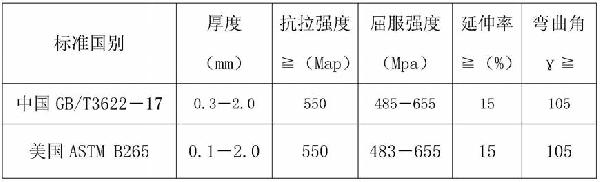
超高強(qiáng)度ta4鈦合金簿帶的生產(chǎn)工藝方法
技術(shù)領(lǐng)域
1.本發(fā)明屬于冶金技術(shù)領(lǐng)域,具體涉及一種超高強(qiáng)度ta4鈦合金簿帶的生產(chǎn)工藝方法。
背景技術(shù):
2.ta4/grade4鈦合金簿帶材是目前世界航空航天工程中使用較多的一種中等強(qiáng)度鈦合金簿帶材,同時(shí)也是電子消費(fèi)等工業(yè)領(lǐng)域特別是高端智能手機(jī)所需的一種
關(guān)鍵材料。根據(jù)應(yīng)用領(lǐng)域的需求,希望ta4/grade4合金帶箔材的綜合力學(xué)性能再進(jìn)一步提高,達(dá)到如下要求:抗拉強(qiáng)度≧700mpa,屈服強(qiáng)度≧600mpa,延伸率≧15%,也就是說,要求材料的抗拉強(qiáng)度和屈服強(qiáng)度底線分別提高150mpa和117mpa,而延伸率還必須保證維持在原指標(biāo)水平。
3.但是,目前包括美國、俄羅斯、中國等世界鈦合金加工技術(shù)發(fā)達(dá)的國家技術(shù)標(biāo)準(zhǔn)要求的力學(xué)性能中的抗拉強(qiáng)度和屈服強(qiáng)度都遠(yuǎn)低于這一要求;具體如下表所示:
[0004][0005]
傳統(tǒng)的ta4/grade4鈦合金簿帶材生產(chǎn)方法也是通過軋制并進(jìn)行真空退火或罩式退火進(jìn)行的,但由于軋制是按照基本等比變形量進(jìn)行的,通常的真空退火或罩式退火也不能解決退火過程中快速冷卻固溶問題,這樣對(duì)材料的加工組織織構(gòu)的影響是不能創(chuàng)造提高強(qiáng)度的同時(shí)又保證延伸率不降低,所以傳統(tǒng)的生產(chǎn)方法無法提高ta4/grade4鈦合金簿帶材的強(qiáng)度指標(biāo),同時(shí)不能保證其延伸率不會(huì)降低;因此,綜上所述,有必要進(jìn)行改進(jìn)。
技術(shù)實(shí)現(xiàn)要素:
[0006]
本發(fā)明解決的技術(shù)問題:提供一種超高強(qiáng)度ta4鈦合金簿帶的生產(chǎn)工藝方法,采用階梯變形量反復(fù)冷軋與多次在線連續(xù)固溶階梯退火交替形成的多軋程方式對(duì)ta4鈦合金帶進(jìn)行處理后,得到抗拉強(qiáng)度≧700mpa、屈服強(qiáng)度≧600mpa、延伸率≧15%的ta4的鈦合金簿帶,在保證ta4的鈦合金簿帶延伸率的情況下,有效的提高了ta4的鈦合金簿帶的抗拉強(qiáng)度和屈服強(qiáng)度,滿足高端設(shè)備的使用需求,具有較高的推廣應(yīng)用價(jià)值。
[0007]
本發(fā)明采用的技術(shù)方案:超高強(qiáng)度ta4鈦合金簿帶的生產(chǎn)工藝方法,采用階梯變形量反復(fù)冷軋與多次在線連續(xù)固溶階梯退火交替形成的多軋程方式對(duì)ta4鈦合金帶進(jìn)行處理后,得到抗拉強(qiáng)度≧700mpa、屈服強(qiáng)度≧600mpa、延伸率≧15%的ta4的鈦合金簿帶,具體步驟如下:
[0008]
1)冷軋:按照當(dāng)下帶厚5%~55%的變形量對(duì)ta4鈦合金帶進(jìn)行冷軋;
[0009]
2)脫油:脫除ta4鈦合金帶表面的冷軋油;
[0010]
