鋁箔軋制過程中,道次及道次加工率的確定,是制定軋制工藝的重要環(huán)節(jié)。道次及道次加工率的合理與否影響產(chǎn)量及軋機(jī)的生產(chǎn)效率,同時(shí)直接影響產(chǎn)品質(zhì)量,因此,在制定軋制工藝時(shí),必須合理地安排好道次數(shù)及道次加工率,這樣才能保證產(chǎn)品的質(zhì)量要求,提高生產(chǎn)率。原有生產(chǎn)工藝一般采用五個(gè)道次甚至六個(gè)軋制雙零鋁箔,純鋁一般道次加工率是55%左右,合金鋁的道次加工率一般在35%。我公司近來采用四個(gè)道次軋制雙零六鋁箔,并已批量穩(wěn)定生產(chǎn)。純鋁道次加工率提高到了63%左右,成功減少了生產(chǎn)道次。本公司生產(chǎn)工藝的確定是從坯料規(guī)格、軋機(jī)性能、工藝潤滑、冷卻條件、張力范圍、軋輥磨削、軋制速度、操作方法和表面質(zhì)量等方面來實(shí)現(xiàn)的。
1 鋁箔生產(chǎn)裝備
本單位使用當(dāng)前國內(nèi)最先進(jìn)、設(shè)計(jì)寬度最寬的ACHENBACH軋機(jī),軋機(jī)裝配了ACHENBACH先進(jìn)的AGC厚度控制系統(tǒng)、AFC板形自動(dòng)控制控制系統(tǒng)。設(shè)備最大壓下率可達(dá)到70%,為減道次生產(chǎn)提供了基礎(chǔ)。
表一:鋁箔軋機(jī)主要技術(shù)參數(shù)
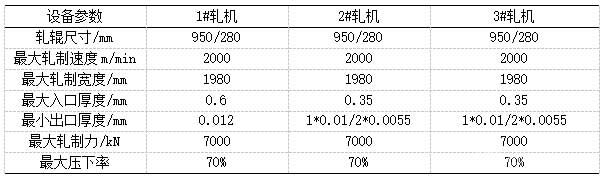
2 坯料選擇及質(zhì)量要求
2.1 鋁箔坯料厚度、寬度、狀態(tài)的選擇
坯料厚度:原五道次軋制雙零鋁箔時(shí)選擇的鋁箔坯料的厚度范圍在0.35mm-0.5mm之間,采用四道次軋制雙零鋁箔時(shí)為避免道次壓下量過大造成表面質(zhì)量缺陷一般采用厚度為0.35mm以下的坯料,本公司采用的厚度為0.28mm。厚度公差一般要求控制在厚度的±3%以內(nèi),要求嚴(yán)格的甚至控制在厚度的±2%以內(nèi)。
坯料寬度:坯料寬度是根據(jù)軋機(jī)最大軋制寬度、設(shè)備能力和成品規(guī)格,且考慮切邊量來確定的。根據(jù)軋機(jī)的技術(shù)參數(shù)本公司的最大入口寬度為1980mm。寬度公差一般要求控制在±2mm以內(nèi),要求嚴(yán)格的應(yīng)為±1.0mm。
坯料重量:坯料的重量主要取決于設(shè)備的機(jī)械化程度和結(jié)構(gòu)性能。卷重越大,生產(chǎn)率越高幾何廢料減少,因此提高卷重量是提高產(chǎn)量、降低成本的有效措施。本公司的最大軋制重量12870kg。
坯料性能:鋁箔坯料狀態(tài)分為軟狀態(tài)、半硬狀態(tài)、和全硬狀態(tài)三種,鋁箔毛料的力學(xué)性能應(yīng)符合下列要求:
H18狀態(tài),αb≥150MPa,δ≥2%;
H14狀態(tài),αb≥110MPa,δ≥3%。
2.2 坯料的冶金質(zhì)量
