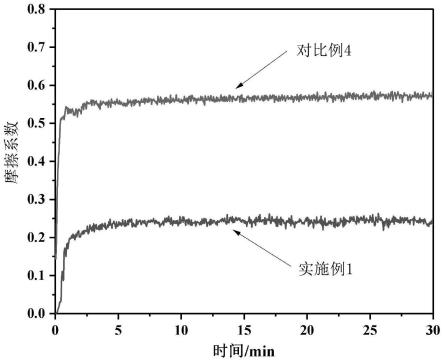
1.本發(fā)明涉及金屬表面處理技術(shù)領(lǐng)域,具體一種面向鋼基件用高溫梯度耐磨涂層及其制備方法。
背景技術(shù):
2.磨損是機(jī)械零件的主要失效形式之一。磨損失效帶來的資源消耗非常巨大,據(jù)統(tǒng)計,我國每年因摩擦磨損造成的經(jīng)濟(jì)損失在1000億人民幣以上。尤其是在高溫工況下,由于材料硬度下降和氧化,將會發(fā)生嚴(yán)重的粘著磨損和氧化磨損,導(dǎo)致劇烈的磨損失效。例如,熱作模具鋼h13往往在高溫下使用,要求具有高的高溫耐磨性,然而當(dāng)溫度超過600℃時其硬度急劇下降,發(fā)生嚴(yán)重的塑性擠出磨損而失效。在材料表面制備高硬度、高耐磨性同時具有低摩擦系數(shù)的合金涂層是修復(fù)失效零部件、延長使用壽命的重要途徑。同時,隨著社會科技技術(shù)的進(jìn)步以及航空航天、機(jī)械車輛和冶金礦山等領(lǐng)域的器械朝著長壽命、高穩(wěn)定的方向發(fā)展,對耐磨涂層材料的性能要求日益提高。
3.涂層制備方法中,激光熔覆技術(shù)具有低稀釋率、熱影響區(qū)小和可精確控制的優(yōu)點從而得到了廣泛的應(yīng)用和推廣。其制備的涂層與基體呈良好冶金結(jié)合,可充分展現(xiàn)出涂層材料的硬度、耐磨性、耐熱性等性能。對于激光熔覆技術(shù)而言,涂層材料的種類及成分設(shè)計至關(guān)重要。目前,激光熔覆涂層合金材料主要有金屬基合金(包括鈷基,鎳基和鐵基)和金屬陶瓷基合金。對于實際生產(chǎn)大量應(yīng)用的鋼鐵零部件來說,鈷基和鎳基合金涂層材料成本高且成分相差大,研究價值不及鐵基材料;鐵基涂層材料具有良好的韌性和一定的耐磨性但高溫硬度低,高溫條件下仍極易磨損。金屬陶瓷基涂層材料往往包含大量硬質(zhì)碳化物,具有高耐磨性,但在熔覆過程中由于韌性差、與基材線膨脹系數(shù)差異大等缺點導(dǎo)致涂層出現(xiàn)易開裂、多道搭接難、厚度低等問題。因此,為進(jìn)一步提高高溫耐磨性,需克服涂層材料熱硬性和易熔覆的矛盾。
4.另外,中國專利(cn 111793773)公開了一種作為刀具材料的金屬間化合物強(qiáng)硬化高速鋼(塊體材料),該鋼具有比傳統(tǒng)碳化物高速鋼更好的耐熱性和比硬質(zhì)合金更好的韌性。然而,雖然金屬間化合物相較于碳化物具有更好的耐熱性,但耐磨性稍顯不足,無法更進(jìn)一步提高材料高溫耐磨性。此外,不同于塊體材料,涂層材料還需要考慮稀釋率帶來的性能改變以及解決不同層之間容易產(chǎn)生熱應(yīng)力和界面應(yīng)力,容易導(dǎo)致裂紋萌生等問題。
技術(shù)實現(xiàn)要素:
5.針對現(xiàn)有技術(shù)的不足,本發(fā)明的第一個目的是提供一種具備硬度高、熱硬性好、韌性佳、易涂覆、具有優(yōu)異高溫耐磨性的梯度涂層。
6.本發(fā)明第二目的在于,提供復(fù)合有所述的高溫梯度耐磨涂層的制備方法。
7.本發(fā)明第三目的在于,提供包含所述耐磨涂層的梯度耐磨涂層材料以及制備方法。
8.一種高溫梯度耐磨涂層,包括底層、過渡層、耐磨層,以及在耐磨層表面硫化形成
的硫化層;
9.所述的底層包括馬氏體基體以及彌散在其中的金屬間化合物;
10.所述的過渡層、耐磨層均包括馬氏體基體以及彌散分布在其中的金屬間化合物和碳化物;
