鋅冶煉企業(yè)單位產品能源消耗限額(GB 21249—2014)中規(guī)定現有鋅冶煉企業(yè)單位產品綜合能耗限定值見表5-30。
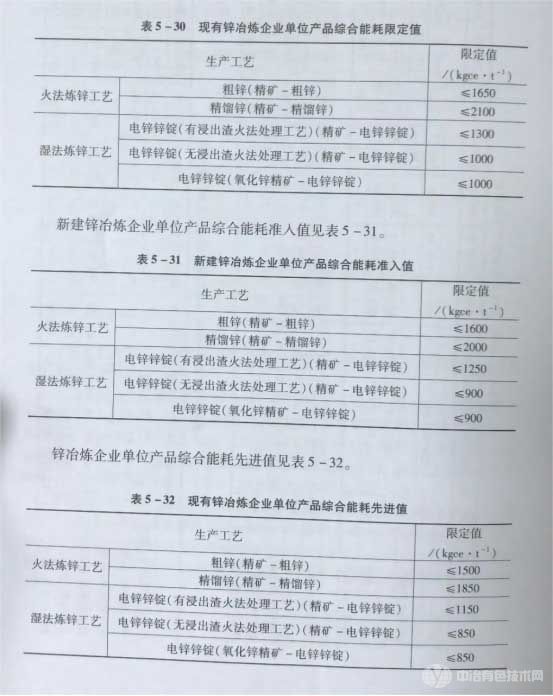
鋅冶煉企業(yè)的產品較為單一,主要包括精鋅、硫酸和溶液凈化的副產品三大類。鋅電積是鋅生產過程的主要耗能工序。
以某采用常規(guī)鋅精礦焙燒—浸出—凈液——電積工藝的鋅冶煉廠為例,不同生產過程的系統(tǒng)能耗分析如下:
備料工序:主要能源消耗為電能和各種爐窯燃料,如表5-33所示,該廠備料工序全年共消耗電能425.78萬kW·h,折合標煤1532.81t,各種爐窯燃料消耗折合標煤2243.87 t。備料工序全年總能耗約0.38萬 tce,其中電能占40.59%。
焙燒工序:能源消耗如表5-34所示,包括各種機械設備電耗3209.19萬kW·h/a,折合標煤11553.08 t;各種燃料消耗10117.14 tce/a、制酸系統(tǒng)能耗6841.92 tce和水耗107.48萬m3/a。焙燒工序全年總能耗約2.90 tce。其中電能占焙燒工序總能耗的40.45%,各種燃料消耗占35.42%,制酸系統(tǒng)占23.96%。
浸出工序:能源消耗如表5-35所示,包括各種槽罐、機械設備的電耗744.65萬kW·h/a,折合標煤2680.74t,浸出渣揮發(fā)窯能耗159476 tce、浸出新水耗9.83萬m3/a,折合標煤4.36 t。浸出工序全年總能耗標煤16.22萬tce。其中,浸出渣揮發(fā)窯能耗占浸出工序總能耗的98.34%。
凈化工序:能耗如表5-36所示,包括鋅粉制備能耗2639 tce/a,各種槽罐、機械設備電耗1117.31萬kW·h/a,折合標煤4022.32t。凈化工序全年總能耗標煤0.67萬t,其中電能消耗占凈化工序總能耗的60.38%。
電積工序:能耗包括析出電鋅直流電耗133466.50萬kW·h/a,折合標煤480479.4 t;電解其他動力消耗2607.92萬kW·h/a,折合標煤9388.51 t。電積工序全年總能耗標煤48.99萬tce。
熔鑄工序:能耗折合標煤0.015 t/t鋅,按該典型工廠2009年鋅產量43.84萬t計,能耗折合標煤6576t。
基于上述計算可知,對應2009年該濕法煉鋅典型工廠43.84萬t鋅產量,其冶煉能源消耗折合標煤如表5-37所示,噸鋅能耗折合標煤1591kg。
在濕法煉鋅工藝過程中,浸出和電積工序能耗是最大的,分別占總能耗的23.25%和70.22%,兩者共占總能耗的93%以上。相對而言,備料、凈化、熔鑄三個工序能耗僅占總能耗的2.43%。因此,在濕法煉鋅生產中,浸出和電積應成
浸出渣揮發(fā)窯能耗占浸出工序總能耗的98.29%,消耗大量碳質燃料,直接排放大量CO,是浸出工序節(jié)能減排的重點所在。應積極開發(fā)低能、高效的浸出渣處理工藝,降低能源消耗,減少CO排放量。
電積工序能耗主要為電能消耗,其中析出電鋅直流電耗占該工序總能耗的99%以上,電解其他動力消耗占比不到1%,因此,電積工序減排的重點在于降低析出電鋅直流電耗。應積極開發(fā)鋅電解過程在線監(jiān)控及節(jié)能降耗優(yōu)化控制系統(tǒng),實時監(jiān)控電解電流、冷卻塔溫度、電解液溫度、地槽液位情況、新液與廢液流量及各生產設備的運行情況,同時優(yōu)化計算各時段的電流密度,合理采用分時供電制度等。
鎂冶煉企業(yè)單位產品能源消耗
鎂冶煉企業(yè)單位產品能源消耗限額(GB 21347——2012)規(guī)定了硅熱法生產能源消耗,現有鎂冶煉企業(yè)單位產品綜合能耗限定值不大于6 tce/t;新建鎂冶煉企業(yè)單位產品綜合能耗準人值不大于5 tce/t;鎂冶煉企業(yè)單位產品綜合能耗先進值不大于4.5 tce/t。
十多年來,我國鎂冶煉工業(yè)通過一系列節(jié)能減排技術的推廣應用,不僅增加了產量,而且使各種技術指標得到了明顯優(yōu)化,原燃料的消耗大幅度降低。表5-38比較了我國硅熱法煉鎂工藝的能耗及CO排放指標的變化。由于鎂冶煉裝備水平的逐年提升,2012年噸鎂平均能耗降到4.6 tce 左右,比2005年節(jié)能40%左右,與2001年比節(jié)能約60%。
2001年,我國原鎂生產普遍直接采用原煤做燃料,噸鎂生產過程中 CO,排放量高達45t;至2004年CO,排放量仍達到32.5t。目前,許多鎂冶煉廠以焦爐煤氣為燃料,噸鎂產量僅排放10.5 t CO。