3)退火:按照退火溫度為400~640℃且退火速度為0.5~3m/min對(duì)ta4鈦合金帶進(jìn)行退火;
[0011]
4)按照每軋程的冷軋變形量和退火溫度依次降低的順序,連續(xù)多次重復(fù)上述步驟1)至步驟3)形成對(duì)ta4鈦合金帶的多次冷軋程加工后,最終得到抗拉強(qiáng)度≧700mpa、屈服強(qiáng)度≧600mpa、延伸率≧15%的ta4鈦合金簿帶;
[0012]
5)平整:采用拉矯機(jī)對(duì)退火后的ta4鈦合金簿帶進(jìn)行矯平;
[0013]
6)分切:通過精密縱剪機(jī)組對(duì)平整后的ta4鈦合金簿帶按照尺寸要求進(jìn)行分切。
[0014]
上述步驟3)中,所述ta4鈦合金帶采用具有氬氣保護(hù)功能的在線連續(xù)固溶退火爐進(jìn)行退火。
[0015]
上述步驟4)中,所述ta4鈦合金簿帶的厚度為0.1~0.6mm。
[0016]
上述步驟4)中,對(duì)ta4鈦合金帶的第一次軋程中的冷軋變形量為當(dāng)下帶厚的45%~60%,對(duì)ta4鈦合金帶的第二次軋程中的冷軋變形量為當(dāng)下帶厚的30%~42%,對(duì)ta4鈦合金帶的第三次軋程中的冷軋變形量為當(dāng)下帶厚的20%~32%,對(duì)ta4鈦合金帶的第四次軋程中的冷軋變形量為當(dāng)下帶厚的12%~30%。
[0017]
上述步驟4)中,對(duì)ta4鈦合金帶的第一次軋程中的退火溫度為600~640℃,退火速度為0.7~1.1m/min;對(duì)ta4鈦合金帶的第二次軋程中的退火溫度為550~600℃,退火速度為1.2~2.0m/min;對(duì)ta4鈦合金帶的第三次軋程中的退火溫度為500~550℃,退火速度為1.4~2.0m/min,對(duì)ta4鈦合金帶的第四次軋程中的退火溫度為400~500℃,退火速度為1.8~2.2m/min。
[0018]
本發(fā)明與現(xiàn)有技術(shù)相比的優(yōu)點(diǎn):
[0019]
1、本技術(shù)方案采用階梯變形量反復(fù)冷軋與多次在線連續(xù)固溶階梯退火交替形成的多軋程方式對(duì)ta4鈦合金帶進(jìn)行處理后,得到抗拉強(qiáng)度≧700mpa、屈服強(qiáng)度≧600mpa、延伸率≧15%的ta4的鈦合金簿帶,在保證ta4的鈦合金簿帶延伸率的情況下,有效的提高了ta4的鈦合金簿帶的抗拉強(qiáng)度和屈服強(qiáng)度,滿足高端設(shè)備的使用需求;
[0020]
2、本技術(shù)方案采用將原來退火溫度和時(shí)間調(diào)整為梯階變化,軋制道次和退火次數(shù)不變等措施解決了國際上鈦合金帶材軋制生產(chǎn)不能提高抗拉強(qiáng)度和屈服強(qiáng)度,并保證了延伸率不降低的難題;
[0021]
3、本技術(shù)方案采用的ta4鈦合金帶材冷軋及熱處理技術(shù)后使鈦合金帶材生產(chǎn)不論是從質(zhì)量到成品率及力學(xué)性能都得到革命性提高,解決了現(xiàn)有技術(shù)難以克服的問題;
[0022]
4、本技術(shù)方案采用的ta4鈦合金帶材冷軋及熱處理技術(shù)后使鈦合金帶材生產(chǎn)可以規(guī)?;?,批量化,可較大幅度降低生產(chǎn)成本,提高鈦合金簿帶材產(chǎn)品質(zhì)量,具有重要的推廣意義。
具體實(shí)施方式
[0023]