11.其中,過渡層、耐磨層中的金屬間化合物的含量大于底層的金屬間化合物的含量;耐磨層中的碳化物的含量大于過渡層中的碳化物的含量;且所述的金屬間化合物包含a7b6型金屬間化合物。
12.本發(fā)明所述的高溫梯度耐磨涂層,分為四層,依次為底層、過渡層、耐磨層和硫化層。其中,底層采用低合金含量金屬間化合物強(qiáng)化高速鋼粉末,過渡層采用高合金含量金屬間化合物強(qiáng)化高速鋼粉末+低含量碳化物粉末,耐磨層采用高合金含量金屬間化合物強(qiáng)化高速鋼粉末+高含量碳化物粉末。本發(fā)明研究發(fā)現(xiàn),所述的金屬間化合物以及碳化物雙梯度控制的層級涂層具有優(yōu)異的協(xié)同性,可以顯著改善涂層的高溫(如700℃)耐磨性能。
13.本發(fā)明底層-過渡層-耐磨層-硫化層成分以及所述的底層-過渡層(耐磨層)的金屬間化合物的梯度控制以及過渡層-耐磨層之間的碳化物梯度控制的聯(lián)合是成功形成無裂紋涂層和協(xié)同改善涂層高溫耐磨性的關(guān)鍵。研究還發(fā)現(xiàn),進(jìn)一步控制金屬間化合物的成分類型,有助于進(jìn)一步配合本發(fā)明所述的多層梯度層級結(jié)構(gòu),有助于進(jìn)一步改善涂層的高溫耐磨性。
14.本發(fā)明中,所述的a7b6型金屬間化合物中的元素為fe、mo、co和w中的兩種及以上,優(yōu)選包含fe、mo、co和w;進(jìn)一步優(yōu)選包括fe7mo6、co7mo6、fe7w6、co7w6以及其四者之間相互形成的具有一定固溶度的金屬間化合物;
15.優(yōu)選地,各層的金屬間化合物中,還包含ab2型金屬間化合物,優(yōu)選地,ab2型金屬間化合物的元素包括fe、ni、ti、nb和mo中的兩種及以上,進(jìn)一步優(yōu)選包括fe、mo、ti和nb。研究發(fā)現(xiàn),各層中采用a7b6型金屬間化合物和ab2型金屬間化合物復(fù)合的金屬間化合物,有助于進(jìn)一步和所述的多層梯度層級結(jié)構(gòu)聯(lián)合,進(jìn)一步改善涂層的高溫耐磨性。
16.優(yōu)選地,所述的金屬間化合物中還包含cr元素相關(guān)的金屬間化合物。
17.本發(fā)明中,所述的層的成分以及層級梯度控制是協(xié)同改善涂層高溫耐磨性的關(guān)鍵。
18.作為優(yōu)選,底層中,按質(zhì)量百分比計,co:10~15%、mo與w元素總量:5~10%,其中w元素含量不超過5%(優(yōu)選為1~3%),ni:0.5~2%、ti:1~2%、nb:1~2%,cr:0.5~2%,余量為fe。本發(fā)明中,底層中的金屬間化合物由所述的成分原位形成。另外,所述的底層中還允許存在無法避免的雜質(zhì)。
19.作為優(yōu)選,過渡層中,按質(zhì)量百分比計,co:15~25%、mo與w總量:10~20%,其中w含量不超過10%(優(yōu)選為1~5%),ni:0.5~2%、ti:1~2%、nb:1~2%,cr:0.5~2%,碳化物:2~5%,其余為fe。本發(fā)明中,過渡層中的金屬間化合物由所述的成分原位形成。另外,本發(fā)明中,所述的過渡層中還允許存在無法避免的雜質(zhì)。
