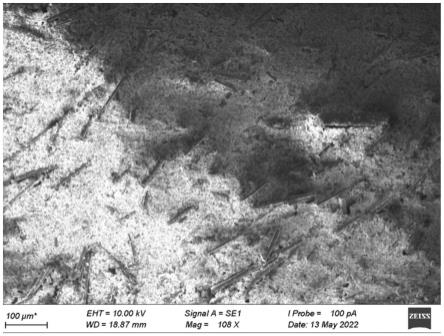
1.本發(fā)明涉及性能各向異性
復(fù)合材料的制備方法,具體涉及一種定向排列的短纖維增強(qiáng)低膨脹玻璃基復(fù)合材料的制備方法及采用該方法制備的定向排列的短纖維增強(qiáng)低膨脹玻璃基復(fù)合材料。
背景技術(shù):
2.航天航空、汽車工業(yè)、精密儀器等領(lǐng)域都涉及到輕質(zhì)低膨脹的結(jié)構(gòu)類復(fù)合材料的應(yīng)用,力學(xué)性能和熱學(xué)性能是衡量這些結(jié)構(gòu)類復(fù)合材料性能的重要指標(biāo)。該類復(fù)合材料的性能除了與組分各自的性能、比例、復(fù)合材料孔隙率有關(guān)外,還與組分(如纖維)在復(fù)合材料中的排列情況有關(guān)。作為復(fù)合材料力學(xué)性能的增強(qiáng)體,纖維的排列方向直接決定其在某個方向上的最大承載力,同時也影響了這個方向上的熱學(xué)性能。
3.在復(fù)合材料普通注漿成型過程中,因?yàn)槔w維的取向是隨機(jī)分布的,因此,它們的性能是沿每個方向的統(tǒng)計(jì)平均值,并表現(xiàn)出與微觀結(jié)構(gòu)相對應(yīng)的各向同性。據(jù)分析表明,隨機(jī)分布的纖維實(shí)際上只有40%發(fā)揮了增韌作用,而其余部分并未得到有效利用,造成很大的資源浪費(fèi)。纖維的定向排列可以賦予復(fù)合材料在特定方向上的某種特殊性能,如可大大提高與纖維排列方向相垂直方向上的力學(xué)性能,同時可實(shí)現(xiàn)復(fù)合材料在兩個不同方向上的熱學(xué)性能各向異性。纖維的定向排列不僅對復(fù)合材料的特定方向上的力學(xué)性能顯著增強(qiáng),而且還可以減少纖維用量,降低材料的孔隙率,進(jìn)一步提高復(fù)合材料的致密度和品質(zhì),節(jié)約原料成本。
4.目前,對纖維實(shí)現(xiàn)有序排列的基質(zhì)主要是有機(jī)聚合物,針對低膨脹玻璃基三相復(fù)合材料,且在注漿成型過程中一步法實(shí)現(xiàn)非磁性纖維的定向排列還未見報(bào)道。
技術(shù)實(shí)現(xiàn)要素:
5.本發(fā)明的目的是解決現(xiàn)有技術(shù)所制備的復(fù)合材料中短纖維原料隨機(jī)無序排布而無法實(shí)現(xiàn)某個方向上力學(xué)性能、熱學(xué)性能提升的技術(shù)問題,而提供一種定向排列的短纖維增強(qiáng)低膨脹玻璃基復(fù)合材料的制備方法及復(fù)合材料。
6.本發(fā)明中制備方法的構(gòu)思是:通過在復(fù)合材料注漿成型過程中加入強(qiáng)磁場,使磁化的纖維在磁場中受到磁場力發(fā)生扭轉(zhuǎn),在成型的同時達(dá)到纖維的有序排列,最終獲得一種短纖維原料定向排列、定向增強(qiáng)、且力學(xué)和熱學(xué)性能各向異性的低膨脹玻璃基復(fù)合材料,本發(fā)明制備得到的一種定向排列的短纖維原料增強(qiáng)低膨脹玻璃基復(fù)合材料適用于航空航天、汽車行業(yè)、精密儀器等領(lǐng)域的結(jié)構(gòu)類材料的應(yīng)用。
7.本發(fā)明的技術(shù)解決方案是:
8.一種定向排列的短纖維增強(qiáng)低膨脹玻璃基復(fù)合材料的制備方法,其特殊之處在于,包括以下步驟:
9.1)漿料制備
10.1.1)分別稱取原料總量50%~60%質(zhì)量比的高硼硅玻璃粉原料、原料總量27%~33%質(zhì)量比的β-鋰霞石粉原料和原料總量10%~18%質(zhì)量比的短纖維原料;
11.1.2)將高硼硅玻璃粉原料、β-鋰霞石粉原料加入到球磨罐中,加入占原料總量50%~94%質(zhì)量比的高純水,再加入占原料總量0.1%~0.5%質(zhì)量比的分散劑溶液,加入直徑為3~5mm的
氧化鋯球,球磨混合均勻,再加入相應(yīng)的短纖維原料,繼續(xù)球磨混合20~40分鐘得到均勻漿料;氧化鋯球的質(zhì)量與原料總量的比為2:1;
12.1.3)將漿料過100~200目篩,過篩后的漿料在攪拌條件下調(diào)節(jié)ph值為8~11,得到均勻穩(wěn)定的三元復(fù)合物漿料;
13.1.4)將三元復(fù)合物漿料中的氣泡抽真空去除;
14.2)注漿
15.將去除氣泡的三元復(fù)合物漿料傾斜45度緩慢倒入預(yù)先制備好的具有一定濕度的模具中;
16.3)磁場中成型
17.將步驟2)中的模具放入磁場中,在磁場中進(jìn)行磁化,完成纖維有序排列和復(fù)合材料的成型;漿料干燥后將模具取出,靜置固化后,脫模;所述磁場的磁場強(qiáng)度為12~16t,重力場為1g~2g,在磁場中進(jìn)行磁化的時間為30~45分鐘;
18.4)將脫模后的坯體進(jìn)行干燥;
19.5)將干燥后的坯體在760℃~850℃進(jìn)行真空無壓燒結(jié),得到定向排列的短纖維增強(qiáng)低膨脹玻璃基復(fù)合材料。
20.進(jìn)一步地,步驟2)中,所述具有一定濕度的模具中水分含量為15%~25%。
21.進(jìn)一步地,步驟1.1)中,所述高硼硅玻璃粉原料的粒徑為0.5~0.9μm;所述β-鋰霞石粉原料的粒徑為0.2~0.9μm;所述短纖維原料為莫來石、氧化鋯、氧化鋅、鈦酸鉛、碳化硅、氮化硅、硼化鋯、硫酸鈣、玻璃纖維中的其中一種;所述短纖維原料的直徑為0.5~5μm,短纖維原料的長徑比為20~40。
22.進(jìn)一步地,步驟1.3)中,調(diào)節(jié)ph的方法為:在電動機(jī)械攪拌條件下,用氨水或氫氧化鈉調(diào)節(jié)。
23.進(jìn)一步地,步驟1.2)中,所述分散劑溶液為5%濃度的聚乙烯醇、乙二醇和檸檬酸銨溶液中的其中一種。
24.進(jìn)一步地,步驟1.4)中,所述三元復(fù)合物漿料中的氣泡去除的方法為:將三元復(fù)合物漿料放入真空箱中,在真空度為-0.01~-0.03mpa條件下保持10~15min,將氣泡去除。
25.進(jìn)一步地,步驟4)中,所述干燥方法為:先在室溫下干燥2-3天,再放入烘箱在30~38℃下進(jìn)行恒溫干燥10~15天。
26.進(jìn)一步地,步驟5)中,真空無壓燒結(jié)的過程為:將干燥后的坯體放入馬弗爐中,先緩慢升溫至760~850℃,真空條件下保溫5~10h;然后降至650℃,保溫2h,然后降至550℃,保溫2h,最后再降至400℃,隨爐自然冷卻至室溫。
27.進(jìn)一步地,步驟1.1)中分別稱取的高硼硅玻璃粉原料、β-鋰霞石粉原料和莫來石短纖維原料的質(zhì)量比為54%、31%和15%;
