銅冶金科技進步
我國銅冶金技術通過引進集成再創(chuàng)新,目前一批企業(yè)從規(guī)模、技術、裝備、能耗、環(huán)保、綜合回收等多方面,已居于世界先進水平,部分技術和裝備已出口國外。銅閃速熔煉技術,銅、鉛富氧溶池熔煉新技術,自主研發(fā)的“氧氣底吹煉銅新工藝”,這些具有世界先進水平的新技術、新工藝在生產中的應用,大大提升了我國重金屬冶煉技術水平。銅冶煉先進技術、富氧熔煉、余熱回收及大型回轉式陽極爐、稀氧燃燒、透氣磚通氮氣攪拌、自氧化還原等技術和裝備的使用,使冶煉過程能耗大幅度降低。煙氣濃度升高,煙氣量減少,煙氣輸送動力消耗降低使得制酸能耗進一步降低。另外,奧托昆普閃速熔煉技術朝著高銅锍品位、高氧濃度、高投料量、高熱負荷“四高”熔煉方向發(fā)展,可進一步實現(xiàn)銅閃速熔煉的高效、節(jié)能、低污染。
“雙閃”冶煉(閃速熔煉、閃速吹煉)是國際上先進的銅冶煉技術,解決了銅冶煉過程中的低空污染問題,能耗大幅降低。山東陽谷祥光銅業(yè)已引進芬蘭奧托昆普閃速熔煉和閃速吹煉雙閃速爐煉銅技術,被國家環(huán)保部評為十大“國家環(huán)境友好工程”之一。中條山有色金屬集團公司和中國恩菲工程技術有限公司開發(fā)的銅锍頂吹吹煉新工藝,有效解決了P-S轉爐逸散SO2煙氣的低空污染和作業(yè)安全問題,粗銅冶煉能耗低于490kgce/t。
我國銅冶煉近年來所取得的成績,主要得益于企業(yè)采用了先進的富氧閃速及富氧熔池熔煉工藝,這種工藝替代了反射爐、鼓風爐和電爐等傳統(tǒng)工藝,提高了熔煉的強度,降低了能耗,減少了二氧化硫的排放。閃速爐、轉爐、反射爐及自熱爐尾部均設置余熱鍋爐,充分回收利用余熱資源生產蒸汽,每年生產余熱飽和蒸汽70多萬t。在“十二五”期間,氧氣底吹爐連續(xù)煉銅技術、閃速爐短流程一步煉銅技術、新型側吹熔池熔煉等銅冶煉工藝的短流程研發(fā)成功和推廣,是銅冶煉節(jié)能減排的重要途徑。
硫化銅精礦火法煉銅包含造锍熔煉、吹煉、火法精煉和電解精煉等主要工序。其中,造锍熔煉是最核心的環(huán)節(jié)。銅冶煉節(jié)能減排主要歸因于造锍熔煉技術的進步。造锍熔煉工藝的技術進步,主要體現(xiàn)在新一代的強化熔煉技術——閃速熔煉和熔池熔煉,取代了傳統(tǒng)的鼓風爐、反射爐和電爐熔煉,實現(xiàn)了節(jié)能及SO2 減排。
表4-3所示為火法煉銅造锍熔煉新技術工業(yè)應用年份。
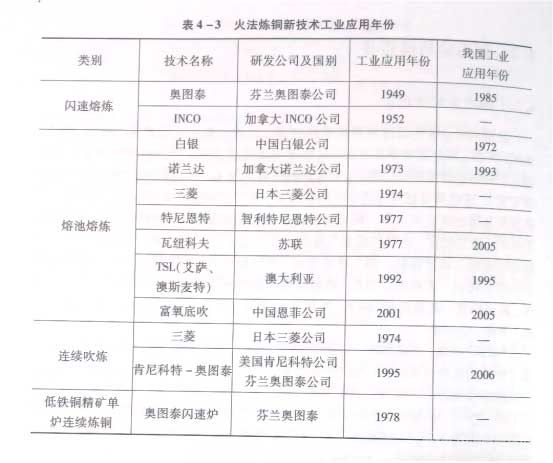
20世紀70年代得到工業(yè)應用的熔池熔煉技術有白銀法、諾蘭達法、三菱法、特尼恩特法和瓦紐科夫法。①白銀法是我國自主研發(fā)的第一種煉銅方法,20世紀70年代由中國白銀有色金屬公司及國內其他單位聯(lián)合開發(fā),1979年正式命名為“白銀煉銅法”,是一種反射爐改良技術,屬側吹熔池熔煉。白銀爐歷經多次改進:其一是由單室爐改為雙室爐(103m2,熔煉區(qū)與爐渣貧化區(qū)分開);其二,由空氣熔煉改為富氧熔煉。目前,白銀爐富氧濃度為45%~55%;第三,近年來,白銀公司與中國瑞林工程技術有限公司合作,對爐體結構等進行了改進,延長了爐齡,提高了產能【目前達10萬t Cu/(爐.a)】,改善了車間環(huán)境。目前,白銀公司有2臺100m2白銀爐在運轉,粗銅產能20萬t/a。②諾蘭達法是中國引進的第二種煉銅工藝,湖北大冶有色金屬公司在20世紀90年代初引進應用。