20.作為優(yōu)選,耐磨層中,按質(zhì)量百分比計,co:15~25%、mo與w總量:10~20%,其中w含量不超過10%(優(yōu)選為1~5%),ni:0.5~2%、ti:1~2%、nb:1~2%,cr:0.5~2%,碳化物:5~10%,其余為fe。本發(fā)明中,耐磨層中的金屬間化合物由所述的成分原位形成。另外,所述的耐磨層中還允許存在無法避免的雜質(zhì)。
21.本發(fā)明中,所述的碳化物為wc、tic、nbc和tac中的至少一種。
22.本發(fā)明中,所述的硫化層由耐磨層的表面原位硫化形成,例如,其可以包含fes、mos2等成分。
23.本發(fā)明中,各層的厚度可根據(jù)需要進(jìn)行調(diào)整,例如,底層的厚度為1~1.5mm;所述的過渡層的厚度為0.8~1.2mm;所述的耐磨層的厚度為1.2~1.7mm;所述的硫化層的厚度為0.1~0.3mm。
24.本發(fā)明還提供了一種所述的高溫梯度耐磨涂層材料的制備方法、包括以下步驟:
25.步驟(1):各層原料處理
26.將各層的原料分別和成型劑、輔助劑進(jìn)行濕式球磨,獲得料漿;將料漿進(jìn)行噴霧造粒、反應(yīng)燒結(jié),分別制得底層前驅(qū)粉末、過渡層前驅(qū)粉末和耐磨層前驅(qū)粉末:
27.步驟(2):
28.采用激光熔覆工藝,依次形成底層、過渡層和耐磨層;
29.步驟(3):
30.對步驟(2)制得的耐磨層進(jìn)行硫化處理;隨后進(jìn)行回火處理,即得。
31.本發(fā)明研究發(fā)現(xiàn),對于層級材料制備而言,其不同于塊體材料,其需要解決層級熱應(yīng)力和界面應(yīng)力干擾所致的難于復(fù)合、容易開裂等制備難點。針對涂層材料的制備難點,本發(fā)明研究發(fā)現(xiàn),創(chuàng)新地將各物料預(yù)先經(jīng)過
粉末冶金工藝獲得具有梯度成分的合金原料,隨后配合激光熔覆工藝以及硫化-回火工藝聯(lián)合,能夠解決層級應(yīng)力問題,能夠成功制備所述的涂層材料,并有助于改善制得的涂層材料的高溫耐磨性。
32.本發(fā)明中,將底層的各金屬原料(單質(zhì))按所述的元素比例配料,并和成型劑以及輔助劑進(jìn)行后續(xù)的濕法球磨、噴霧造粒以及反應(yīng)燒結(jié),制得底層合金原料粉末。將過渡層中的各金屬原料(單質(zhì))以及碳化物按所述的比例配料并和成型劑以及輔助劑進(jìn)行濕法球磨、噴霧造粒以及反應(yīng)燒結(jié),制得過渡層合金原料粉末。將耐磨層中的各金屬原料(單質(zhì))以及碳化物按所述的比例配料并和成型劑以及輔助劑進(jìn)行濕法球磨、噴霧造粒以及反應(yīng)燒結(jié),制得耐磨層合金原料粉末。
33.本發(fā)明中,首先根據(jù)各層的成分配料,例如,所述的底層的原料按co:10~15%、mo與w元素總量:5~10%(其中w元素含量不超過5%),ni:0.5~2%、ti:1~2%、nb:1~2%,cr:0.5~2%,余量為fe配料。過渡層的原料按co:15~25%、mo與w總量:10~20%,其中w含量不超過10%,ni:0.5~2%、ti:1~2%、nb:1~2%,cr:0.5~2%,碳化物:2~5%,其余為fe的比例配料。所述的耐磨層原料按co:15~25%、mo與w總量:10~20%,其中w含量不超過10%,ni:0.5~2%、ti:1~2%、nb:1~2%,cr:0.5~2%,碳化物:5~10%,其余為fe的比例配料。所述的配料百分比均指重量百分比。