28.步驟1.2)中,加入高純水的量占原料總量的62.5%,加入分散劑溶液的量占原料總量0.2%;
29.步驟1.3)中,將漿料過200目篩;過篩后的漿料在攪拌條件下調(diào)節(jié)ph值為9;
30.步驟2)中,所述具有一定濕度模具中水分含量為20%;
31.步驟3中,所述磁場的強(qiáng)度為16t,重力場為1g,磁化時間為30分鐘;
32.步驟5)中,真空無壓燒結(jié)溫度為805℃。
33.一種定向排列的短纖維增強(qiáng)低膨脹玻璃基復(fù)合材料,其特殊之處在于:采用上述定向排列的短纖維增強(qiáng)低膨脹玻璃基復(fù)合材料的制備方法制備。
34.本發(fā)明的有益效果:
35.1、本發(fā)明制備方法,結(jié)合注漿成型法的優(yōu)點(diǎn),在低膨脹玻璃基三相復(fù)合材料注漿成型過程中,通過強(qiáng)磁場的誘導(dǎo),使磁化的纖維在磁場中受到磁場力的扭轉(zhuǎn),實(shí)現(xiàn)纖維在復(fù)合材料中的定向排列,獲得性能可調(diào)且性能各向異性的復(fù)合材料,相比于現(xiàn)有技術(shù)制備的復(fù)合材料中纖維的隨機(jī)無序排列,該復(fù)合材料在垂直于纖維排列的方向上,力學(xué)性能大大提升,抗彎強(qiáng)度提高了50%,膨脹系數(shù)也顯示出各向異性,使纖維發(fā)揮了極大增韌性能的同時,還調(diào)節(jié)了材料的膨脹系數(shù),不僅滿足了特殊應(yīng)用環(huán)境條件下對材料在不同方向上的力學(xué)性能和熱學(xué)性能各相向異性的要求,還減少了纖維用量,節(jié)約了生產(chǎn)成本。
36.2、本發(fā)明制備方法,將漿料倒入具有一定濕度的模具中,使接觸模具的漿料在完成定向排列前不易干結(jié),漿料中纖維受磁場作用進(jìn)行定向排列的阻礙力減小。
37.3、本發(fā)明制備方法,結(jié)合磁場和重力場,使纖維能在特定的方向上進(jìn)行排列,通過簡單的設(shè)備即可實(shí)現(xiàn)。
38.4、本發(fā)明制備方法,短纖維原料采用莫來石、氧化鋯、氧化鋅、鈦酸鉛、碳化硅、氮化硅、硼化鋯、硫酸鈣、玻璃纖維等,上述材料在力學(xué)性能和膨脹系數(shù)等方面均表現(xiàn)良好,對本發(fā)明實(shí)現(xiàn)短纖維的定向排列和復(fù)合材料性能調(diào)節(jié)奠定了良好的基礎(chǔ)。
39.5、本發(fā)明制備方法,通過調(diào)節(jié)漿料的ph值,使?jié){料的zeta電位的絕對值最大,漿料能夠保持穩(wěn)定分散。
40.6、本發(fā)明制備方法采用真空除泡技術(shù),將漿料中的氣泡排除,并以45
°
傾斜角度將漿料緩慢倒入模具中排出模具中的空氣,兩步排氣大大降低了復(fù)合材料坯體中氣孔。
41.7、本發(fā)明制備方法通過簡單的真空無壓燒結(jié)制得,生產(chǎn)工藝及設(shè)備簡單、生產(chǎn)成本較低,節(jié)能減排。
42.8、本發(fā)明制備方法所用的高硼硅玻璃粉原料尺寸和β-鋰霞石粉原料尺寸均為微納米級,大大提高了漿料的穩(wěn)定性,保證了坯體的均勻穩(wěn)定性。
附圖說明
43.圖1是本發(fā)明實(shí)施例1所制備得到的復(fù)合材料斷面的掃描電鏡(sem)圖;
44.圖2是現(xiàn)有技術(shù)通過注漿成型法制備得到的復(fù)合材料斷面掃描電鏡(sem)圖;
45.圖3是本發(fā)明實(shí)施例1所制備得到的復(fù)合材料在垂直于纖維排列方向上的膨脹系數(shù)圖;
46.圖4是本發(fā)明實(shí)施例1所制備得到的復(fù)合材料在平行于纖維排列方向上的膨脹系數(shù)圖;
47.圖5是現(xiàn)有注漿技術(shù)所制備得到的纖維無序排列復(fù)合材料的膨脹系數(shù)圖。
具體實(shí)施方式
48.本發(fā)明結(jié)合注漿成型法的優(yōu)點(diǎn),在低膨脹玻璃基三相復(fù)合材料注漿成型過程中,通過強(qiáng)磁場的誘導(dǎo),實(shí)現(xiàn)纖維在復(fù)合材料中的定向排列,獲得性能可調(diào)且性能各向異性的復(fù)合材料。這些材料可以用于特殊環(huán)境下的結(jié)構(gòu)材料,如用作光纖陀螺骨架,滿足其在垂直于光纖線圈和平行于光纖線圈上的熱學(xué)各向異性的需求。
49.本發(fā)明提供的一種定向排列的短纖維增強(qiáng)低膨脹玻璃基復(fù)合材料的制備方法,包括以下步驟:
50.1)漿料制備
51.1.1)分別稱取原料總量50%~60%質(zhì)量比的高硼硅玻璃粉原料、原料總量27%~33%質(zhì)量比的β-鋰霞石粉原料和原料總量10%~18%質(zhì)量比的短纖維原料;
52.其中,高硼硅玻璃粉原料的粒徑為0.5~0.9μm;β-鋰霞石粉原料的粒徑為0.2~0.9μm;短纖維原料為莫來石、氧化鋯、氧化鋅、鈦酸鉛、碳化硅、氮化硅、硼化鋯、硫酸鈣、玻璃纖維纖維中的其中一種,短纖維原料的直徑為0.5~5μm,短纖維原料的長徑比為20~40。
53.1.2)將高硼硅玻璃粉原料、β-鋰霞石粉原料加入到球磨罐中,加入占原料總量50%~94%質(zhì)量比的高純水,再加入占原料總量0.1%~0.5%質(zhì)量比的分散劑溶液,按球料比2:1加入直徑為3~5mm的氧化鋯球,球磨混合均勻,再加入相應(yīng)的短纖維原料,繼續(xù)球磨混合20~40分鐘得到均勻漿料;
54.其中,分散劑溶液為5%濃度的聚乙烯醇、乙二醇和檸檬酸銨溶液中的其中一種。
55.1.3)將漿料過100~200目篩,過篩后的漿料在攪拌條件下調(diào)節(jié)ph值為8~11,得到均勻穩(wěn)定的三元復(fù)合物漿料。
56.1.4)將三元復(fù)合物漿料中的氣泡抽真空去除;三元復(fù)合物漿料中的氣泡去除的方法為:將三元復(fù)合物漿料放入真空箱中,在真空度為-0.01~-0.03mpa條件下保持10~15min,將氣泡去除。
57.2)注漿
58.將去除氣泡的三元復(fù)合物漿料傾斜45度緩慢倒入預(yù)先制備好的具有一定濕度的模具中;模具中水分含量為15%~25%;
59.3)磁場中成型
60.將步驟2)中的模具放入磁場中,在磁場中進(jìn)行磁化,完成纖維有序排列和復(fù)合材料的成型;將模具取出,室溫固化后,脫模;其中,磁場的強(qiáng)度為12~16t,重力場為1g~2g,磁化時間為30~45分鐘;
61.4)將脫模后的坯體進(jìn)行干燥;干燥方法為:先在室溫下干燥2-3天,再放入烘箱在30~38℃下進(jìn)行恒溫干燥10~15天。