用于生產(chǎn)鋁箔坯料的熔體要有高的金屬純潔度,熔體含渣、含氣量要低,熔體精練后氫含量必須控制在0.12mL/(100g鋁)以下,生產(chǎn)的鑄軋坯料不產(chǎn)生氣道、夾渣等內(nèi)部質(zhì)量缺陷,晶粒度達(dá)到一級(jí)。
2.3 坯料的表面質(zhì)量
毛料表面質(zhì)量直接影響到鋁箔的表面質(zhì)量。坯料的表面質(zhì)量加以嚴(yán)格控制,表面要潔凈、平整、無腐蝕,表面不允許有油斑、孔洞、金屬和非金屬壓入物、暗紋、擦劃傷等缺陷。
2.4 坯料的板形質(zhì)量
對(duì)鋁箔毛料的板形要求控制在15I以內(nèi)。不允許有兩邊松或兩邊緊、兩肋松或兩肋緊、中間松等不良板形。板形的理想狀態(tài)應(yīng)為拋物線狀,中凸度要求控制在厚度的1%以內(nèi)。
2.5 鋁箔毛料的技術(shù)標(biāo)準(zhǔn)要求
鋁箔毛料的技術(shù)標(biāo)準(zhǔn)應(yīng)涵蓋以下12個(gè)方面的內(nèi)容:合金與狀態(tài),卷材尺寸與公差,化學(xué)成分,性能與組織,表面粗糙度,平直度,凸面率,內(nèi)、外部質(zhì)量,端面質(zhì)量,包裝要求,質(zhì)量證明書和其他要求等。作為技術(shù)標(biāo)準(zhǔn),每項(xiàng)內(nèi)容應(yīng)有具體的技術(shù)要求.
3 生產(chǎn)過程控制
3.1 道次加工率:
原鋁箔軋制道次加工率一般控制在50%~60%,減道次后鋁箔道次加工率一般在60%以上。軋制壓下量的分配按道次加工率逐步上升的原則。減道次后與原軋制加工率對(duì)如表二表三,
表二:五道次雙零鋁箔的軋制加工率
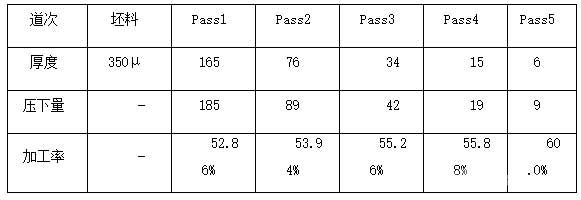
表三:減道次后的鋁箔加工率
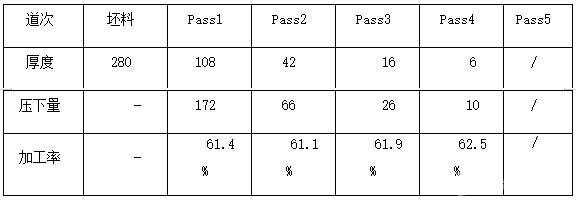
軋制力:對(duì)于厚度0.05mm以上的箔材能起到主要壓下作用,因減道次生產(chǎn)時(shí)壓下量較大,為保證其他工藝參數(shù)平衡,因此軋制力的使用也較大。
軋制速度:軋制速度是軋機(jī)和軋制技術(shù)先進(jìn)程度的主要標(biāo)志,鋁箔軋機(jī)的發(fā)展方向,就是高速軋制,以獲得高的生產(chǎn)率,但減道次生產(chǎn)時(shí),前兩道絕對(duì)壓下量大,變形熱和摩擦熱較大,如果軋制速度過快極易產(chǎn)生起鼓。
后張力:后張力應(yīng)控制較小,避免對(duì)鋁箔內(nèi)部組織塑性的破壞,有利于針孔的減少。
軋制油溫:為保證軋制油的冷卻能力、控制好版型,防止軋制起鼓要控制好軋制油溫度。
版型曲線:軋制過程I值特別是前4道次I值的設(shè)定一與控制,不僅受到坯料的影響,而且如果板形控制不好,直接會(huì)導(dǎo)致在成品道次軋制過程中出現(xiàn)起皺、起棱等現(xiàn)象。具體方案見下表四:
表四:0.006mm鋁箔軋制工藝
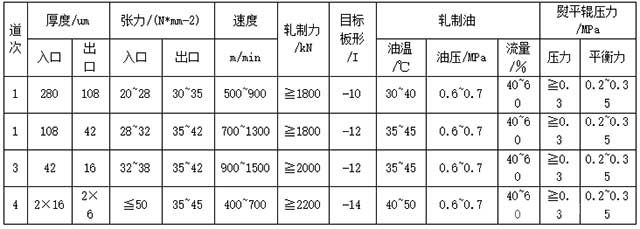
3.3 軋制油的選擇與管理
