引 言
摻雜鎢條的特性對鎢絲的高溫性能及加工性能有很大的影響。在一定范圍內(nèi)隨著鎢絲鉀含量提高,絲材高溫性能得到改善,但是隨著鎢粉鉀含量的提高,在鎢坯高溫?zé)Y(jié)過程中就容易產(chǎn)生塊狀晶粒甚至環(huán)形框晶的不良燒結(jié)組織。而這些不良燒結(jié)組織由于塊晶的晶界強度較低,會使這種鎢坯條的加工性能惡化[1],在壓力加工過程中會出現(xiàn)諸如成品率偏低、鎢桿探傷檢測裂紋率偏高等問題。因此制取具有適當鉀含量,比重及均勻晶粒結(jié)構(gòu)的摻雜鎢條顯得極為重要。
圖1是有環(huán)形框晶問題的垂熔鎢坯條加工到8.9mm的桿料表面照片,可以看到有很嚴重的橫向裂紋問題,這種情況會使得整根鎢材全部報廢,造成很大的經(jīng)濟損失。從這我們可以看出環(huán)形框晶的燒結(jié)組織對鎢坯條的壓力加工會造成無可挽回的影響。
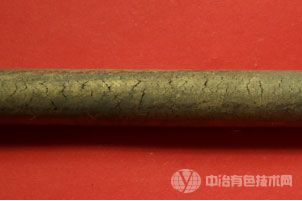
圖1. 環(huán)形框晶坯條的8.9mm桿料表面
我們希望通過對整個高溫?zé)Y(jié)過程不同階段的金相組織和鉀含量變化的研究,了解鎢坯條產(chǎn)生環(huán)形框晶的機理,從中尋找解決高鉀鎢粉高溫?zé)Y(jié)避免產(chǎn)生大晶或框晶的方法,使我們在獲得優(yōu)越高溫性能的同時又可以避免類似環(huán)形框晶的不良燒結(jié)組織的出現(xiàn)。
摻雜粗鎢絲的原料為仲鎢酸氨(俗稱APT),APT通入氮氣和氫氣的混合氣體加熱還原成藍色氧化鎢,依據(jù)生產(chǎn)要求配好附加劑,往藍鎢中依次摻入一定量的K2SiO3 和Al(NO3)3溶液[2],產(chǎn)出的摻雜藍鎢通氫加熱還原成摻雜鎢粉,將摻雜鎢粉按粒度需求組批后加入鹽酸、氫氟酸進行酸洗,以除去多余的大量附加劑,再把不同粒度的摻雜鎢粉搭配混粉后使用冷等靜壓技術(shù)把摻雜鎢粉壓制成直徑Φ20mm、根重3kg的鎢圓棒,將鎢圓棒在預(yù)燒爐內(nèi)進行通氫低溫?zé)Y(jié),制成使之具有一定強度的鎢坯條,然后在氫氣保護下通電進行垂熔高溫?zé)Y(jié)制成摻雜鎢條。
垂熔高溫?zé)Y(jié)是一個比較復(fù)雜的物理化學(xué)過程,是從鎢粉性能轉(zhuǎn)變?yōu)橹旅苕u材性能的重要工序。垂熔高溫?zé)Y(jié)過程中鎢壓坯的物理機械性能和幾何尺寸會發(fā)生顯著變化,一般表現(xiàn)出坯條各方向收縮、密度提高和硬度增加,向致密體材料接近。鎢坯的這種變化,是由于多孔體壓坯在加熱燒結(jié)過程中發(fā)生一系列的物理和化學(xué)變化的結(jié)果,即在高溫?zé)Y(jié)過程中發(fā)生粘結(jié)、流動、擴散(表面擴散、體積擴散和晶界擴散等)、蒸發(fā)凝結(jié)、蠕變(或塑性流動)和再結(jié)晶過程所引起的。
在垂熔高溫?zé)Y(jié)過程中所發(fā)生的收縮(線收縮、面收縮和體積收縮)和顆粒長大現(xiàn)象,都是因為在燒結(jié)溫度下,原子具有較高的活動性所造成的[1~4]。晶體晶格中的原子具有一定的振幅,它隨溫度升高而增大。位于表面原子的能量和振幅與晶格內(nèi)部原子是不同的,表面原子的自由能量過剩,它力圖減少表面張力。當溫度升高時,表面原子的活化能增大,這些原子將從凸出地方向凹陷地方遷移,即從不穩(wěn)定狀態(tài)向穩(wěn)定狀態(tài)移動。原子表面遷移過程導(dǎo)致顆粒表面拉平和孔隙球形化,顆粒間的接觸面積增大。
