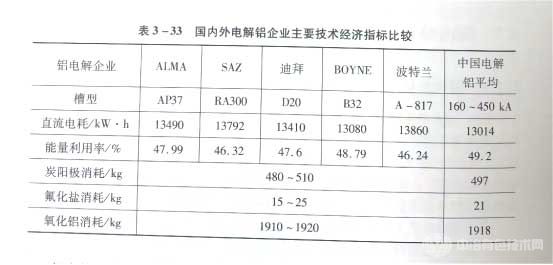
鋁電解技術(shù)方面,國(guó)外都采用高電流密度、高電流效率、低陽(yáng)極效應(yīng)系數(shù)的生產(chǎn)運(yùn)行模式。因而單槽產(chǎn)出率高、直流電耗也高,能量利用率較低。而中國(guó)電解鋁企業(yè)因電價(jià)較高,則采用低電流密度、低電壓和低直流電耗以及較低電流效率的生產(chǎn)運(yùn)行模式,因而往往單槽產(chǎn)出率較低,但電耗也較低。
國(guó)內(nèi)外銅冶金工藝比較與現(xiàn)狀評(píng)價(jià)
(1)銅冶煉先進(jìn)技術(shù)及其代表企業(yè)
據(jù)國(guó)際銅研究組織(ICSG,International copper study group)報(bào)告,2011年全球銅冶煉產(chǎn)量約1580萬(wàn)t,其中礦產(chǎn)銅約1300萬(wàn)t,占82%,再生銅約280萬(wàn)t,占18%。2011年冶煉銅產(chǎn)量前20位的國(guó)家排名見(jiàn)圖3-57。前5位分別為中國(guó)(470萬(wàn)t,占37%)、日本(140萬(wàn)t,占9%)、智利(140萬(wàn)t,占9%)、俄羅斯(80 萬(wàn)t,占5%)、印度(65萬(wàn)t,占4%)。
表3-34為2011年全球按產(chǎn)能排名前20位煉銅廠的情況。我國(guó)貴溪冶煉廠產(chǎn)能最大,達(dá)到年產(chǎn)90萬(wàn)t銅規(guī)模。排名第20位為日本直島煉銅廠,產(chǎn)能為30.6萬(wàn)t,前20位銅廠總產(chǎn)能高達(dá)772萬(wàn)t,約占火法煉銅(含礦產(chǎn)銅和再生銅)全球產(chǎn)能的50%。因此,這些煉銅廠應(yīng)能反映當(dāng)前世界銅冶煉總體情況。
在2011年產(chǎn)能世界前20位銅廠中,使用奧圖泰閃速熔煉的有11家(少數(shù)冶煉廠使用多種技術(shù)),其中雙閃法2家,應(yīng)用最為廣泛。使用TSL(艾薩,奧圖泰-澳斯麥特)法4家,其中艾薩法3家,奧圖泰-澳斯麥特法1家。使用三菱連續(xù)煉銅法的3家。使用特尼恩特法2家、反射爐2家、電爐2家、瓦紐科夫1家、諾蘭達(dá)1家??傮w來(lái)看,煉銅技術(shù)領(lǐng)先的國(guó)家為中國(guó)、美國(guó)、日本等,這些國(guó)家大型銅廠主要采用奧圖泰閃速熔煉—P-S吹煉、奧圖泰閃速熔煉—肯尼科特-奧圖泰閃速吹煉、TSL(艾薩、奧圖泰-澳斯麥特)法、三菱法連續(xù)煉銅等技術(shù)。智利、俄羅斯和印度,盡管銅產(chǎn)量位居全球前5位之列,但仍在應(yīng)用反射爐、電爐、特尼恩特爐、諾蘭達(dá)爐等技術(shù)。我國(guó)在銅冶金技術(shù)發(fā)展上走了一條引進(jìn)、集成、再創(chuàng)新的道路,目前,一批企業(yè)在規(guī)模、技術(shù)、裝備、能耗、環(huán)保和綜合回收等多方面,已居于世界先進(jìn)水平,部分技術(shù)和裝備已開(kāi)始出口國(guó)外。
表3-35所列為目前火法煉銅先進(jìn)且應(yīng)用較廣的技術(shù)及其國(guó)內(nèi)外代表企業(yè)。其中,雙閃法、奧圖泰閃速熔煉—P-S轉(zhuǎn)爐吹煉、TSL(艾薩、澳斯麥特)法,國(guó)內(nèi)外均有水平高的代表性企業(yè)。
我國(guó)富氧底吹爐和雙側(cè)吹爐有較廣泛的應(yīng)用,但國(guó)外應(yīng)用較少,缺乏代表性數(shù)據(jù)。三菱法也屬較先進(jìn)的煉銅法,我國(guó)沒(méi)有應(yīng)用,也無(wú)從進(jìn)行比較。
奧圖泰閃速熔煉—肯尼科特-奧圖泰閃速吹煉、奧圖泰閃速熔煉—P-S轉(zhuǎn)爐吹煉、TSL熔池熔煉—P-S轉(zhuǎn)爐吹煉是國(guó)內(nèi)外應(yīng)用最廣泛的幾種銅火法冶金技術(shù),富氧底吹、雙側(cè)吹近年來(lái)在國(guó)內(nèi)也得到一定的推廣,但在國(guó)外并未得到廣泛應(yīng)用,瓦紐科夫(雙側(cè)吹)法在國(guó)際上應(yīng)用水平也不高。就國(guó)內(nèi)外應(yīng)用較廣的3種火法煉銅方法,國(guó)內(nèi)外各選1家水平較高的代表性工廠,就工藝、裝備、技術(shù)經(jīng)濟(jì)與能耗和環(huán)保等指標(biāo)進(jìn)行了比較,見(jiàn)表3-36。