在箔材軋制中,軋制油除了起冷卻、潤滑作用外,其抗壓性對(duì)箔材的軋制壓下量有很大的影響,在一般的情況下潤滑油的抗壓性好,道次加工率大,否則道次加工率將減少。
本廠粗、精軋同時(shí)選用了一種低粘度的基礎(chǔ)油MOA-80,通過調(diào)整添加劑的含量來滿足粗、精軋不同的工藝要求。這樣做從軋制油的管理上比較方便。所選基礎(chǔ)油指標(biāo)如下表五:
表五:基礎(chǔ)油指標(biāo)
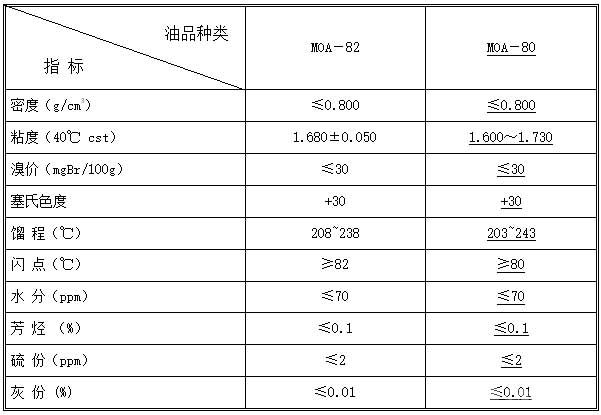
軋制油添加劑主要使用的是酯、醇添加少量酸,從而使軋制油達(dá)到最佳效果。因四道次出雙零成品所采用的道次壓下量較大,所以添加劑含量較五道次軋制時(shí)含量高。醇的添加量一般為基礎(chǔ)油量的2%~5%,酯的添加量為基礎(chǔ)油量的1%~3%。當(dāng)酯含量過低時(shí),則在軋制時(shí)會(huì)發(fā)生壓不下的現(xiàn)象;而過高時(shí)退火后易產(chǎn)生油斑。具體軋制油使用指標(biāo)見下表六:
表六:軋制油控制指標(biāo)
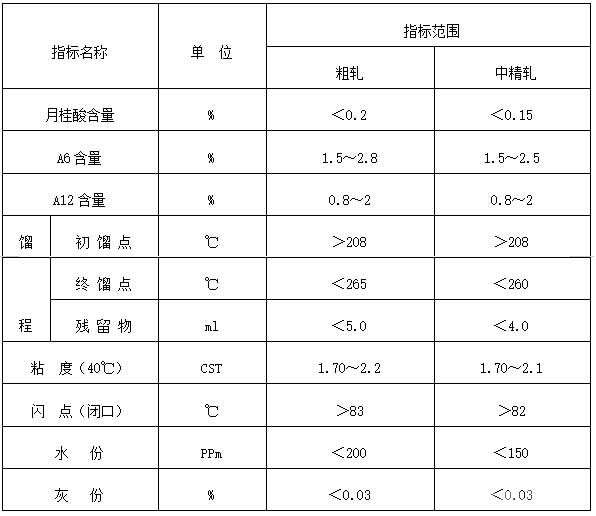
3.4 軋輥管理
軋輥是軋制工藝的重要一環(huán),軋輥質(zhì)量穩(wěn)定是軋制穩(wěn)定的基礎(chǔ)。主要工藝
參數(shù)是軋輥凸度與表面粗糙度的控制,本廠減道次軋制時(shí)軋輥磨削工藝如表七:
表七:軋輥磨削工藝參數(shù)
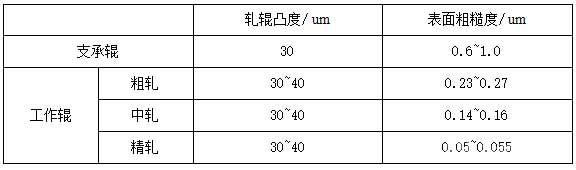
3.5 中間退火
中間退火主要是為了消除加工硬化。熱軋鋁箔坯料從750μ軋制到15μ,總加工率已經(jīng)達(dá)到98%,抗拉強(qiáng)度達(dá)到180MPa左右。這樣,在成品軋制過程,減薄相對(duì)困難,經(jīng)常發(fā)生打滑。
中間退火的另外一項(xiàng)主要任務(wù)是減少成品的針孔。經(jīng)驗(yàn)數(shù)據(jù)表明,熱軋坯料軋制雙零鋁箔,中間退火以后軋制針孔成倍減少。
所以中間退火一般安排在成品道次之前,使鋁箔機(jī)械性能從160~180MPa降低到120~140MPa。因?yàn)榕髁虾穸冗x擇有所不同,四道次生產(chǎn)比五道次軋制總加工率略低,加之四道次生產(chǎn)時(shí)變形區(qū)溫度高,降低了鋁箔的加工硬化程度,因此中間退火溫度比五道次生產(chǎn)時(shí)略低。
中間退火工藝:165℃×8~18h。
4 常見問題及解決措施
4.1 板形控制
減道次后隨著道次加工率的上升,變形區(qū)內(nèi)的變形熱急劇增加,超出軋制油的冷卻能力,使局部版型惡化,造成版型不良。因?yàn)檐堉七^程中工作輥輥型的變化主要來源于溫度的干擾,其中軋材產(chǎn)生的變形熱是使軋輥溫度上升的主要原因,為了獲得良好的板形,必須對(duì)輥型的變化給予及時(shí)有效地糾正,