62.5)將干燥后的坯體在760℃~850℃進(jìn)行真空無壓燒結(jié),無壓燒結(jié)的過程為:將干燥后的坯體放入馬弗爐中,先緩慢升溫至760~850℃,真空條件下保溫5~10h;然后降至650℃,保溫2h,然后降至550℃,保溫2h,最后再降至400℃,隨爐自然冷卻至室溫,得到定向排列的短纖維原料增強(qiáng)低膨脹玻璃基復(fù)合材料。
63.下面通過具體的實(shí)施例和附圖對本發(fā)明進(jìn)行詳細(xì)的說明描述。
64.實(shí)施例1
65.以原料總重20g為基準(zhǔn),按照以下步驟制備短纖維原料增韌的低膨脹玻璃基三元
復(fù)合材料,模具尺寸φ35mm
×
40mm。
66.1)漿料制備:按照高硼硅玻璃粉原料、β-鋰霞石粉原料、短纖維原料分別為54wt%、31wt%、15wt%的質(zhì)量比例,首先稱取10.8g粒徑為0.5~0.7μm的高硼硅玻璃粉原料和6.2g粒徑為0.2~0.5μm的β-鋰霞石粉原料,再稱取40g直徑為5mm的氧化鋯球(氧化鋯球的質(zhì)量與原料總量的比為2:1),然后量取12.5ml高純水(占總固體原料質(zhì)量比為62.5%),加入0.8ml、5%的乙二醇溶液,使分散劑占原料總量的0.2%,在氧化鋯的球磨罐中混合后,將球磨罐放入球磨機(jī)中,在250rpm/min的轉(zhuǎn)速下球磨混合20min后,然后再向球磨罐中再加入3g莫來石纖維(直徑為5μm,長徑比為20~40),在250rpm/min下繼續(xù)球磨混合30min,得到均勻漿料。將漿料過200目篩,然后在電動機(jī)械攪拌條件下用氨水調(diào)節(jié)漿料的ph值為9,獲得固相含量為60wt%、粘度為37mpa
·
s的均勻穩(wěn)定的三元復(fù)合物漿料。將三元復(fù)合物漿料放置于真空箱中,進(jìn)行真空除泡10min,真空度為-0.02mpa,獲得的三元復(fù)合物漿料待用。
67.2)注漿:將上述除泡后的三元復(fù)合物漿料以45
°
傾斜角緩慢注入含水量為20%,尺寸為φ35mm
×
40mm的石膏模具中。
68.3)磁場中成型:將裝有漿料的模具固定在支架上,放入強(qiáng)磁體的磁場中,在重力場為1g,磁場強(qiáng)度為16t的條件下磁化30分鐘,待漿料干燥后,緩慢取出模具;靜置固化1h后,脫模,獲得尺寸為φ35mm
×
25mm的坯體。
69.4)坯體干燥:將坯體在室溫下干燥3天,然后將其放置在烘箱中,38℃條件下干燥15天。
70.5)燒結(jié):將干燥后的坯體放入馬弗爐中,進(jìn)行真空無壓燒結(jié)。燒結(jié)過程為:先緩慢升溫至805℃,真空條件下保溫5h;然后降至650℃,保溫2h,然后降至550℃,保溫2h,最后再降至400℃,隨爐自然冷卻至室溫,得到定向排列的短纖維增強(qiáng)低膨脹玻璃基復(fù)合材料,尺寸為φ30mm
×
12mm。
71.圖1是本實(shí)施例所制備得到的復(fù)合材料斷面的掃描電鏡(sem)圖,圖2是現(xiàn)有技術(shù)通過注漿成型法制備得到的復(fù)合材料斷面形貌圖。兩圖對比可以看出,通過強(qiáng)磁場的引入,復(fù)合材料中纖維排列有序。本實(shí)施例所制備的復(fù)合材料密度為2.35g/cm3,與普通注漿成型相比(2.32g/cm3)明顯提高,說明該技術(shù)方案制備的復(fù)合材料更加致密。本實(shí)施例制得到的復(fù)合材料在垂直于纖維排列方向上的抗彎強(qiáng)度為139mpa,平均膨脹系數(shù)為1.48
×
10-6
/k(圖3)。在平行于纖維排列方向上的抗彎強(qiáng)度為75mpa,平均膨脹系數(shù)為1.89
×
10-6
/k(圖4)?,F(xiàn)有技術(shù)注漿成型法制備的樣品抗彎強(qiáng)度83mpa,平均膨脹系數(shù)為1.76
×
10-6
/k(圖5)。通過纖維的定向排列,實(shí)現(xiàn)了力學(xué)和熱學(xué)性能的各向異性及在某個方向上力學(xué)性能的顯著提升。
72.實(shí)施例2
73.以原料總重20g為基準(zhǔn),按照以下步驟制備短纖維原料增韌的低膨脹玻璃基三元復(fù)合材料,模具尺寸φ35mm
×
40mm。
74.1)漿料制備:按照高硼硅玻璃粉原料、β-鋰霞石粉原料、短纖維原料為60wt%、30wt%、10wt%的比例,首先稱取12g粒徑為0.7~0.9μm的高硼硅玻璃粉原料和6g粒徑為0.5~0.7μm的β-鋰霞石粉原料,再稱取40g直徑為3mm的氧化鋯球,然后量取14.4ml高純水(占總固體粉料質(zhì)量比為72%),2ml 5%的pva溶液,使分散劑占總固體粉料的0.5wt%,在氧化鋯的球磨罐中混合,將球磨罐放入球磨機(jī)中,在230rpm/min下球磨混合30min后,然后
再向球磨罐中再加入2g氧化鋯纖維(直徑為3.5μm,長徑比為30~40),在240rpm/min下繼續(xù)球磨混合25min,得到均勻漿料。將漿料過200目篩,然后在電動機(jī)械攪拌條件下用氫氧化鈉溶液調(diào)節(jié)漿料的ph值為10,獲得固相含量為55%、粘度為26.3mpa
·
s的三元復(fù)合物漿料。將三元復(fù)合物漿料放置于真空箱中,進(jìn)行真空除泡15min,真空度為-0.03mpa,獲得的漿料待用。
75.2)注漿:將上述除泡后的三元復(fù)合物漿料以45
°
傾斜角緩慢注入含水量為20%,尺寸為φ35mm
×
40mm的石膏模具中。
76.3)磁場中成型:將裝有漿料的模具固定在支架上,放入強(qiáng)磁體的磁場中,在重力為2g,磁場強(qiáng)度為12t的條件下磁化35分鐘,待漿料干燥后,緩慢取出模具;靜置固化2h后,脫模,獲得尺寸為φ35mm
×
25mm的坯體。
77.4)坯體干燥:將坯體在室溫下干燥2天,然后將其放置在烘箱中,35℃條件下干燥14天。
78.5)燒結(jié):將干燥后的坯體放入馬弗爐中,進(jìn)行真空無壓燒結(jié)。燒結(jié)過程為:先緩慢升溫至850℃,真空條件下保溫10h;然后降至650℃,保溫2h,然后降至550℃,保溫2h,最后再降至400℃,隨爐自然冷卻至室溫,得到尺寸為φ30mm
×
12mm復(fù)合材料。
79.本實(shí)施例所得的復(fù)合材料密度為2.58g/cm3,與普通注漿成型法制備的樣品(2.45g/cm3)相比,樣品內(nèi)部更加致密。在垂直于纖維排列方向上的抗彎強(qiáng)度為154mpa,在平行于纖維排列方向上的抗彎強(qiáng)度為98mpa。
80.實(shí)施例3
81.以原料總重20g為基準(zhǔn),按照以下步驟制備短纖維原料增韌的低膨脹玻璃基三元復(fù)合材料,模具尺寸φ35mm
