肯尼科特-奧圖泰連續(xù)吹煉
1)方法簡(jiǎn)介
美國肯尼科特銅公司Garfield煉銅廠原采用P-S轉(zhuǎn)爐工藝生產(chǎn),為滿足美國猶他州日趨嚴(yán)格的環(huán)保標(biāo)準(zhǔn),以及降低生產(chǎn)成本,20世紀(jì)70年代末提出了“固體銅锍氧化連續(xù)吹煉”專利,開展了實(shí)驗(yàn)。20世紀(jì)80年代中期,與在閃速爐熔煉技術(shù)上具有優(yōu)勢(shì)的奧圖泰公司合作,共同進(jìn)行閃速吹煉技術(shù)研發(fā)及推廣,在奧圖泰公司Pori研發(fā)中心進(jìn)行的半工業(yè)試驗(yàn)取得了很好的結(jié)果,在此基礎(chǔ)上,1995年Garfield煉銅廠建成閃速吹煉系統(tǒng),取代P-S轉(zhuǎn)爐吹煉。因此,目前這一技術(shù)為肯尼科特公司與奧圖泰公司共有,稱之為肯尼科特-奧圖泰閃速吹煉。
閃速吹煉爐與閃速熔煉爐結(jié)構(gòu)大致相同,只是爐體規(guī)格要小得多,但由于粗銅比重大、浮力強(qiáng),以及鐵酸鈣爐渣腐蝕性強(qiáng)等原因,在爐體結(jié)構(gòu)細(xì)節(jié)上,如冷卻水套、爐襯,特別是爐底結(jié)構(gòu)等方面,進(jìn)行了許多改進(jìn)。Garfield煉銅廠閃速吹煉爐前期爐壽命較短,其間發(fā)生過2次跑銅事故,通過不斷改進(jìn),從第6爐期開始,爐壽命提高至5年以上,祥光銅業(yè)第1爐期爐壽命即達(dá)3.5年。預(yù)期今后爐壽命完全可能達(dá)到7~10年。
圖3-33為閃速吹煉爐示意圖。我國已投產(chǎn)的2座閃速吹煉爐,產(chǎn)能均按40萬tCu/a設(shè)計(jì),其規(guī)格略有不同。祥光銅業(yè)閃速吹煉爐內(nèi)部尺寸為:反應(yīng)塔直徑4.3m,高6m,池中心距11.6m。銅陵金冠銅業(yè)閃速吹煉爐內(nèi)部尺寸為:反應(yīng)塔直徑5m,高7m,沉淀池長21.8m,寬6.7m,高2.1m。
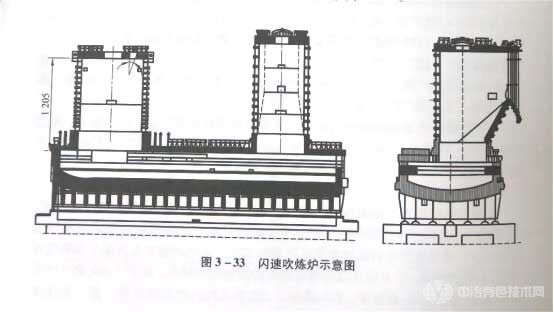
圖3-33 閃速吹煉爐示意圖
圖3-34所示為雙閃法煉銅工藝原則流程圖??夏峥铺?奧圖泰閃速吹煉(以下簡(jiǎn)稱閃速吹煉)除可以與奧圖泰閃速熔煉配套外,也可與其他能產(chǎn)出70%左右高品位銅锍的任何熔煉方法結(jié)合,由于其處理能力強(qiáng),今后甚至可以將異地多個(gè)廠家產(chǎn)出的高品位銅锍,匯集在一座閃速吹煉爐處理,這點(diǎn)是閃速吹煉相較于三菱法吹煉較大的優(yōu)勢(shì)所在。
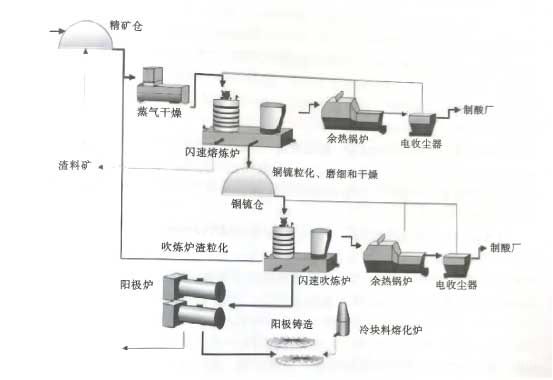
圖3-34 閃速熔煉一肯尼科特-奧圖泰閃速吹煉工藝