原始輥型的設(shè)計(jì)不可能完全適應(yīng)不同規(guī)格。軋輥的凸度與來料板帶的板凸度不能完全相匹配,容易早成版型不良,打底廢料。因此換新輥后軋制前軋輥預(yù)熱很重要。但傳統(tǒng)的熱輥方式很難達(dá)到理想的效果,而且熱輥時(shí)間較長,造成成品率損失,制約生產(chǎn)效率。通過分段冷卻熱輥的方式可以有效的解決,即開機(jī)軋制前應(yīng)根據(jù)工作經(jīng)驗(yàn)對(duì)出口版型進(jìn)行預(yù)判,例如寬幅鋁箔軋制時(shí)版型容易出現(xiàn)小邊緊肋部松中間松,熱輥時(shí)可對(duì)應(yīng)出口的預(yù)判版型將軋制油油嘴分段開啟控制流量大小控制輥型,使輥型接近軋制時(shí)的熱凸度。這樣可以有效提高打底質(zhì)量和版型質(zhì)量。
4.2 軋制起鼓
鋁箔軋制過程中,特別是減道次生產(chǎn)時(shí)將會(huì)產(chǎn)生大量的變形熱和摩擦熱.使軋制變形區(qū)始終處于受熱狀態(tài)。如果變形區(qū)的軋輥局部溫度過高。超出了軋制冷卻油的最大沖冷卻能力,使該處的熱膨脹變大,則與之對(duì)應(yīng)該處出口鋁箔變松,如在鋁箔卷取過程中無法將其展平。則該處卷取后的孔隙率比平整處的大,累積后就形成起鼓,也稱為熱鼓,
鋁箔熱鼓問題具體措施為:根據(jù)出口側(cè)打底時(shí)的板形情況及時(shí)調(diào)整軋輥凸度,保證打底的質(zhì)量和正常軋制時(shí)的板形控制;板形參數(shù)的設(shè)汁必須保證出口板形平整同時(shí)保證中部比邊部略緊,即保持一定中高,還要考慮道次間板形參數(shù)的合理過渡;應(yīng)定期檢查噴嘴的噴射效果,及時(shí)停機(jī)檢查軋制油嘴工作情況;一般軋制油的配制按照高油膜強(qiáng)度、低粘度、低油斑傾向的原則,配制過程中嚴(yán)格控制好軋制油的各項(xiàng)性能參數(shù);更換清輥器膠片或更換支承輥后必須檢查清輥器膠片與支撐輥的壓靠輥是否正常,同時(shí)調(diào)整好清輥器壓力;注意觀察料面的質(zhì)量情況;應(yīng)根據(jù)來料性質(zhì)和設(shè)備的冷卻能力合理分配好道次壓下率。在具體原因未明確之前,為防止批量廢品出現(xiàn),一般都先采用降溫、降速的方法來進(jìn)行生產(chǎn)。
4.3 針孔控制
由于四道次軋制雙零鋁箔壓下量大大增加,因此對(duì)應(yīng)使用的軋制工藝參數(shù)較大,出現(xiàn)針孔的幾率也就大為增加。因此,除了坯料的質(zhì)量需要確保之外,在生產(chǎn)過程中要特別注意以下方面:
四道次生產(chǎn)雙零鋁箔是,軋制速度和后張力的控制應(yīng)結(jié)合軋輥表面粗糙度和軋制油的性能進(jìn)行調(diào)整。特別是在軋制成品的前一道次和成品道次軋制速度和后張力的控制是否合適對(duì)針孔影響最大。實(shí)踐證明軋制速度太快或后張力太大針孔數(shù)明顯增多,速度太慢或后張力太小又影響生產(chǎn)效率甚至造成鋁箔出現(xiàn)皺褶、開縫等。因此要合理控制速度和張力,我們的工藝要求正常軋制時(shí)速度不大于600m/min,后張力不大于65N/mm2 .