×
40mm。
82.1)漿料制備:按照高硼硅玻璃粉原料、β-鋰霞石粉原料、短纖維原料50wt%、33wt%、17wt%的比例,首先稱取10g粒徑為0.5~0.7μm的高硼硅玻璃粉原料和6.6g粒徑為0.7~0.9μm的β-鋰霞石粉原料,再稱取40g直徑為3mm的氧化鋯球,然后量取18.8ml高純水(占總固體粉料質(zhì)量比為94%),1.2ml 5%的檸檬酸銨溶液,使分散劑占總固體粉料的0.3%,在氧化鋯的球磨罐中混合,將球磨罐放入球磨機(jī)中,在230rpm/min下球磨混合15min后,然后再向球磨罐中再加入3.4g鈦酸鉛纖維(直徑為2.5μm,長徑比為20~30),在230rpm/min下繼續(xù)球磨混合20min,得到均勻漿料。將漿料過120目篩,然后在電動機(jī)械攪拌條件下用氨水調(diào)節(jié)漿料的ph值為8,獲得固相含量為50%、粘度為9.02mpa
·
s的均勻穩(wěn)定的三元復(fù)合物漿料。將三元復(fù)合物漿料放置于真空箱中,進(jìn)行真空除泡12min,真空度為-0.03mpa,獲得的漿料待用。
83.2)注漿:將上述除泡后的三元復(fù)合物漿料以45
°
傾斜角緩慢注入含水量為15%、尺寸為φ35mm
×
40mm的石膏模具中。
84.3)磁場中成型:將裝有漿料的模具固定在支架上,放入強(qiáng)磁體的磁場中,在重力為2g,磁場強(qiáng)度為16t的條件下磁化45分鐘,待漿料干燥后,緩慢取出模具;靜置固化2h后,脫模,獲得尺寸為φ35mm
×
25mm的坯體。
85.4)坯體干燥:將坯體在室溫下干燥2天,然后將其放置在烘箱中,30℃條件下干燥15天。
86.5)燒結(jié):將干燥后的坯體放入馬弗爐中,進(jìn)行真空無壓燒結(jié)。燒結(jié)過程為:先緩慢
升溫至790℃,真空條件下保溫8h;然后降至650℃,保溫2h,然后降至550℃,保溫2h,最后再降至400℃,隨爐自然冷卻至室溫。
87.得到尺寸為φ30mm
×
11mm復(fù)合材料,本實(shí)施例所得的復(fù)合材料密度為2.62g/cm3。在垂直于纖維排列方向上的抗彎強(qiáng)度為135mpa,在平行于纖維排列方向上的抗彎強(qiáng)度為86mpa。
88.實(shí)施例4
89.以原料總重20g為基準(zhǔn),按照以下步驟制備短纖維原料增強(qiáng)的低膨脹玻璃基三元復(fù)合材料,模具尺寸φ35mm
×
40mm。
90.1)漿料制備:按照高硼硅玻璃粉原料、β-鋰霞石粉原料、短纖維原料為55wt%、27wt%、18wt%的比例,首先稱取11g粒徑為0.7~0.9μm的高硼硅玻璃粉原料和5.4g粒徑為0.2~0.5μm的β-鋰霞石粉原料,再稱取40g直徑為5mm的氧化鋯球,然后量取10.4ml高純水(占總固體粉料質(zhì)量比為52%),0.4ml 5%的檸檬酸胺溶液,使分散劑占總固體粉料的0.1wt%,在氧化鋯的球磨罐中混合,將球磨罐放入球磨機(jī)中,在230rpm/min的轉(zhuǎn)速下球磨混合30min后,然后再向球磨罐中再加入3.6g氧化鋅纖維(直徑為0.5μm,長徑比為20~30),在230rpm/min下繼續(xù)球磨混合30min,得到均勻漿料。將漿料過200目篩,然后在電動機(jī)械攪拌條件下用氫氧化鈉溶液調(diào)節(jié)漿料的ph值為11,獲得固相含量為65wt%、粘度為70mpa
·
s的三元復(fù)合物漿料。將三元復(fù)合物漿料放置于真空箱中,進(jìn)行真空除泡10min,真空度為-0.01mpa,獲得的漿料待用。
91.2)注漿:將上述除泡后的三元復(fù)合物漿料以45
°
傾斜角緩慢注入含水量為25%,尺寸為φ35mm
×
40mm的石膏模具中。
92.3)磁場中成型:將裝有漿料的模具固定在支架上,放入強(qiáng)磁體的磁場中,在重力為2g,磁場強(qiáng)度為12t的條件下磁化30分鐘,待漿料干燥后,緩慢取出模具;靜置固化1.5h后,脫模,獲得尺寸為φ35mm
×
25mm的坯體。
93.4)坯體干燥:將坯體在室溫下干燥3天,然后將其放置在烘箱中,38℃條件下干燥13天。
94.5)燒結(jié):將干燥后的坯體放入馬弗爐中,進(jìn)行真空無壓燒結(jié)。燒結(jié)過程為:先緩慢升溫至760℃,真空氣氛下保溫6h,然后降至650℃,保溫2h,然后降至550℃,保溫2h,最后再降至400℃,隨爐自然冷卻至室溫,得到尺寸為φ32mm
×
10mm復(fù)合材料。本實(shí)施例所得的復(fù)合材料密度為2.37g/cm3。在垂直于纖維排列方向上的抗彎強(qiáng)度為124mpa,在平行于纖維排列方向上的抗彎強(qiáng)度為72mpa。
95.實(shí)施例5
96.以原料總重20g為基準(zhǔn),按照以下步驟制備短纖維原料增韌的低膨脹玻璃基三元復(fù)合材料,模具尺寸φ35mm
×
40mm。
97.1)漿料制備:按照高硼硅玻璃粉原料、β-鋰霞石粉原料、短纖維原料為55wt%、29wt%、16wt%的比例,首先稱取11g粒徑為0.5~0.7μm的高硼硅玻璃粉原料和5.8g粒徑為0.2~0.5μm的β-鋰霞石粉原料,再稱取40g直徑為5mm的氧化鋯球,然后量取10ml高純水(占總固體粉料質(zhì)量比為50%),0.4ml 5%的檸檬酸銨溶液,使分散劑占總固體粉料的0.1%wt,在氧化鋯的球磨罐中混合,將球磨罐放入球磨機(jī)中,在230rpm/min的轉(zhuǎn)速下球磨混合30min后,然后再向球磨罐中再加入3.2g氮化硅纖維(直徑為2.5μm,長徑比為20~30),在
230rpm/min下繼續(xù)球磨混合30min,得到均勻漿料。將漿料過160目篩,然后在電動機(jī)械攪拌條件下用氫氧化鈉溶液調(diào)節(jié)漿料的ph值為11,獲得固相含量為58wt%、粘度為32.6mpa
·
s的三元復(fù)合物漿料。將三元復(fù)合物漿料放置于真空箱中,進(jìn)行真空除泡10min,真空度為-0.01mpa,獲得的漿料待用。
98.2)注漿:將上述除泡后的三元復(fù)合物漿料以45
°
傾斜角緩慢注入含水量為18%,尺寸為φ35mm
×
40mm的石膏模具中。
99.3)磁場中成型:將裝有漿料的模具固定在支架上,放入強(qiáng)磁體的磁場中,在重力為2g,磁場強(qiáng)度為16t的條件下磁化35分鐘,待漿料干燥后,緩慢取出模具;靜置固化1.5h后,脫模,獲得尺寸為φ35mm
×
25mm的坯體。
100.4)坯體干燥:將坯體在室溫下干燥2天,然后將其放置在烘箱中,33℃條件下干燥14天。