熔煉爐產(chǎn)出的銅锍,品位控制在67%~72%,SiO含量控制在小于0.5%,水淬后磨細(xì)干燥至粒度為48μm左右,水分小于0.3%,氣動(dòng)輸運(yùn)到爐頂料倉。然后,通過噴嘴將其與熔劑石灰和少量石英砂、吹煉煙塵及80%左右的富氧空氣一并噴灑進(jìn)入反應(yīng)塔中,在1400℃左右高溫下,發(fā)生銅锍吹煉的物理化學(xué)反應(yīng),生成粗銅(Cu 99%,S 0.3%)、鐵酸鈣爐渣(Cu 20%,Ca0/Fe 0.37,F(xiàn)e,0.30%,SiO2.5%)及SO煙氣(SO40%,煙塵率5%,煙塵95%為硫酸鹽),這一反應(yīng)過程可能持續(xù)到熔池中才結(jié)束。粗銅和爐渣熔體在沉淀池中沉淀分離,分別定期從排銅口和排渣口排出。粗銅通過流槽排放至回轉(zhuǎn)式陽極爐中火法精煉。爐渣通過流槽排出后水淬,水淬渣干燥磨細(xì)后輸送至熔煉系統(tǒng)處理。煙氣與煙塵經(jīng)直升煙道進(jìn)入余熱鍋爐回收余熱,再經(jīng)電收塵、濕式洗滌、電除霧后進(jìn)入制酸系統(tǒng)。
與三菱法相同,閃速吹煉也采用CaO溶劑,造鐵酸鈣爐渣。這一爐渣體系有下列優(yōu)點(diǎn):①對(duì)FeO溶解能力強(qiáng),熔點(diǎn)低,在粗銅含S0.3%,渣含Cu20%的情況下,爐渣可正常放出;②CuO在其中的活度系數(shù)小,渣含銅較鐵橄欖石爐渣低;③對(duì)砷、銻等雜質(zhì)脫除能力強(qiáng),但脫鉛鉍能力較低。鐵酸鈣爐渣體系對(duì)SiO,溶解度極小,當(dāng)其中SiO含量超過5%,即可能過飽和析出,因此,對(duì)銅锍中夾帶的SiO,應(yīng)嚴(yán)格控制,不能超過0.5%,在P-S轉(zhuǎn)爐吹煉中,則不存在這一問題。但由于鐵酸鈣爐渣對(duì)爐襯腐蝕性強(qiáng)、流動(dòng)性好,因此,為了不致過分沖刷爐襯,以及達(dá)到對(duì)爐襯掛渣保護(hù)的要求,對(duì)其中Fe,O的量和過飽和度也應(yīng)控制恰當(dāng)。正常吹煉中,除通過調(diào)節(jié)料/O,比控制粗銅含S外,還要控制渣中Ca/Fe比在0.3 ~0.45(一般為0.37),SiO,含量在2.5%,這樣,渣中Fe,O么大致在30%,就既能保證爐渣有足夠的流動(dòng)性,能夠從爐內(nèi)正常放出,而流動(dòng)性又不至于太高,過分沖刷爐襯,同時(shí)還能對(duì)爐襯掛渣保護(hù)。
閃速吹煉生產(chǎn)中,應(yīng)對(duì)渣型、粗銅質(zhì)量、渣溫實(shí)現(xiàn)穩(wěn)定控制。銅锍、爐渣、粗銅成分定期取樣快速測(cè)定,渣溫測(cè)定以沉淀池頂溫度為準(zhǔn),每小時(shí)測(cè)定1次。將這些測(cè)定數(shù)據(jù)輸入計(jì)算機(jī),根據(jù)控制模型計(jì)算結(jié)果對(duì)相關(guān)工藝參數(shù)進(jìn)行自動(dòng)調(diào)控,以使過程穩(wěn)定進(jìn)行。
渣含銅控制目標(biāo)值為20%。生產(chǎn)實(shí)踐表明,渣含銅與粗銅含S大致成反比,在渣含Cu20%時(shí),粗銅含S為0.3%,含0為0.35%。渣含銅主要通過調(diào)節(jié)氧系數(shù)(0/銅锍)控制。每2h取1次干燥銅锍樣化驗(yàn)為反饋控制提供依據(jù),每1h 由沉淀池頂取棒渣樣,為反饋控制提供依據(jù)。爐渣m(CaO)/m(Fe)比控制在0.3~0.45,正常目標(biāo)值為0.37,通過調(diào)節(jié)溶劑Ca0加入量控制。