下面結(jié)合描述本發(fā)明的第一種實(shí)施例,從而對(duì)技術(shù)方案進(jìn)行清楚、完整地描述,顯然,所描述的實(shí)施例僅僅是本發(fā)明一部分實(shí)施例,而不是全部的實(shí)施例。
[0024]
超高強(qiáng)度ta4鈦合金簿帶的生產(chǎn)工藝方法,其特征在于:采用階梯變形量反復(fù)冷軋與多次在線連續(xù)固溶階梯退火交替形成的多軋程方式對(duì)ta4鈦合金帶進(jìn)行處理后,得到抗
拉強(qiáng)度≧700mpa、屈服強(qiáng)度≧600mpa、延伸率≧15%的ta4的鈦合金簿帶,將1.2
×
530
×
l(ta4鈦合金帶長度)mm的ta4鈦合金帶坯軋制到0.15mm厚度的ta4鈦合金簿帶,其中,1.2
×
530
×
lmm ta4鈦合金帶坯的的化學(xué)成份如下:
[0025][0026][0027]
具體加工步驟如下:
[0028]
1)冷軋:按照當(dāng)下帶厚5%~55%的變形量對(duì)ta4鈦合金帶進(jìn)行冷軋;
[0029]
2)脫油:脫除ta4鈦合金帶表面的冷軋油;
[0030]
3)退火:按照退火溫度為400~640℃且退火速度為0.5~3m/min對(duì)ta4鈦合金帶進(jìn)行退火;具體的,所述ta4鈦合金帶采用具有氬氣保護(hù)功能的在線連續(xù)固溶退火爐進(jìn)行退火。
[0031]
4)按照每軋程的冷軋變形量和退火溫度依次降低的順序,連續(xù)多次重復(fù)上述步驟1)至步驟3)形成對(duì)ta4鈦合金帶的多次冷軋程加工后,最終得到抗拉強(qiáng)度≧700mpa、屈服強(qiáng)度≧600mpa、延伸率≧15%的ta4鈦合金簿帶,具體的,所述ta4鈦合金簿帶的厚度為0.15mm;
[0032]
其中,對(duì)ta4鈦合金帶的第一次軋程中由1.2
→
0.6mm的冷軋變形量為50%,對(duì)ta4鈦合金帶的第一次軋程中的退火溫度為630℃,退火速度為1.0m/min;
[0033]
對(duì)ta4鈦合金帶的第二次軋程中由0.60
→
0.37mm的冷軋變形量為38.3%,退火溫度為550℃,退火速度為1.3m/min;
[0034]
對(duì)ta4鈦合金帶的第三次軋程中由0.37
→
0.26mm的冷軋變形量為29.7%,退火溫度為500℃,退火速度為1.8m/min;
[0035]
對(duì)ta4鈦合金帶的第四次軋程中由0.26
→
0.195mm的冷軋變形量為25%,退火溫度為450℃,退火速度為2.2m/min;
[0036]
上述加工過程完畢后,可根據(jù)加工情況,進(jìn)行第五次軋程,由0.195
→
0.15mm的變形量為23.08%,退火溫度為400℃,退火速度2.2m/min;
[0037]
加工后的力學(xué)性能如下:
[0038][0039]
5)平整:采用拉矯機(jī)對(duì)退火后的ta4鈦合金簿帶進(jìn)行矯平;
[0040]
6)分切:通過精密縱剪機(jī)組對(duì)平整后的ta4鈦合金簿帶按照尺寸要求進(jìn)行分切。
[0041]
下面結(jié)合描述本發(fā)明的第二種實(shí)施例,從而對(duì)技術(shù)方案進(jìn)行清楚、完整地描述,顯然,所描述的實(shí)施例僅僅是本發(fā)明一部分實(shí)施例,而不是全部的實(shí)施例。
[0042]
超高強(qiáng)度ta4鈦合金簿帶的生產(chǎn)工藝方法,采用階梯變形量反復(fù)冷軋與多次在線連續(xù)固溶階梯退火交替形成的多軋程方式對(duì)ta4鈦合金帶進(jìn)行處理后,得到抗拉強(qiáng)度≧700mpa、屈服強(qiáng)度≧600mpa、延伸率≧15%的ta4的鈦合金簿帶,將1.8