對燒結(jié)過程影響較大的熱力學(xué)數(shù)據(jù)是與總的孔隙表面積有關(guān)的表面能,對大多數(shù)研究來說,是不能輕視總的孔隙表面積這個參數(shù)的,因為它在熱力學(xué)上起著重要的作用。
研究發(fā)現(xiàn),燒結(jié)過程中的孔隙表面積F與空穴體積V可以由下面的四個階段表征:
⑴、燒結(jié)過程第一階段:
低溫?zé)Y(jié)坯條中的鎢粉顆粒之間發(fā)生粘結(jié),顆粒之間形成了“燒結(jié)頸”,壓坯之間的強度和硬度顯著增加,但坯條的孔隙表面積F的總量沒有明顯的下降,也就是說,壓坯并沒有顯著的收縮和形狀變化。該階段的加熱過程受快速短程過程控制。
⑵、燒結(jié)過程第二階段:
形成的“燒結(jié)頸”隨著溫度的提高而長大,這就需要燒結(jié)坯中鎢顆粒發(fā)生遷移。在近似穩(wěn)定的空穴體積V值下,孔隙表面積F值急劇減小。這一燒結(jié)階段表現(xiàn)為很小的空穴消失,使總的空穴體積V下降不明顯,而可能產(chǎn)生光滑和圓的空穴表面。壓坯并沒有顯著的收縮和形狀變化。該階段摻雜鎢坯條中摻雜的Si、Al、K氧化物開始大量揮發(fā)。
⑶、燒結(jié)過程第三階段:
在此階段孔隙仍然開口的,孔隙表面積F與空穴體積V呈直線的關(guān)系,此時由于空穴的消失及無空穴粗化現(xiàn)象而使孔隙表面積減少,空穴平均半徑維持R=V/F的穩(wěn)定值。通過空穴向外擴散作用而引起孔隙收縮,使得壓坯有顯著的收縮和形狀變化。該階段摻雜鎢坯條中摻雜的Si、Al、K氧化物繼續(xù)揮發(fā)。
⑷、燒結(jié)過程第四階段:
在此階段大多數(shù)的孔隙已被封閉(空穴體積約為0.1%)[5~7],正如在文獻中所指出,由于空穴擴散到外表面而使空穴消除,以及由于蒸發(fā)濃縮機理而使空穴粗化,這兩個過程對表面積起著對等的作用。這是坯條致密化的重要過程,特別是對于需要繼續(xù)深度加工所需的垂熔高溫?zé)Y(jié)鎢坯條而言,需要在高溫下經(jīng)過足夠的保溫時間才能完成。
二、垂熔實驗:
為了了解在垂熔高溫?zé)Y(jié)過程中鎢坯條組織和鉀含量的變化過程,我們針對垂熔高溫?zé)Y(jié)不同階段的組織結(jié)構(gòu)變化做相關(guān)的對比實驗。
選取10根外形尺寸相近的摻雜鎢低溫?zé)Y(jié)坯條,在同一垂熔設(shè)備上,分別按圖2中選取的 1#~10#垂熔工藝點進行垂熔燒結(jié),這樣燒結(jié)出來的1#~10#垂熔坯條就可以代表在一個完整垂熔過程中不同階段的垂熔坯條情況。燒結(jié)結(jié)束后根據(jù)坯條收縮率統(tǒng)一在大頭端一定位置截取20mm長的垂熔燒結(jié)鎢坯條樣品,然后做垂熔鎢坯條橫斷面的金相組織以及鎢坯條橫斷面中心區(qū)、過渡區(qū)、邊緣區(qū)三個區(qū)域的鉀含量對比分析。
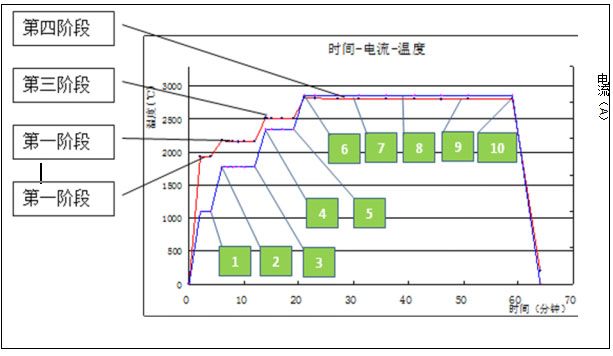
圖2. 鎢坯條垂熔時間、電流和燒結(jié)溫度工藝示意圖
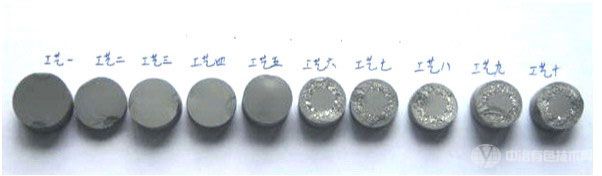
圖3. 10個實驗垂熔鎢坯條樣品的橫截面照片
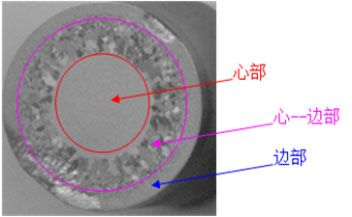
圖4. 鎢坯條橫斷面
表1. 10個實驗垂熔坯條樣品的K含量