操作經(jīng)驗(yàn)表明,CaO/Fe比大于0.45,CaSO&會(huì)在沉淀池表面結(jié)殼;小于0.3,F(xiàn)e,O.會(huì)過飽和析出沉淀,隨粗銅排出,黏結(jié)在粗銅流槽和陽極爐內(nèi)。渣中Fe。O么含量與爐渣含銅、CaO/Fe比、SiO含量等相關(guān),控制渣含銅20%,m(Ca0)/m(Fe)比0.37,SiO,含量2.5%時(shí),渣中FeO含量為30%。渣中SiO含量控制在約2.5%,通過調(diào)節(jié)溶劑SiO,的加入量控制。爐渣中少量SiO存在,可調(diào)節(jié)爐渣流動(dòng)性及FeO的飽和程度,提高爐襯壽命。粗銅質(zhì)量主要是控制其中的S含量,目標(biāo)值為0.3%,通過調(diào)節(jié)氧系數(shù)控制。從原理上講,氧系數(shù)是根據(jù)物料平衡計(jì)算確定的,因此,與銅锍品位、煙塵返回與否及其成分等有關(guān)。粗銅中As、Sb、Bi、Pb等雜質(zhì)含量,主要與原料成分、煙塵返回走向等有關(guān)。Garfield煉銅廠實(shí)踐表明,在銅精礦雜質(zhì)含量偏高,煙塵直接返回的情況下,粗銅中雜質(zhì)含量有增高的趨勢(shì),說明雜質(zhì)元素在系統(tǒng)中有循環(huán)累積,此時(shí),應(yīng)對(duì)部分高含雜煙塵采用濕法處理,使部分有害雜質(zhì)開路。目標(biāo)渣溫為1270±20℃,目標(biāo)銅锍溫度為1250℃,允許在1240~1270℃范圍內(nèi)波動(dòng),通過調(diào)節(jié)煙塵加入量和富氧濃度控制。
2)技術(shù)特點(diǎn)
①以CaO為熔劑,造鐵酸鈣爐渣,降低形成泡沫渣的風(fēng)險(xiǎn),較之鐵橄欖石渣型,該爐渣含銅低,對(duì)砷、銻等雜質(zhì)脫除能力強(qiáng),但脫鉛率低。
②閃速吹煉中,爐膛內(nèi)只有粗銅和爐渣兩個(gè)熔體相,粗銅含S0.3%左右。③環(huán)保。消除了P-S轉(zhuǎn)爐爐口SO泄露及銅锍、粗銅包子吊運(yùn)中SO的逸散,煙氣量及SO濃度的穩(wěn)定有利于制酸,硫捕集率高,生產(chǎn)現(xiàn)場(chǎng)環(huán)境好。Garfield煉銅廠1999年硫捕集率達(dá)到99.9%,每生產(chǎn)1t銅SO排放量小于2kg,該廠1998年P(guān)M10總排放量234 t,僅為政府限定允許排放量的56%。
④閃速吹煉處理冷態(tài)固體銅锍,可與任何能產(chǎn)出70%左右高品位銅锍的熔煉工藝配套使用,而且可將多座熔煉爐產(chǎn)出的銅锍集中在1座吹煉爐中處理。
⑤投資及運(yùn)行費(fèi)用低。對(duì)年產(chǎn)30~40萬t的煉銅廠,采用閃速吹煉,在投資和運(yùn)行成本方面,可降低20%左右。這主要?dú)w因于以下幾點(diǎn):第一是1臺(tái)吹煉爐可取代4~5臺(tái)P-S轉(zhuǎn)爐;第二是閃速吹煉煙氣量小,SO濃度高,流量及濃度穩(wěn)定,使得余熱回收、除塵及制酸系統(tǒng)投資及運(yùn)行成本大幅度降低。第三是爐體壽命長,耐火材料消耗低。