能耗:從銅精礦到陽(yáng)極銅,上述3種方法國(guó)內(nèi)外代表廠家,工藝能耗水平大致相當(dāng),在11000 MJ/1陽(yáng)極銅左右,折算成標(biāo)煤為375 kgce/t 陽(yáng)極銅左右GB21248——2007規(guī)定的銅冶煉企業(yè)從銅精礦到陽(yáng)極銅能耗先進(jìn)值為≤380kgce/陽(yáng)極銅,與其相當(dāng)吻合。閃速熔煉只能處理干燥物料(含水小于0.3%),要采用回轉(zhuǎn)窯、氣流干燥、蒸汽干燥等方式對(duì)爐料進(jìn)行干燥,從能耗和環(huán)保方面考慮采用蒸汽干燥最為有利,目前已普遍采用這一方式。熔池熔煉(三菱法除外)爐料含水8%~10%,僅考慮備料工序,能耗較閃速熔煉小,但由于熔煉煙氣含有大量水分,在余熱回收方面是不利的,因此總體而言,熔池熔煉加濕料在能耗方面并無(wú)優(yōu)勢(shì)。閃速吹煉由于其不能處理冷料,和P-S轉(zhuǎn)爐比較,在能耗方面并不占有優(yōu)勢(shì)。雙閃法工藝煙氣SO濃度高,目前已普遍采用高濃度(16%~20%)SO,煙氣制酸技術(shù),而采用P-S轉(zhuǎn)爐吹煉,制酸煙氣濃度一般僅為12%SO,在制酸能耗方面,前者噸酸能耗大致僅為后者的一半,每噸酸節(jié)能約50kW·h,按1t 銅附產(chǎn)3.5 t酸折算,能耗降低約56 kgce/t陽(yáng)極銅,這是雙閃法工藝在能耗方面的優(yōu)勢(shì)所在。
余熱回收:國(guó)內(nèi)外水平較高的廠家,都對(duì)熔煉及吹煉余熱進(jìn)行了回收,產(chǎn)出蒸汽用于干燥爐料、驅(qū)動(dòng)SO主風(fēng)機(jī)及發(fā)電等,由于各廠蒸汽壓力等級(jí)及利用途徑并不完全一致,因此,僅憑發(fā)電量難以直接比較余熱回收水平。部分廠家,如我國(guó)的祥光銅業(yè)公司等,還對(duì)陽(yáng)極爐、硫酸制造中、低溫位余熱進(jìn)行了回收,因此,其工藝能耗應(yīng)處于世界領(lǐng)先地位。銅锍、爐渣冷卻余熱目前國(guó)內(nèi)外各廠家均未回收,這是今后進(jìn)一步降低能耗應(yīng)致力的研究方向。
SO2排放:雙閃法的最大優(yōu)勢(shì),在于有利于達(dá)到高的硫捕集率,實(shí)現(xiàn)火法煉銅中SO2的大規(guī)模減排。目前,采用這一工藝的國(guó)內(nèi)外廠家,硫捕集率普遍達(dá)到99.9%,噸銅SO2排放量小于2kg。提高硫捕集率的關(guān)鍵在于:第一,加強(qiáng)環(huán)境集煙及其收塵脫硫處理,如日本東予冶煉廠,采用P-S轉(zhuǎn)爐吹煉,全廠設(shè)有30多個(gè)環(huán)境集煙點(diǎn),總煙量達(dá)到45萬(wàn)m3(標(biāo))/h,采用布袋收塵、Mg(OH),料漿吸收、電除霧處理后,排空氣體SO濃度僅10~20mg/m3。第二,制酸尾氣吸收。目前,銅冶煉SO2煙氣制硫酸,國(guó)家標(biāo)準(zhǔn)(GB 25467—2010)規(guī)定尾氣SO2濃度小于400mg/m3。在此方面,政府要求最嚴(yán)格、企業(yè)減排最徹底的是日本東予冶煉廠,轉(zhuǎn)化SO2濃度為11%,轉(zhuǎn)化率為99.8%,尾氣未吸收前SO濃度為579mg/m3,采用苛性堿溶液吸收后,排空尾氣SO濃度僅為5~15mg/m3。美國(guó)肯尼科特銅公司Garfield廠,制酸SO2轉(zhuǎn)化率達(dá)99.95%,尾氣加空氣稀釋后,SO2濃度為50~70mg/m3。我國(guó)主要煉銅廠均采用“二轉(zhuǎn)二吸”技術(shù)制酸,部分系統(tǒng)轉(zhuǎn)化率偏低,不能達(dá)到GB25467——2010標(biāo)準(zhǔn),尾氣吸收脫硫后排放,部分新的系統(tǒng)制酸尾氣SO2濃度小于300mg/m3,直接達(dá)標(biāo)排放。
我國(guó)從20世紀(jì)80年代中期引進(jìn)奧圖泰閃速熔煉建成江西銅業(yè)公司貴溪冶煉廠開(kāi)始,歷經(jīng)30年努力,目前我國(guó)銅冶煉行業(yè)在技術(shù)裝備及節(jié)能減排等方面,已全面趕上和超過(guò)世界先進(jìn)水平,發(fā)展成為有色金屬領(lǐng)域最具國(guó)際競(jìng)爭(zhēng)力的行業(yè)。在能耗方面,祥光銅業(yè)、金隆銅業(yè)和云南銅業(yè)等,與國(guó)外先進(jìn)水平同類銅冶煉企業(yè)比較,已處于領(lǐng)先水平;在SO排放方面,國(guó)內(nèi)企業(yè)已全面接近甚至超過(guò)國(guó)外同類企業(yè)先進(jìn)水平。