目前,大冶公司諾蘭達爐已為澳斯麥特爐取代。③三菱法屬非浸沒式頂吹熔池熔煉,是世界上第一種成功工業(yè)應用的連續(xù)煉銅工藝,由日本三菱公司研發(fā)成功。中國沒有引進三菱法。④特尼恩特爐可單獨處理銅精礦生產高品位銅锍。特尼恩特法在智利得到廣泛應用,目前,智利有5座爐子運轉,年產銅約70萬t。特尼恩特法在中國沒有得到應用。⑤瓦紐科夫法屬側吹熔池熔煉技術。2000年以來,我國逐步掌握該技術,用于煉鉛、煉銅等方面,由此該法在我國又稱為“金峰爐”“側吹爐”“雙側吹爐”等(統(tǒng)一稱其為雙側吹爐)。目前,
我國至少有3座雙側吹爐正常運行,用于造锍熔煉(金峰、富邦、和鼎),粗銅產能約30萬t/a。
在我國銅冶煉中,除奧圖泰型閃速熔煉外,另一項得到廣泛應用的技術是浸沒式頂吹(TSL)熔池熔煉法(艾薩法和澳斯麥特法)。目前,TSL技術廣泛應用于銅、鎳、鉛、錫、鋅、電子廢料及工業(yè)垃圾處理等領域。在全球有數(shù)十座爐子在運轉。我國銅冶金方面有9座爐子用于造锍熔煉和吹煉,其中澳斯麥特爐7座,艾薩爐2座。除白銀法外,底吹爐熔煉是中國擁有自主知識產權的另一項煉銅技術。1990—1993年,中國恩菲公司及水口山有色金屬公司等單位,在氧氣底吹煉鉛試驗裝置上,開展了3000 t/a銅富氧底吹造锍熔煉半工業(yè)化試驗,取得初步成功。故該法又稱為水口山(SKS)煉銅法。1994——1995年,中國恩菲公司、中科院過程所和中條山有色金屬公司,聯(lián)合開展了底吹爐煉銅放大冷態(tài)模型研究。2001 年,中國恩菲公司采用富氧底吹法為越南建成1萬t/a的大龍銅冶煉廠,標志著該技術得到工業(yè)應用。2005年,山東方圓公司采用富氧底吹技術,建設規(guī)模為5~10萬t/a煉銅廠。2008年建成投產,標志著富氧底吹成為較為成熟的煉銅技術。隨后,國內又采用該技術相繼建成山東恒邦、內蒙古包頭華鼎、山西垣曲等煉銅廠。
在火法煉銅節(jié)能減排進程中,新的強化熔煉技術及氧氣的應用,起到了決定性的作用。氧氣的應用及富氧濃度的提高,使得煙氣量減少,煙氣SO2,濃度提高,對銅冶煉節(jié)能減排起到了關鍵作用,各種煉銅方法富氧濃度如表4-4所示。工藝模擬表明,在造锍熔煉中,使用1t0可節(jié)能5440MJ,制氧廠生產1t0,耗電285kW.h,電廠發(fā)電效率按38%計算,抵消制氧能耗后,凈節(jié)能為2740MJ,折合93.6 kgce。
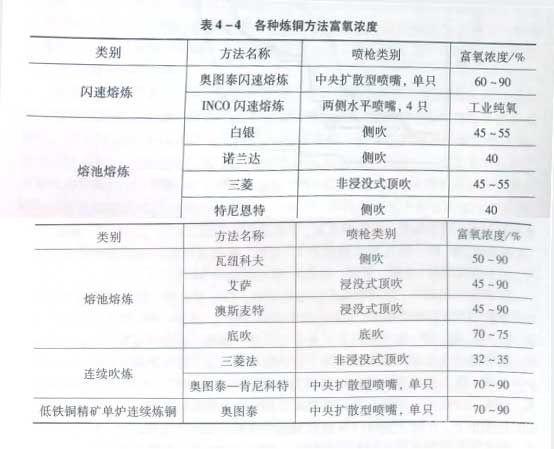
圖4-8所示為1960—2007年世界銅冶煉工業(yè)SO2捕集情況。由圖可見,在20世紀60——70年代,世界主要銅冶煉國家和地區(qū)中,僅日本和西歐SO2捕集率達到較高水平,而當時美國、智利和中國銅冶煉煙氣中SO2都幾乎沒有回收。而到2007年,全球銅冶煉SO2捕集率均達到90%左右。以方法而論,雙閃法和三菱法,由于實現(xiàn)了連續(xù)吹煉,生產中基本消除了SO2的無組織排放,SO2捕集率均超過99.5%,是SO2,排放量最低的火法煉銅工藝。在造锍熔煉—P-S轉爐吹煉煉銅工藝中,奧圖泰型閃速熔煉由于爐體密封較好,SO2捕集率較高,可以達到99%以上。其他熔池熔煉法,SO2捕集率在98%~99%,但爐體固定的熔池熔煉爐,SO2無組織排放比爐體轉動的稍少。
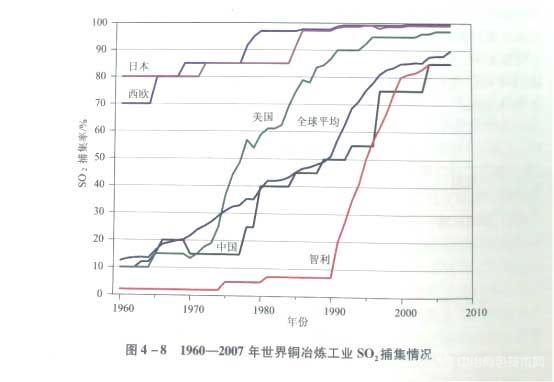