101.5)燒結(jié):將干燥后的坯體放入馬弗爐中,進(jìn)行真空無壓燒結(jié)。燒結(jié)過程為:先緩慢升溫至760℃,真空條件下保溫8h,然后降至650℃,保溫2h,然后降至550℃,保溫2h,最后再降至400℃,隨爐自然冷卻至室溫,得到尺寸為φ31mm
×
10mm復(fù)合材料。本實(shí)施例所得的復(fù)合材料密度為2.18g/cm3。在垂直于纖維排列方向上的抗彎強(qiáng)度為286mpa,在平行于纖維排列方向上的抗彎強(qiáng)度為143mpa。
102.實(shí)施例6
103.以原料總重20g為基準(zhǔn),按照以下步驟制備短纖維原料增韌的低膨脹玻璃基三元復(fù)合材料,模具尺寸φ35mm
×
40mm。
104.1)漿料制備:按照高硼硅玻璃粉原料、β-鋰霞石粉原料、短纖維原料為60wt%、28wt%、12wt%的比例,首先稱取12g粒徑為0.7~0.9μm的高硼硅玻璃粉原料和5.6g粒徑為0.5~0.7μm的β-鋰霞石粉原料,再稱取40g直徑為5mm的氧化鋯球,然后量取11.5ml高純水(占總固體粉料質(zhì)量比為51.8%),0.8ml5%的檸檬酸胺溶液,使分散劑占總固體粉料的0.2%,在氧化鋯的球磨罐中混合,將球磨罐放入球磨機(jī)中,在230rpm/min的轉(zhuǎn)速下球磨混合30min后,然后再向球磨罐中再加入2.4g硼化鋯纖維(直徑為5μm,長徑比為20~30),在250rpm/min下繼續(xù)球磨混合35min,得到均勻漿料。將漿料過100目篩,然后在電動機(jī)械攪拌條件下用氫氧化鈉溶液調(diào)節(jié)漿料的ph值為11,獲得固相含量為62wt%、粘度為65.3mpa
·
s的三元復(fù)合物漿料。將三元復(fù)合物漿料放置于真空箱中,進(jìn)行真空除泡12min,真空度為-0.03mpa,獲得的漿料待用。
105.2)注漿:將上述除泡后的三元復(fù)合物漿料以45
°
傾斜角緩慢注入含水量為15%、尺寸為φ35mm
×
40mm的石膏模具中。
106.3)磁場中成型:將裝有漿料的模具固定在支架上,放入強(qiáng)磁體的磁場中,在重力為1g,磁場強(qiáng)度為16t的條件下磁化30分鐘,待漿料干燥后,緩慢取出模具;靜置固化1.5h后,脫模,獲得尺寸為φ35mm
×
25mm的坯體。
107.4)坯體干燥:將坯體在室溫下干燥2天,然后將其放置在烘箱中,35℃條件下干燥15天。
108.5)燒結(jié):將干燥后的坯體放入馬弗爐中,進(jìn)行真空無壓燒結(jié)。燒結(jié)過程為:先緩慢升溫至850℃,真空條件下保溫10h,然后降至650℃,保溫2h,然后降至550℃,保溫2h,最后再降至400℃,隨爐自然冷卻至室溫,得到尺寸為φ30mm
×
11mm復(fù)合材料。本實(shí)施例所得的
0.03mpa,獲得的漿料待用。
120.2)注漿:將上述除泡后的三元復(fù)合物漿料以45
°
傾斜角緩慢注入含水量為20%、尺寸為φ35mm
×
40mm的石膏模具中。
121.3)磁場中成型:將裝有漿料的模具固定在支架上,放入強(qiáng)磁體的磁場中,在重力為2g,磁場強(qiáng)度為16t的條件下磁化30分鐘,待漿料干燥后,緩慢取出模具;靜置固化1.5h后,脫模,獲得尺寸為φ35mm
×
25mm的坯體。
122.4)坯體干燥:將坯體在室溫下干燥2天,然后將其放置在烘箱中,35℃條件下干燥15天。
123.5)燒結(jié):將干燥后的坯體放入馬弗爐中,進(jìn)行真空無壓燒結(jié)。燒結(jié)過程為:先緩慢升溫至760℃,真空條件下保溫8h,然后降至650℃,保溫2h,然后降至550℃,保溫2h,最后再降至400℃,隨爐自然冷卻至室溫,得到尺寸為φ30mm
×
11mm復(fù)合材料。
124.本實(shí)施例所得的復(fù)合材料密度為1.98g/cm3。在垂直于纖維排列方向上的抗彎強(qiáng)度為127mpa,在平行于纖維排列方向上的抗彎強(qiáng)度為75mpa。
125.實(shí)施例9
126.以原料總重20g為基準(zhǔn),按照以下步驟制備短纖維原料增韌的低膨脹玻璃基三元復(fù)合材料,模具尺寸φ35mm
×
40mm。
127.1)漿料制備:按照高硼硅玻璃粉原料、β-鋰霞石粉原料、莫來石纖維為58wt%、28wt%、14wt%的比例,首先稱取11.6g粒徑為0.7~0.9μm的高硼硅玻璃粉原料和5.6g粒徑為0.2~0.5μm的β-鋰霞石粉原料,再稱取40g直徑為5mm的氧化鋯球,然后量取13ml高純水(占總固體粉料質(zhì)量比為51.8%),2ml 5%的乙二醇溶液,使分散劑占總固體粉料的0.5wt%,在氧化鋯的球磨罐中混合,將球磨罐放入球磨機(jī)中,在230rpm/min的轉(zhuǎn)速下球磨混合30min后,然后再向球磨罐中再加入2.8g硫酸鈣纖維(直徑為1μm,長徑比為30~40),在230rpm/min下繼續(xù)球磨混合30min,得到均勻漿料。將漿料過180目篩,然后在電動機(jī)械攪拌條件下用氫氧化鈉溶液調(diào)節(jié)漿料的ph值為11,獲得固相含量為57wt%、粘度為34.2mpa
·
s的三元復(fù)合物漿料。將三元復(fù)合物漿料放置于真空箱中,進(jìn)行真空除泡15min,真空度為-0.03mpa,獲得的漿料待用。
128.2)注漿:將上述除泡后的三元復(fù)合物漿料以45
°
傾斜角緩慢注入含水量為20%、尺寸為φ35mm
×
40mm的石膏模具中。
129.3)磁場中成型:將裝有漿料的模具固定在支架上,放入強(qiáng)磁體的磁場中,在重力為1g,磁場強(qiáng)度為16t的條件下磁化35分鐘,待漿料干燥后,緩慢取出模具;靜置固化1.5h后,脫模,獲得尺寸為φ35mm
×
25mm的坯體。
130.4)坯體干燥:將坯體在室溫下干燥3天,然后將其放置在烘箱中,33℃條件下干燥15天。
131.5)燒結(jié):將干燥后的坯體放入馬弗爐中,進(jìn)行真空無壓燒結(jié)。燒結(jié)過程為:先緩慢升溫至760℃,真空條件下保溫8h,然后降至650℃,保溫2h,然后降至550℃,保溫2h,最后再降至400℃,隨爐自然冷卻至室溫,得到尺寸為φ30mm
×
11mm復(fù)合材料。
132.本實(shí)施例所得的復(fù)合材料密度為2.04g/cm3。在垂直于纖維排列方向上的抗彎強(qiáng)度為130mpa,在平行于纖維排列方向上的抗彎強(qiáng)度為72mpa。技術(shù)特征:
1.一種定向排列的短纖維增強(qiáng)低膨脹玻璃基復(fù)合材料的制備方法,其特征在于,包括以下步驟:1)漿料制備1.1)分別稱取原料總量50%~60%質(zhì)量比的高硼硅玻璃粉原料、原料總量27%~33%質(zhì)量比的β-鋰霞石粉原料和原料總量10%~18%質(zhì)量比的短纖維原料;1.2)將高硼硅玻璃粉原料、β-鋰霞石粉原料加入到球磨罐中,加入占原料總量50%~94%質(zhì)量比的高純水,再加入占原料總量0.1%~0.5%質(zhì)量比的分散劑溶液,加入直徑為3~5mm的氧化鋯球,球磨混合均勻,再加入相應(yīng)的短纖維原料,繼續(xù)球磨混合20~40分鐘得到均勻漿料;氧化鋯球的質(zhì)量與原料總量的比為2:1;1.3)將漿料過100~200目篩,過篩后的漿料在攪拌條件下調(diào)節(jié)ph值為8~11,得到均勻穩(wěn)定的三元復(fù)合物漿料;1.4)將三元復(fù)合物漿料中的氣泡抽真空去除;2)注漿將去除氣泡的三元復(fù)合物漿料傾斜45度緩慢倒入預(yù)先制備好的具有一定濕度的模具中;3)磁場中成型將步驟2)中的模具放入磁場中,在磁場中進(jìn)行磁化,完成纖維有序排列和復(fù)合材料的成型;漿料干燥后將模具取出,靜置固化后,脫模;所述磁場的磁場強(qiáng)度為12~16t,重力場為1g~2g,在磁場中進(jìn)行磁化的時間為30~45分鐘;4)將脫模后的坯體進(jìn)行干燥;5)將干燥后的坯體在760℃~850℃進(jìn)行真空無壓燒結(jié),得到定向排列的短纖維增強(qiáng)低膨脹玻璃基復(fù)合材料。2.根據(jù)權(quán)利要求1所述的定向排列的短纖維增強(qiáng)低膨脹玻璃基復(fù)合材料的制備方法,其特征在于:步驟2)中,所述具有一定濕度的模具中水分含量為15%~25%。3.根據(jù)權(quán)利要求2所述的定向排列的短纖維增強(qiáng)低膨脹玻璃基復(fù)合材料的制備方法,其特征在于:步驟1.1)中,所述高硼硅玻璃粉原料的粒徑為0.5~0.9μm;所述β-鋰霞石粉原料的粒徑為0.2~0.9μm;所述短纖維原料為莫來石、氧化鋯、氧化鋅、鈦酸鉛、碳化硅、氮化硅、硼化鋯、硫酸鈣、玻璃纖維中的其中一種;所述短纖維原料的直徑為0.5~5μm,短纖維原料的長徑比為20~40。4.根據(jù)權(quán)利要求3所述的定向排列的短纖維增強(qiáng)低膨脹玻璃基復(fù)合材料的制備方法,其特征在于:步驟1.3)中,調(diào)節(jié)ph的方法為:在電動機(jī)械攪拌條件下,用氨水或氫氧化鈉調(diào)節(jié)。5.根據(jù)權(quán)利要求1-4任一所述的定向排列的短纖維增強(qiáng)低膨脹玻璃基復(fù)合材料的制備方法,其特征在于:步驟1.2)中,所述分散劑溶液為5%濃度的聚乙烯醇、乙二醇和檸檬酸銨溶液中的其中一種。
6.根據(jù)權(quán)利要求5所述的定向排列的短纖維增強(qiáng)低膨脹玻璃基復(fù)合材料的制備方法,其特征在于,步驟1.4)中,所述三元復(fù)合物漿料中的氣泡去除的方法為:將三元復(fù)合物漿料放入真空箱中,在真空度為-0.01~-0.03mpa條件下保持10~15min,將氣泡去除。7.根據(jù)權(quán)利要求6所述的定向排列的短纖維增強(qiáng)低膨脹玻璃基復(fù)合材料的制備方法,其特征在于:步驟4)中,所述干燥方法為:先在室溫下干燥2-3天,再放入烘箱在30~38℃下進(jìn)行恒溫干燥10~15天。8.根據(jù)權(quán)利要求7所述的定向排列的短纖維增強(qiáng)低膨脹玻璃基復(fù)合材料的制備方法,其特征在于:步驟5)中,真空無壓燒結(jié)的過程為:將干燥后的坯體放入馬弗爐中,先緩慢升溫至760~850℃,真空條件下保溫5~10h;然后降至650℃,保溫2h,然后降至550℃,保溫2h,最后再降至400℃,隨爐自然冷卻至室溫。9.根據(jù)權(quán)利要求8所述的定向排列的短纖維增強(qiáng)低膨脹玻璃基復(fù)合材料的制備方法,其特征在于:步驟1.1)中分別稱取的高硼硅玻璃粉原料、β-鋰霞石粉原料和莫來石短纖維原料的質(zhì)量比為54%、31%和15%;步驟1.2)中,加入高純水的量占原料總量的62.5%,加入分散劑溶液的量占原料總量0.2%;步驟1.3)中,將漿料過200目篩;過篩后的漿料在攪拌條件下調(diào)節(jié)ph值為9;步驟2)中,所述具有一定濕度模具中水分含量為20%;步驟3中,所述磁場的強(qiáng)度為16t,重力場為1g,磁化時間為30分鐘;步驟5)中,真空無壓燒結(jié)溫度為805℃。10.一種定向排列的短纖維增強(qiáng)低膨脹玻璃基復(fù)合材料,其特征在于:采用權(quán)利要求1-9任一所述定向排列的短纖維增強(qiáng)低膨脹玻璃基復(fù)合材料的制備方法制備。
技術(shù)總結(jié)
本發(fā)明涉及性能各向異性復(fù)合材料的制備方法,具體涉及定向排列的短纖維增強(qiáng)低膨脹玻璃基復(fù)合材料的制備方法及復(fù)合材料。解決了現(xiàn)有技術(shù)所制備的復(fù)合材料中短纖維原料隨機(jī)無序排布而無法實(shí)現(xiàn)某個方向上力學(xué)性能、熱學(xué)性能提升的技術(shù)問題。本發(fā)明制備方法,包括以下步驟:1)漿料制備;2)注漿;3)磁場中成型;4)將脫模后的坯體進(jìn)行干燥;5)將干燥后的坯體在760℃~850℃進(jìn)行真空無壓燒結(jié),得到定向排列的短纖維原料增強(qiáng)低膨脹玻璃基復(fù)合材料。本發(fā)明制備方法,在復(fù)合材料注漿成型過程中,通過強(qiáng)磁場的誘導(dǎo),實(shí)現(xiàn)纖維在復(fù)合材料中的定向排列,獲得在力學(xué)、熱學(xué)等性能上具有各向異性的復(fù)合材料,滿足在特殊環(huán)境應(yīng)用下對復(fù)合材料性能的要求。能的要求。能的要求。
技術(shù)研發(fā)人員:崔曉霞 郭海濤 許彥濤
受保護(hù)的技術(shù)使用者:中國科學(xué)院西安光學(xué)精密機(jī)械研究所
技術(shù)研發(fā)日:2022.07.05
技術(shù)公布日:2022/11/8 專利名稱:鐵硅鋁軟磁粉末及其制造方法
技術(shù)領(lǐng)域:
本發(fā)明涉及一種鐵硅鋁軟磁粉末及其制造方法,屬于金屬磁性材料領(lǐng)域。
背景技術(shù):
軟磁材料從純鐵、硅鋼到坡莫合金等已有100多年的發(fā)展歷史;近二十多年來先 后發(fā)展起來的非晶態(tài)合金和納米晶合金等新型軟磁合金材料,使軟磁材料的組織結(jié)構(gòu)從晶 態(tài)躍向非晶態(tài),又從非晶態(tài)發(fā)展為納米晶態(tài),從而把軟磁合金