×
600
×
l(ta4鈦合金板坯長度)mm的ta4鈦合金帶坯軋制到0.3mm厚度,其中,1.8
×
530
×
lmm ta4鈦合金帶坯的的化學(xué)成份如下:
[0043][0044]
具體加工步驟如下:
[0045]
1)冷軋:按照當(dāng)下帶厚5%~55%的變形量對(duì)ta4鈦合金帶進(jìn)行冷軋;
[0046]
2)脫油:脫除ta4鈦合金帶表面的冷軋油;
[0047]
3)退火:按照退火溫度為400~640℃且退火速度為0.5~3m/min對(duì)ta4鈦合金帶進(jìn)行退火;具體的,所述ta4鈦合金帶采用具有氬氣保護(hù)功能的在線連續(xù)固溶退火爐進(jìn)行退火。
[0048]
4)按照每軋程的冷軋變形量和退火溫度依次降低的順序,連續(xù)多次重復(fù)上述步驟1)至步驟3)形成對(duì)ta4鈦合金帶的多次冷軋程加工后,最終得到抗拉強(qiáng)度≧700mpa、屈服強(qiáng)度≧600mpa、延伸率≧15%的ta4鈦合金簿帶,具體的,所述ta4鈦合金簿帶的厚度為0.3mm;
[0049]
其中,對(duì)ta4鈦合金帶的第一次軋程中由1.8
→
0.9mm的冷軋變形量為50%,對(duì)ta4鈦合金帶的第一次軋程中的退火溫度為640℃,退火速度為0.7m/min;
[0050]
對(duì)ta4鈦合金帶的第二次軋程中由0.9
→
0.56mm的冷軋變形量為37.8%,退火溫度為600℃,退火速度為1.0m/min;
[0051]
對(duì)ta4鈦合金帶的第三次軋程中由0.56
→
0.4mm的冷軋變形量為28.6%,退火溫度為550℃,退火速度為1.5m/min;
[0052]
對(duì)ta4鈦合金帶的第四次軋程中由0.4
→
0.3mm的冷軋變形量為25%,退火溫度為500℃,退火速度為1.8m/min;
[0053]
加工后的力學(xué)性能如下:
[0054][0055][0056]
5)平整:采用拉矯機(jī)對(duì)退火后的ta4鈦合金簿帶進(jìn)行矯平;
[0057]
6)分切:通過精密縱剪機(jī)組對(duì)平整后的ta4鈦合金簿帶按照尺寸要求進(jìn)行分切。
[0058]
下面結(jié)合描述本發(fā)明的第三種實(shí)施例,從而對(duì)技術(shù)方案進(jìn)行清楚、完整地描述,顯然,所描述的實(shí)施例僅僅是本發(fā)明一部分實(shí)施例,而不是全部的實(shí)施例。
[0059]
超高強(qiáng)度ta4鈦合金簿帶的生產(chǎn)工藝方法,其特征在于:采用階梯變形量反復(fù)冷軋與多次在線連續(xù)固溶階梯退火交替形成的多軋程方式對(duì)ta4鈦合金帶進(jìn)行處理后,得到抗拉強(qiáng)度≧700mpa、屈服強(qiáng)度≧600mpa、延伸率≧15%的ta4的鈦合金簿帶,將2.0
×
510
×
l(ta4鈦合金板坯長度)mm的ta4鈦合金帶坯軋制到0.5mm厚度,其中,2.0
×
510
×
lmm ta4鈦合金帶坯的的化學(xué)成份如下:
[0060][0061]
具體加工步驟如下:
[0062]
1)冷軋:按照當(dāng)下帶厚5%~55%的變形量對(duì)ta4鈦合金帶進(jìn)行冷軋;
[0063]
2)脫油:脫除ta4鈦合金帶表面的冷軋油;
[0064]