圖5. 10個實驗垂熔坯條樣品的K含量變化趨勢
從圖3、圖4、圖5、表1中,我們可以得到以下結(jié)論:
a、垂熔高溫?zé)Y(jié)過程前12分鐘(3#樣)坯條的K揮發(fā)量占總揮發(fā)量的80~85%,在19分鐘(5#樣、剛好達到最高電流),坯條中的附加劑幾乎完全揮發(fā);
b、在垂熔燒結(jié)過程的17~19分鐘(4#和5#樣,即形成閉合孔5~6分鐘后),在鎢坯條心部直徑大概為Φ10mm左右的位置形成環(huán)形框晶;
三、高溫?zé)Y(jié)實驗結(jié)論分析及改善方向:
坯條在垂熔燒結(jié)第一、第二、第三階段中,附加劑K、Al、Si氧化物會從坯條中向四周揮發(fā)出來。如圖6所示,我們把坯條分成三層,分別為中心區(qū)、心邊過渡區(qū)、邊緣區(qū)。附加劑K、Al、Si氧化物從中心區(qū)揮發(fā)到過渡區(qū)的速度定為V1,從過渡區(qū)揮發(fā)到邊緣區(qū)的速度定為V2,而從邊緣區(qū)揮發(fā)到坯條外的速度定為V3。從表1、圖5中我們看到,在垂熔燒結(jié)不同階段,附加劑K、Al、Si氧化物揮發(fā)速度V1、V2、V3三個速度是會發(fā)生變化并且是不會相等。
圖6. 垂熔坯條附加劑揮發(fā)示意圖
垂熔燒結(jié)第一階段中,雖然坯條各部位電阻率可以理想化看作一致,通電自身產(chǎn)生的熱量也就相同,但由于散熱問題,坯條中心區(qū)的溫度T1、坯條心邊過渡區(qū)的溫度T2、坯條邊緣區(qū)的溫度T3三個區(qū)域的溫度會由高向低過渡,所以附加劑揮發(fā)速度V1>V2>V3,這可以從1#垂熔鎢坯條樣品的三個區(qū)域K含量測試值對比中得到證實。
經(jīng)過第一階段垂熔燒結(jié)后,由于附加劑K、Al、Si氧化物揮發(fā)程度不同,第二階段垂熔燒結(jié)中坯條電阻率會降低[1],但各部位電阻率就不一樣了,邊緣區(qū)k含量較高,使得電阻率ρ邊緣>ρ過渡>ρ中心,鎢坯條邊緣區(qū)的溫度T3 >坯條心邊過渡區(qū)的溫度T2>坯條中心區(qū)的溫度T1,附加劑揮發(fā)速度V3>V2>V1。在鎢坯條心邊過渡區(qū)附加劑有向坯條邊緣區(qū)揮發(fā),但同時又有鎢坯條中心區(qū)揮發(fā)的附加劑加入,這導(dǎo)致雖然鎢坯條心邊過渡區(qū)附加劑揮發(fā)速度V2>坯條中心區(qū)的V1,但是鎢坯條過渡區(qū)的附加劑減少量反而低于坯條中心區(qū)、邊緣區(qū),使得坯條過渡區(qū)的附加劑含量在坯條三個區(qū)域中最高。這一點從2#、3#垂熔鎢坯條樣品的三個區(qū)域K含量測試值對比中得到證實。
從第三階段垂熔燒結(jié)開始,坯條開始形成閉合孔隙,附加劑揮發(fā)也接近尾聲,揮發(fā)量大幅減小,但情況跟第二階段垂熔燒結(jié)差不多,這時由于坯條心邊過渡區(qū)的附加劑含量最多,電阻率最大,溫度T2也就最高,因此坯條心邊過渡區(qū)的燒結(jié)速度較快,晶??焖匍L大,進而使坯條心邊過渡區(qū)出現(xiàn)粗晶甚至框晶,這從垂熔坯條6#樣品的電鏡照片可以看到:在坯樣直徑大概為Φ10mm左右的位置形成框晶,框晶處孔洞數(shù)量比心部和邊部少。
通過以上分析,我們可以從坯條心邊過渡區(qū)厚度、附加劑揮發(fā)量、附加劑揮發(fā)速度等方面再進一步研究,從中找到解決垂熔鎢坯條出現(xiàn)環(huán)形框晶的質(zhì)量問題。
1. 控制摻雜鎢粉有效鉀含量;