新材料的研發(fā)與應(yīng)用推向了 一個新的高潮。材料研究工作者曾長期致力于研究同時具有高飽和磁感應(yīng)強(qiáng)度、高磁導(dǎo)率、 低損耗的軟磁材料,謂之“二高一低”的“理想”軟磁材料,但是始終未能實(shí)現(xiàn)。金屬軟磁合 金不僅微觀結(jié)構(gòu)新穎、不同于晶態(tài)和非晶態(tài),而且具有綜合的優(yōu)異軟磁特性、即具有較高飽 和磁感應(yīng)強(qiáng)度、高磁導(dǎo)率、低損耗等;與此同時,該合金還具有生產(chǎn)工藝簡單、成本低、無污 染等特點(diǎn)。因而可以講,金屬軟磁合金的出現(xiàn)是軟磁材料的一個突破性進(jìn)展,它解決了人 們長期努力研究而未能解決的難題;其貢獻(xiàn)就在于①找到了一條使狗基合金晶粒細(xì)化到 1 20納米而飽和磁致伸縮系數(shù)和磁晶各向異性常數(shù)又同時趨于零的途徑;②改變了以往 各類軟磁材料的磁導(dǎo)率、損耗與飽和磁感應(yīng)強(qiáng)度相沖突,磁性能與成本相沖突的狀況。但具 體到生產(chǎn)軟磁材料,國內(nèi)水平與發(fā)達(dá)國家水平存在著差距?,F(xiàn)代電子技術(shù)向高頻、高效、大 功率、小型、節(jié)能方向發(fā)展,對軟磁材料提出了越來越高標(biāo)準(zhǔn)的要求。發(fā)明內(nèi)容
本發(fā)明的目的是為解決上述技術(shù)問題,提供一種鐵硅鋁軟磁粉末。本發(fā)明的上述技術(shù)目的是通過以下技術(shù)方案得以實(shí)現(xiàn)的鐵硅鋁軟磁粉末,它的組成成分中含有9 10wt%的硅,5 6wt%的鋁,0. 5 lwt%的 鉻,余量為鐵。通常作為微量元素添加入鐵硅鋁軟磁粉末的金屬元素有Mn、La、Ni、Ta。經(jīng)過反 復(fù)實(shí)驗(yàn),發(fā)明人添加了 Cr,這改善了材料的塑性,有利于材料的扁平化處理。如采用球磨處 理工藝對鐵硅
鋁合金料進(jìn)行改型處理,可獲得扁平薄片狀外形結(jié)構(gòu),也使其晶粒細(xì)化并獲 得晶粒尺寸小于交換作用長度的納米晶結(jié)構(gòu),材料的微波復(fù)磁導(dǎo)率實(shí)部和虛部均有顯著提 高,介電常數(shù)有效降低。本發(fā)明的另一個目的是提供上述鐵硅鋁軟磁粉末的制造方法。鐵硅鋁軟磁粉末的制造方法,包括以下步驟①將鐵鋁合金、鐵粉、硅粉和鉻粉冶煉成含硅9 10wt%、鋁5 6wt%、鉻0.5 lwt% 的合金;②將步驟①制得的合金破碎成合金塊,將該合金塊倒入球磨機(jī)并在該在球磨機(jī)中添加 占合金塊質(zhì)量3 6%的分散劑,然后通過球磨機(jī)將合金塊研磨成100目以下的合金粉末; 所述分散劑為十二烷基苯磺酸、聚乙二醇、
硅烷偶聯(lián)劑和正己烷的混合物;③對經(jīng)過步驟②制得的合金粉末進(jìn)行熱處理,熱處理包括加熱、保溫和冷卻三個階段,所述三個階段均在以氮?dú)鉃楸Wo(hù)氣體的條件下進(jìn)行,保溫階段的溫度控制為900 950°C, 冷卻階段以彡IO0C / min的冷卻速度冷卻至室溫。本發(fā)明上述技術(shù)方案中,不用純鋁作為原料,其原因在于,由于鋁的熔點(diǎn)低,在 660°C左右,而鐵水的溫度在1500°C上下,使得鋁在溶解的過程中容易揮發(fā),所以鋁含量控 制難度大,另外由于鋁的密度低,合金溶液的上半部分鋁的含量高,容易造成合金成分的均 勻性差。而本發(fā)明采用鐵鋁合金作為原料之一,鐵鋁合金熔點(diǎn)要比鋁的熔點(diǎn)高300°C左右, 而且密度大,溶解時容易下沉,所以有效地解決了上述難題。本發(fā)明上述技術(shù)方案中,原料中添加有鉻,且添加量控制在一定范圍內(nèi)使得經(jīng)過 步驟①制得的合金中鉻元素含量控制在0. 5 lwt%。鉻的添加有利于改善材料的塑性,有 利于材料的扁平化處理。如采用球磨處理工藝對鐵硅鋁合金料進(jìn)行改型處理,可獲得扁平 薄片狀外形結(jié)構(gòu),也使其晶粒細(xì)化并獲得晶粒尺寸小于交換作用長度的納米晶結(jié)構(gòu),材料 的微波復(fù)磁導(dǎo)率實(shí)部和虛部均有顯著提高,介電常數(shù)有效降低。采用球磨工藝要克服一個難點(diǎn)是確保鐵硅鋁合金在球磨的過程中表面不要被氧 化,由于在球磨高速轉(zhuǎn)動的情況下,磨機(jī)連續(xù)工作,球磨筒體內(nèi)的溫度就可以達(dá)到180°c以 上,在這樣的溫度下,細(xì)小的金屬粉末的表面會被氧化,而氧化的結(jié)果會造成粉體的功耗 大,導(dǎo)磁率降低。而在進(jìn)行球磨的同時持續(xù)加入質(zhì)量分?jǐn)?shù)為3 6%的分散劑就可以使球磨 桶內(nèi)的溫度降低到80 90°C之間,大大降低了粉末表面的氧化程度;所述分散劑是十二烷 基苯磺酸、聚乙二醇、硅烷偶聯(lián)劑和正己烷的混合物;該分散劑具有揮發(fā)性,在后續(xù)工藝熱 處理時能夠完全揮發(fā)掉所以不會影響粉末的物理成分,不會對粉末的質(zhì)量造成不良影響。熱處理是磁性材料制備的常用手段,通過熱處理不僅可以去掉磁性合金粉末的內(nèi) 應(yīng)力,還能改善它的磁性。熱處理時的溫度通常以該材料的居里點(diǎn)為溫度界限,居里點(diǎn)也稱 居里溫度或磁性轉(zhuǎn)變點(diǎn),是指材料可以在鐵磁體和順磁體之間改變的溫度,即鐵電體從鐵 電相轉(zhuǎn)變成順電相引的相變溫度。低于居里點(diǎn)溫度時該物質(zhì)成為鐵磁體,此時和材料有關(guān) 的磁場很難改變。當(dāng)溫度高于居里點(diǎn)溫度時,該物質(zhì)成為順磁體,磁體的磁場很容易隨周 圍磁場的改變而改變。基于這一理論,熱處理時通常要將磁性材料溫度提高到居里溫度以 上,另外由于相轉(zhuǎn)變需要一定的時間,因此當(dāng)金屬工件表面達(dá)到要求的加熱溫度時,還須在 此溫度保持一定時間,使內(nèi)外溫度一致,以使顯微組織轉(zhuǎn)變完全,這段時間稱為保溫時間。 另外降溫速度也是熱處理工藝的重要參數(shù)之一。在原料中加入鉻之后,這些控制參數(shù)都要 進(jìn)行修正。在本發(fā)明人經(jīng)過多次試驗(yàn)后最終確定了保溫階段的溫度控制為900 950°C,冷 卻階段以彡IO0C / min的冷卻速度冷卻至室溫這樣的技術(shù)方案。綜上所述,本發(fā)明具有以下有益效果
1、本發(fā)明鐵硅鋁軟磁粉末具有磁性好的優(yōu)點(diǎn);
2、本發(fā)明方法不僅可以生產(chǎn)出質(zhì)量優(yōu)異的鐵硅鋁軟磁粉末,并且還具有有效降低生產(chǎn) 成本的優(yōu)點(diǎn)。
具體實(shí)施例方式