⑥雙閃法是目前能耗最低的煉銅方法之一。與三菱法比較,能耗更低。⑦閃速吹煉銅锍需要水淬磨細(xì)干燥,不僅不能利用其熱量,還要額外耗能。⑧閃速吹煉不能處理塊狀冷料,如殘陽極、流槽結(jié)殼等。
3)技術(shù)指標(biāo)
①富氧濃度:常溫,80%0;
②銅锍品位:69%~71%;
③爐渣CaO/Fe比:0.33~0.39;
④爐渣SiO含量:1.5%~2.5%;
⑤粗銅成分:Cu98.5%~99.3%,S0.3%,00.25%;
⑥爐渣成分:Cu20%,F(xiàn)e030%;
⑦煙氣SO濃度:30%~40%;
⑧煙塵率:8%~9%;
⑨粗銅溫度:1230~1270℃;
⑩爐渣溫度:1250~1290℃。
4)國內(nèi)外應(yīng)用情況
到目前為止,世界上已有4座閃速吹煉爐建成投產(chǎn),這些閃速吹煉爐均與閃速熔煉配套使用,即所謂雙閃法煉銅。世界首座閃速吹煉爐1995年在美國肯尼科特公司Garfield煉銅廠建成,規(guī)模為年產(chǎn)銅30萬t,一次投產(chǎn)成功并很快達(dá)產(chǎn),初期存在爐體壽命短等問題,經(jīng)改進(jìn)爐體壽命已提高至5年以上。該廠閃速吹煉工藝已運(yùn)行18年,標(biāo)志著閃速吹煉技術(shù)已較為成熟。其余幾座閃速吹煉爐都在我國。2007年,山東祥光銅業(yè)公司雙閃法系統(tǒng)建成投產(chǎn),規(guī)模為年產(chǎn)銅40萬t,一期20萬t,該廠整合了多項(xiàng)先進(jìn)工藝和裝備,是世界上最先進(jìn)的煉銅企業(yè)之一。
2011年,達(dá)到年產(chǎn)40萬t銅規(guī)模。2012年,銅陵有色金屬公司金冠銅業(yè)公司建成一套雙閃法系統(tǒng)投人生產(chǎn),規(guī)模為年產(chǎn)銅40萬t。金川有色金屬公司在廣西防城港建設(shè)一套年產(chǎn)40萬t銅的雙閃法系統(tǒng),2013年建成投產(chǎn)。
5)總體評(píng)價(jià)
閃速吹煉的發(fā)明及推廣應(yīng)用,是煉銅技術(shù)發(fā)展的一個(gè)重大成就。自20世紀(jì)后半葉開始,一系列先進(jìn)的火法煉銅熔煉技術(shù)逐步取代了鼓風(fēng)爐、反射爐和電爐,使得過程得以強(qiáng)化,實(shí)現(xiàn)了高效、節(jié)能、低污染。相比較而言,吹煉技術(shù)的進(jìn)步相對(duì)滯后。傳統(tǒng)的P-S轉(zhuǎn)爐吹煉,由于效率低、設(shè)備臺(tái)數(shù)多、間斷操作、SO,泄漏及逸散問題難以徹底解決,已成為火法煉銅技術(shù)進(jìn)一步向高效節(jié)能、環(huán)保清潔方向發(fā)展的制約環(huán)節(jié),長期以來,冶金工作者一直致力于連續(xù)煉銅、連續(xù)吹煉技術(shù)的研發(fā),但截至目前,僅有三菱法和閃速吹煉得到推廣應(yīng)用。而三菱法吹煉由于與其他熔煉方法配套存在一些問題,加之其能耗偏高,難以廣泛推廣應(yīng)用。因此,可以預(yù)期,P-S轉(zhuǎn)爐吹煉將逐步為閃速吹煉所取代,但由于銅冶煉項(xiàng)目投資巨大等原因,這一過程將很漫長。