3)退火:按照退火溫度為400~640℃且退火速度為0.5~3m/min對(duì)ta4鈦合金帶進(jìn)行退火;具體的,所述ta4鈦合金帶采用具有氬氣保護(hù)功能的在線連續(xù)固溶退火爐進(jìn)行退火。
[0065]
4)按照每軋程的冷軋變形量和退火溫度依次降低的順序,連續(xù)多次重復(fù)上述步驟
1)至步驟3)形成對(duì)ta4鈦合金帶的多次冷軋程加工后,最終得到抗拉強(qiáng)度≧700mpa、屈服強(qiáng)度≧600mpa、延伸率≧15%的ta4鈦合金簿帶,具體的,所述ta4鈦合金簿帶的厚度為0.5mm;
[0066]
其中,對(duì)ta4鈦合金帶的第一次軋程中由2.0
→
1.1mm的冷軋變形量為45%,對(duì)ta4鈦合金帶的第一次軋程中的退火溫度為620℃,退火速度為1.0m/min;
[0067]
對(duì)ta4鈦合金帶的第二次軋程中由1.1
→
0.77mm的冷軋變形量為30%,退火溫度為550℃,退火速度為1.3m/min;
[0068]
對(duì)ta4鈦合金帶的第三次軋程中由0.77
→
0.615mm的冷軋變形量為20.13%,退火溫度為500℃,退火速度為1.8m/min;
[0069]
對(duì)ta4鈦合金帶的第四次軋程中由0.615
→
0.5mm的冷軋變形量為18.7%,退火溫度為450℃,退火速度為2.2m/min;
[0070]
加工后的力學(xué)性能如下:
[0071][0072][0073]
5)平整:采用拉矯機(jī)對(duì)退火后的ta4鈦合金簿帶進(jìn)行矯平;
[0074]
6)分切:通過精密縱剪機(jī)組對(duì)平整后的ta4鈦合金簿帶按照尺寸要求進(jìn)行分切。
[0075]
下面結(jié)合描述本發(fā)明的第四種實(shí)施例,從而對(duì)技術(shù)方案進(jìn)行清楚、完整地描述,顯然,所描述的實(shí)施例僅僅是本發(fā)明一部分實(shí)施例,而不是全部的實(shí)施例。
[0076]
超高強(qiáng)度ta4鈦合金簿帶的生產(chǎn)工藝方法,采用階梯變形量反復(fù)冷軋與多次在線連續(xù)固溶階梯退火交替形成的多軋程方式對(duì)ta4鈦合金帶進(jìn)行處理后,得到抗拉強(qiáng)度≧700mpa、屈服強(qiáng)度≧600mpa、延伸率≧15%的ta4的鈦合金簿帶,將1.2
×
520
×
l(ta4鈦合金板坯長度)mm的ta4鈦合金帶坯軋制到0.1mm厚度,其中,1.2
×
520
×
llmm ta4鈦合金帶坯的的化學(xué)成份如下:
[0077][0078]
具體加工過程如下:
[0079]
1)冷軋:按照當(dāng)下帶厚5%~55%的變形量對(duì)ta4鈦合金帶進(jìn)行冷軋;
[0080]
2)脫油:脫除ta4鈦合金帶表面的冷軋油;
[0081]
3)退火:按照退火溫度為400~640℃且退火速度為0.5~3m/min對(duì)ta4鈦合金帶進(jìn)行退火;具體的,所述ta4鈦合金帶采用具有氬氣保護(hù)功能的在線連續(xù)固溶退火爐進(jìn)行退火。
[0082]
4)按照每軋程的冷軋變形量和退火溫度依次降低的順序,連續(xù)多次重復(fù)上述步驟1)至步驟3)形成對(duì)ta4鈦合金帶的多次冷軋程加工后,最終得到抗拉強(qiáng)度≧700mpa、屈服強(qiáng)度≧600mpa、延伸率≧15%的ta4鈦合金簿帶,具體的,所述ta4鈦合金簿帶的厚度為0.1mm;
[0083]
其中,對(duì)ta4鈦合金帶的第一次軋程中由1.2
→