摻雜鎢粉經(jīng)過酸洗后有效鉀含量為50~130ppm,而鎢粉摻雜過程中鉀的加入量超過有效鉀的20倍。在摻雜藍鎢還原過程中延長摻雜藍鎢600-700度的還原時間,將大大增加摻雜鎢粉有效鉀含量,而減少坯條垂熔燒結(jié)中附加劑揮發(fā)量,降低垂熔鎢條出現(xiàn)大晶及環(huán)形框晶的機率。
2. 摻雜鎢粉鉀含量,粒度及粒度分布;
在配粉過程中,摻雜鎢粉細粉較多使鎢條鉀含量上升晶粒變粗,比重下降,在鎢粉鉀含量較高的極端情況下使摻雜鎢條出現(xiàn)大晶或框晶而影響摻雜鎢條的加工性能及鎢絲的高溫性能。摻雜鎢粉粗粉較多使鎢條鉀含量下降,比重上升,晶粒變細,極端情況下將影響摻雜鎢條的高溫性能。因此通過合理的粒度搭配來獲得理想高溫性能的鎢絲,而不采用很高的K、Al、Si氧化物摻雜量,減少坯條垂熔燒結(jié)中附加劑揮發(fā)量,就像水池一樣,進水變小,而出水速度按原來不變,這樣這個水池的水就不滿起來,同樣道理,坯條心邊過渡區(qū)在垂熔燒結(jié)過程中不會出現(xiàn)附加劑堆積,也就不會出現(xiàn)框晶出現(xiàn)。。
3. 控制低溫?zé)Y(jié)鎢坯條比重;
低溫?zé)Y(jié)鎢坯條的比重會對摻雜鎢條的性能產(chǎn)生較大的影響。低溫?zé)Y(jié)鎢坯條的比重較高同時鉀含量也較高的情況下,鎢條在高溫?zé)Y(jié)過程中易出現(xiàn)大晶及環(huán)形框晶。此種情況出現(xiàn)時,降低鎢坯條壓制壓力是非常有效的方法,因鎢坯條的比重偏高時,在高溫?zé)Y(jié)過程中坯條中的附加劑不能充分揮發(fā)而使鎢條結(jié)晶惡化。
4.垂熔燒結(jié)制度;
降低垂熔燒結(jié)初始電流上升速率,使鎢坯條在垂熔燒結(jié)過程中孔隙閉合不至于過快,從而使鎢坯條在垂熔燒結(jié)過程中多余附加劑能充分揮發(fā),避免鎢條出現(xiàn)大晶及環(huán)形框晶。
參考文獻
[1]. 印協(xié)世. 鎢絲生產(chǎn)原理、工藝及其性能[M]. 冶金工業(yè)出版社,北京,1998,5:1-288.
[2]. 張福生. 等靜壓成型圓鎢條工藝研究[J]. 中國鎢業(yè),2000,15(3):29-35.
[3]. 譚銓斌,郭讓民,劉建章,殷為宏. 鎢的冶金及其加工技術(shù)[J]. 《中國鎢業(yè)》2007.2, VOL.22, No.1
[4]. 蔣正典,張汝珍. 金屬粉末成形和燒結(jié)原理[M]. 合肥工業(yè)大學(xué)粉末冶金教研室, 1994,2:157-213.
[5]. O.Blaschko等. 不同粒度鎢粉在燒結(jié)過程中孔隙度的變化. 羅麗譯自《Scri Mater》1996,34(7):10-1049.
[6]. 劉安生等. 關(guān)于鎢坯條中鉀泡的形成[J]. 譯自《Metallurgical Transactions》,1989,20(1) :179-184.
[7]. 張汝珍. 粉末冶金檢測技術(shù)[M]. 合肥工業(yè)大學(xué)粉末冶金教研室,1987,6:2-27.
聲明:
“高溫?zé)Y(jié)鎢坯條產(chǎn)生環(huán)形框晶組織機理研究” 該技術(shù)專利(論文)所有權(quán)利歸屬于技術(shù)(論文)所有人。僅供學(xué)習(xí)研究,如用于商業(yè)用途,請聯(lián)系該技術(shù)所有人。
我是此專利(論文)的發(fā)明人(作者)