本具體實(shí)施例僅僅是對本發(fā)明的解釋,其并不是對本發(fā)明的限制,本領(lǐng)域技術(shù)人 員在閱讀完本說明書后可以根據(jù)需要對本實(shí)施例做出沒有創(chuàng)造性貢獻(xiàn)的修改,但只要在本 發(fā)明的權(quán)利要求范圍內(nèi)都受到專利法的保護(hù)。
實(shí)施例一鐵硅鋁軟磁粉末,它的組成成分中中含有9wt%的硅,6wt%的鋁,0. 5%的鉻,余量為鐵。上述鐵硅鋁軟磁粉末的制造方法,是通過以下步驟制得的①將鐵鋁合金、鐵粉、硅粉和鉻粉冶煉成含硅9wt%、鋁6wt%、鉻0.5wt%的合金;②將步驟①制得的合金破碎成合金塊,將該合金塊倒入球磨機(jī)并在該在球磨機(jī)中添 加占合金塊質(zhì)量3%的分散劑,然后通過球磨機(jī)將合金塊研磨成100目以下的合金粉末;所 述分散劑為十二烷基苯磺酸、聚乙二醇、硅烷偶聯(lián)劑和正己烷的混合物;③對經(jīng)過步驟②制得的合金粉末進(jìn)行熱處理,熱處理包括加熱、保溫和冷卻三個階 段,所述三個階段均在以氮?dú)鉃楸Wo(hù)氣體的條件下進(jìn)行;熱處理設(shè)備的加熱段長度設(shè)置為 3米,分3個溫區(qū),3個溫區(qū)溫度分別700°C,SOO0C,900°C ;保溫段設(shè)置為3米,分3個溫區(qū), 3個溫區(qū)溫度統(tǒng)一為900°C,冷卻段設(shè)置為6米,采用高壓冷水沖擊高溫合金液的方法將冷 卻速度控制在10°C /min,冷卻至室溫。實(shí)施例二鐵硅鋁軟磁粉末,它的組成成分中中含有9. 6wt%的硅,5. 4wt%的鋁,0. 8%的鉻,余量為鐵。上述鐵硅鋁軟磁粉末的制造方法,是通過以下步驟制得的①將鐵鋁合金、鐵粉、硅粉和鉻粉冶煉成含硅9.6wt%、鋁5. 、鉻0. 8wt%的合金;②將步驟①制得的合金破碎成合金塊,將該合金塊倒入球磨機(jī)并在該在球磨機(jī)中添 加占合金塊質(zhì)量5%的分散劑,然后通過球磨機(jī)將合金塊研磨成100目以下的合金粉末;所 述分散劑為十二烷基苯磺酸、聚乙二醇、硅烷偶聯(lián)劑和正己烷的混合物;③對經(jīng)過步驟②制得的合金粉末進(jìn)行熱處理,熱處理包括加熱、保溫和冷卻三個階 段,所述三個階段均在以氮?dú)鉃楸Wo(hù)氣體的條件下進(jìn)行;熱處理設(shè)備的加熱段長度設(shè)置為 3米,分3個溫區(qū),3個溫區(qū)溫度分別700°C,SOO0C,900°C ;保溫段設(shè)置為3米,分3個溫區(qū), 3個溫區(qū)溫度統(tǒng)一為930°C,冷卻段設(shè)置為6米,采用高壓冷水沖擊高溫合金液的方法將冷 卻速度控制在15°C /min,冷卻至室溫。實(shí)施例三鐵硅鋁軟磁粉末,它的組成成分中中含有10wt%的硅,5wt%的鋁,lwt%的鉻,余量為鐵。上述鐵硅鋁軟磁粉末的制造方法,是通過以下步驟制得的①將鐵鋁合金、鐵粉、硅粉和鉻粉冶煉成含硅10wt%、鋁6wt%、鉻lwt%的合金;②將步驟①制得的合金破碎成合金塊,將該合金塊倒入球磨機(jī)并在該在球磨機(jī)中添 加占合金塊質(zhì)量6%的分散劑,然后通過球磨機(jī)將合金塊研磨成100目以下的合金粉末;所 述分散劑為十二烷基苯磺酸、聚乙二醇、硅烷偶聯(lián)劑和正己烷的混合物;③對經(jīng)過步驟②制得的合金粉末進(jìn)行熱處理,熱處理包括加熱、保溫和冷卻三個階 段,所述三個階段均在以氮?dú)鉃楸Wo(hù)氣體的條件下進(jìn)行;熱處理設(shè)備的加熱段長度設(shè)置為 3米,分3個溫區(qū),3個溫區(qū)溫度分別700°C,SOO0C,900°C ;保溫段設(shè)置為3米,分3個溫區(qū), 3個溫區(qū)溫度統(tǒng)一為950°C,冷卻段設(shè)置為6米,采用高壓冷水沖擊高溫合金液的方法將冷 卻速度控制在20°C /min,冷卻至室溫。對比例將工業(yè)純鐵、結(jié)晶硅、純鋁投入公稱50公斤的高頻感應(yīng)爐內(nèi)冶煉,澆鑄成化學(xué)成分為5鐵84. 80%、硅9. 53%、鋁5. 62%的合金鑄錠,用機(jī)械方法將合金鑄錠粗破碎成25毫米以下的 料塊,將這些料塊置入具有氫氣保護(hù)氣氛的通用還原爐內(nèi)并在700°C左右的溫度條件下保 溫2小時左右后冷卻,再用穎式
破碎機(jī)進(jìn)一步將這些料塊破碎成小于6毫米的料塊,再用振 動球磨粉碎成100目以下的合金粉末,將該合金粉末置入具有氫氣保護(hù)氣氛的通用還原爐 內(nèi)在900°C左右的溫度條件下保溫1小時進(jìn)行應(yīng)力退火處理,之后篩分。
權(quán)利要求
1.鐵硅鋁軟磁粉末,其特征在于它的組成成分中含有9 10wt%的硅,5% 6wt%的 鋁,0. 5 lwt%的鉻,余量為鐵。
2.權(quán)利要求1所述的鐵硅鋁軟磁粉末的制造方法,其特征在于,包括以下步驟①將鐵鋁合金、鐵粉、硅粉和鉻粉冶煉成含硅9 10wt%、鋁5 6wt%、鉻0.5 lwt%、 余量為鐵的合金;②將步驟①制得的合金破碎成合金塊,將該合金塊倒入球磨機(jī)并在該在球磨機(jī)中添加 占合金塊質(zhì)量3 6%的分散劑,然后通過球磨機(jī)將合金塊研磨成100目以下的合金粉末; 所述分散劑為十二烷基苯磺酸、聚乙二醇、硅烷偶聯(lián)劑和正己烷的混合物;③對經(jīng)過步驟②制得的合金粉末進(jìn)行熱處理,熱處理包括加熱、保溫和冷卻三個階段, 所述三個階段均在以氮?dú)鉃楸Wo(hù)氣體的條件下進(jìn)行,保溫階段的溫度控制為900 950°C, 冷卻階段以彡IO0C / min的冷卻速度冷卻至室溫。
全文摘要
本發(fā)明涉及一種鐵硅鋁軟磁粉末及其制造方法,屬于金屬磁性材料領(lǐng)域。鐵硅鋁軟磁粉末,它的組成成分中含有9~10wt%的硅,5~6wt%的鋁,0.5~1wt%的鉻,余量為鐵。本發(fā)明鐵硅鋁軟磁粉末具有磁性好的優(yōu)點(diǎn);本發(fā)明方法不僅可以生產(chǎn)出質(zhì)量優(yōu)異的鐵硅鋁軟磁粉末,并且還具有有效降低生產(chǎn)成本的優(yōu)點(diǎn)。
文檔編號B22F1/00GK102049515SQ201010604020
公開日2011年5月11日 申請日期2010年12月24日 優(yōu)先權(quán)日2010年12月24日
發(fā)明者劉丙前, 沈偉明 申請人:湖州南潯聞天磁性材料有限公司
聲明:
“鐵硅鋁軟磁粉末及其制造方法” 該技術(shù)專利(論文)所有權(quán)利歸屬于技術(shù)(論文)所有人。僅供學(xué)習(xí)研究,如用于商業(yè)用途,請聯(lián)系該技術(shù)所有人。
我是此專利(論文)的發(fā)明人(作者)