0.58mm的冷軋變形量為51.67%,對(duì)ta4鈦合金帶的第一次軋程中的退火溫度為630℃,退火速度為1.0m/min;
[0084]
對(duì)ta4鈦合金帶的第二次軋程中由0.58
→
0.35mm的冷軋變形量為39.65%,退火溫度為600℃,退火速度為1.3m/min;
[0085]
對(duì)ta4鈦合金帶的第三次軋程中由0.35
→
0.25mm的冷軋變形量為28.6%,退火溫度為550℃,退火速度為1.8m/min;
[0086]
對(duì)ta4鈦合金帶的第四次軋程中由0.25
→
0.18mm的冷軋變形量為28%,退火溫度為500℃,退火速度為2.1m/min;
[0087]
上述加工過程完畢后,可根據(jù)加工情況,進(jìn)行第五次軋程,由0.18
→
0.14mm的變形量為22.22%,退火溫度為450℃,退火速度2.3m/min;
[0088]
第六次軋程,由0.14
→
0.1mm的變形量為28.57%,退火溫度為400℃,退火速度2.5m/min;
[0089]
加工后的力學(xué)性能如下:
[0090][0091]
5)平整:采用拉矯機(jī)對(duì)退火后的ta4鈦合金簿帶進(jìn)行矯平;
[0092]
6)分切:通過精密縱剪機(jī)組對(duì)平整后的ta4鈦合金簿帶按照尺寸要求進(jìn)行分切。
[0093]
本技術(shù)方案采用階梯變形量反復(fù)冷軋與多次在線連續(xù)固溶階梯退火交替形成的多軋程方式對(duì)ta4鈦合金帶進(jìn)行處理后,得到抗拉強(qiáng)度≧700mpa、屈服強(qiáng)度≧600mpa、延伸率≧15%的ta4的鈦合金簿帶,在保證ta4的鈦合金簿帶延伸率的情況下,有效的提高了ta4的鈦合金簿帶的抗拉強(qiáng)度和屈服強(qiáng)度,滿足高端設(shè)備的使用需求,采用將原來退火溫度和時(shí)間調(diào)整為梯階變化,軋制道次和退火次數(shù)不變等措施解決了國際上鈦合金帶材軋制生產(chǎn)不能提高抗拉強(qiáng)度和屈服強(qiáng)度,并保證了延伸率不降低的難題,采用的ta4鈦合金帶材冷軋及熱處理技術(shù)后使鈦合金帶材生產(chǎn)不論是從質(zhì)量到成品率及力學(xué)性能都得到革命性提高,解決了現(xiàn)有技術(shù)難以克服的問題,采用的ta4鈦合金帶材冷軋及熱處理技術(shù)后使鈦合金帶
材生產(chǎn)可以規(guī)?;?,批量化,可較大幅度降低生產(chǎn)成本,提高鈦合金簿帶材產(chǎn)品質(zhì)量,具有重要的推廣意義。
[0094]
上述實(shí)施例,只是本發(fā)明的較佳實(shí)施例,并非用來限制本發(fā)明實(shí)施范圍,故凡以本發(fā)明權(quán)利要求所述內(nèi)容所做的等效變化,均應(yīng)包括在本發(fā)明權(quán)利要求范圍之內(nèi)。技術(shù)特征:
1.超高強(qiáng)度ta4鈦合金簿帶的生產(chǎn)工藝方法,其特征在于:采用階梯變形量反復(fù)冷軋與多次在線連續(xù)固溶階梯退火交替形成的多軋程方式對(duì)ta4鈦合金帶進(jìn)行處理后,得到抗拉強(qiáng)度≧700mpa、屈服強(qiáng)度≧600mpa、延伸率≧15%的ta4的鈦合金簿帶,具體步驟如下:1)冷軋:按照當(dāng)下帶厚5%~55%的變形量對(duì)ta4鈦合金帶進(jìn)行冷軋;2)脫油:脫除ta4鈦合金帶表面的冷軋油;3)退火:按照退火溫度為400~640℃且