軋制油的潔凈度越高越好,針孔數(shù)越少。因此,要合理調(diào)配硅藻土與活性白土的比例,定期清洗過濾器,并有專人管理,保證軋制的過濾系統(tǒng)必須良好運(yùn)行。
對(duì)軋輥表面粗糙度要求特別嚴(yán)格,如果軋輥表面粗糙度太高,則軋制速度較快,針孔增多且表面光亮度低, 為保證穩(wěn)定性和質(zhì)量、降低針孔。應(yīng)保證工藝要求的粗糙度參數(shù)。
5 成果分析
5.1 質(zhì)量情況
通過改變道次壓下量、控制油溫、一二道次交叉軋制、篩選軋輥、沖洗軋輥及加大基礎(chǔ)潤滑油等方式解決了高速軋制時(shí)的熱鼓、二道次斜紋問題,避免了很容易出現(xiàn)的表面質(zhì)量、板形不良等問題。通過控制工藝參數(shù)和采取其他控制針孔措施,0.006mm鋁箔針孔數(shù)均小于1000個(gè)/㎡,最少控制在200個(gè)/㎡。針孔在卷面邊部較多,有少量密集成行針孔。由于斷帶較少,生產(chǎn)情況穩(wěn)定,加上固定的幾何切邊、每道次料頭及料尾扒料,成材率較高,軋制綜合成品率在95%以上。
5.2 提高了生產(chǎn)效率
對(duì)于四個(gè)道次生產(chǎn)雙零鋁箔最大的優(yōu)勢是極大提高生產(chǎn)效率,降低生產(chǎn)成本。通過初步統(tǒng)計(jì)工藝由原來五道次改為四個(gè)道次出成品后,生產(chǎn)效率提高了15%以上,以本廠3臺(tái)鋁箔軋機(jī)為例,原設(shè)計(jì)年產(chǎn)量為20000噸,減道次后理論計(jì)算年產(chǎn)量可達(dá)到25000噸。同時(shí)大幅降低了單位輔材的消耗,降低了成本。
6 結(jié)束語
通過對(duì)優(yōu)化選擇坯料,尤其是在不增加原料成本情況下,合理定制坯料厚度,合理制定道次壓下率、優(yōu)化調(diào)配添加劑、優(yōu)化工藝參數(shù)、以及對(duì)板型和表面質(zhì)量等關(guān)鍵因素的控制,成功實(shí)現(xiàn)四道次軋制出0.006㎜優(yōu)質(zhì)鋁箔,極大提高了生產(chǎn)效率,有效降低了生產(chǎn)成本。為企業(yè)的良性發(fā)展和擴(kuò)大市場競爭力奠定了堅(jiān)實(shí)基礎(chǔ)。
參考文獻(xiàn)
[1]潘復(fù)生,張靜,等。鋁箔材料[M].北京:化學(xué)工業(yè)出版社,2005
[2]王祝堂,田榮章。鋁合金及其加工手冊[M].長沙:中南大學(xué)出版社,2005
聲明:
“四個(gè)道次生產(chǎn)雙零鋁箔軋制工藝淺析” 該技術(shù)專利(論文)所有權(quán)利歸屬于技術(shù)(論文)所有人。僅供學(xué)習(xí)研究,如用于商業(yè)用途,請(qǐng)聯(lián)系該技術(shù)所有人。
我是此專利(論文)的發(fā)明人(作者)