退火速度為0.5~3m/min對(duì)ta4鈦合金帶進(jìn)行退火;4)按照每軋程的冷軋變形量和退火溫度依次降低的順序,連續(xù)多次重復(fù)上述步驟1)至步驟3)形成對(duì)ta4鈦合金帶的多次冷軋程加工后,最終得到抗拉強(qiáng)度≧700mpa、屈服強(qiáng)度≧600mpa、延伸率≧15%的ta4鈦合金簿帶;5)平整:采用拉矯機(jī)對(duì)退火后的ta4鈦合金簿帶進(jìn)行矯平;6)分切:通過精密縱剪機(jī)組對(duì)平整后的ta4鈦合金簿帶按照尺寸要求進(jìn)行分切。2.根據(jù)權(quán)利要求1所述的超高強(qiáng)度ta4鈦合金簿帶的生產(chǎn)工藝方法,其特征在于:上述步驟3)中,所述ta4鈦合金帶采用具有氬氣保護(hù)功能的在線連續(xù)固溶退火爐進(jìn)行退火。3.根據(jù)權(quán)利要求1所述的超高強(qiáng)度ta4鈦合金簿帶的生產(chǎn)工藝方法,其特征在于:上述步驟4)中,所述ta4鈦合金簿帶的厚度為0.1~0.6mm。4.根據(jù)權(quán)利要求1所述的超高強(qiáng)度ta4鈦合金簿帶的生產(chǎn)工藝方法,其特征在于:上述步驟4)中,對(duì)ta4鈦合金帶的第一次軋程中的冷軋變形量為當(dāng)下帶厚的45%~60%,對(duì)ta4鈦合金帶的第二次軋程中的冷軋變形量為當(dāng)下帶厚的30%~42%,對(duì)ta4鈦合金帶的第三次軋程中的冷軋變形量為當(dāng)下帶厚的20%~32%,對(duì)ta4鈦合金帶的第四次軋程中的冷軋變形量為當(dāng)下帶厚的12%~30%。5.根據(jù)權(quán)利要求1所述的超高強(qiáng)度ta4鈦合金簿帶的生產(chǎn)工藝方法,其特征在于:上述步驟4)中,對(duì)ta4鈦合金帶的第一次軋程中的退火溫度為600~640℃,退火速度為0.7~1.1m/min;對(duì)ta4鈦合金帶的第二次軋程中的退火溫度為550~600℃,退火速度為1.2~2.0m/min;對(duì)ta4鈦合金帶的第三次軋程中的退火溫度為500~550℃,退火速度為1.4~2.0m/min,對(duì)ta4鈦合金帶的第四次軋程中的退火溫度為400~500℃,退火速度為1.8~2.2m/min。
技術(shù)總結(jié)
提供一種采用階梯變形量反復(fù)冷軋與多次在線連續(xù)固溶階梯退火交替形成的多軋程方式對(duì)TA4鈦合金帶進(jìn)行處理后,得到抗拉強(qiáng)度≧700Mpa、屈服強(qiáng)度≧600Mpa、延伸率≧15%的TA4的鈦合金簿帶,在保證TA4的鈦合金簿帶延伸率的情況下,有效的提高了TA4的鈦合金簿帶的抗拉強(qiáng)度和屈服強(qiáng)度,滿足高端設(shè)備的使用需求,具有較高的推廣應(yīng)用價(jià)值。具有較高的推廣應(yīng)用價(jià)值。
技術(shù)研發(fā)人員:唐普放 楊艾琴 唐韻
受保護(hù)的技術(shù)使用者:陜西凸鵬鈦鋯股份有限公司
技術(shù)研發(fā)日:2020.12.09
技術(shù)公布日:2021/4/17
聲明:
“超高強(qiáng)度TA4鈦合金簿帶的生產(chǎn)工藝方法與流程” 該技術(shù)專利(論文)所有權(quán)利歸屬于技術(shù)(論文)所有人。僅供學(xué)習(xí)研究,如用于商業(yè)用途,請(qǐng)聯(lián)系該技術(shù)所有人。
我是此專利(論文)的發(fā)明人(作者)