34.本方法中,將各層配好的原料和輔助劑以及成型劑混合球磨后進(jìn)行造粒和燒結(jié),制得各層的前驅(qū)粉末。
35.優(yōu)選地,所述的輔助劑為b和si;輔助劑的添加,利于和所述的特殊成分以及梯度原料聯(lián)合,利于減少層級應(yīng)力,可以降低涂層氣孔率,增加熔池流動性;
36.優(yōu)選地,輔助劑中,b的添加量為各層原料總質(zhì)量的0.5~2wt.%,優(yōu)選為0.5~1wt.%;si的添加量為各層原料總質(zhì)量的0.5~2wt.%,優(yōu)選為0.5~1wt.%。
37.本發(fā)明步驟(1)中,成型劑可以行業(yè)內(nèi)技術(shù)人員能夠獲知的任意可以輔助物料成
型的材料,例如可為石蠟、peg、pvb中的至少一種;
38.本發(fā)明步驟(1)中,成型劑的添加含量可根據(jù)需要進(jìn)行調(diào)整,例如,成型劑添加量為各層原料總質(zhì)量的2~4%。
39.本發(fā)明步驟(1)中,球磨介質(zhì)可以是行業(yè)內(nèi)技術(shù)人員所公知的濕法球磨介質(zhì),例如,可以為無水乙醇。
40.本發(fā)明步驟(1)中,球磨過程中,球料質(zhì)量比可根據(jù)行業(yè)內(nèi)常規(guī)公知制備規(guī)律以及要求進(jìn)行調(diào)整,例如可以為(4~8):1;
41.本發(fā)明步驟(1)中,球磨時間可根據(jù)需要進(jìn)行調(diào)整,例如可以為72h~96h;
42.本發(fā)明中,可以采用行業(yè)通識方法進(jìn)行噴霧干燥造粒處理。例如,噴霧干燥造粒方式可為壓力式或離心式噴霧干燥造粒??刂浦迫〉姆勰┝6确秶鸀?0~200μm。作為進(jìn)一步的優(yōu)選,上述粉末粒度范圍為80~150μm。
43.優(yōu)選地,反應(yīng)燒結(jié)為氫氣燒結(jié)、氬氣燒結(jié)或真空燒結(jié);最終燒結(jié)溫度為800-850℃,燒結(jié)時間1-2h;
44.優(yōu)選地,激光熔覆處理階段在保護(hù)性氣氛下進(jìn)行:
45.底層制備時控制為15%~20%的大稀釋率,激光熔覆工藝參數(shù)為:光斑直徑為2-5mm,激光功率為900~1200w,掃描速度為400~800mm/min;
46.過渡層和耐磨層制備時保證為5%~10%的小稀釋率,激光熔覆工藝參數(shù)為:光斑直徑為2-5mm,激光功率為600~1000w,掃描速度為400~700mm/min;
47.優(yōu)選地,硫化處理采用以h2s氣體為硫源的真空低溫處理;真空度控制為5~10pa,滲流溫度為250~350℃,真空室內(nèi)充入h2s氣體,流量控制為100~200sccm,硫化時間為5~10h;
48.優(yōu)選地,回火處理的溫度為500~650℃;回火時間為20~60min。
49.本發(fā)明還提供了一種梯度耐磨涂層材料,包括基材,以及在所述基材表面制備的所述的高溫梯度耐磨涂層,其中,所述的底層與基材表面呈冶金結(jié)合;
50.優(yōu)選地,所述的基材可以是行業(yè)內(nèi)公知的任意需要的鋼件基材,為降低成本,所述基材可為q235鋼、45鋼或40cr等低合金鋼。
51.本發(fā)明還提供了一種所述的梯度耐磨涂層材料的制備方法,采用本發(fā)明的涂層制備方法,在基材表面制備所述的高溫梯度耐磨涂層;
52.優(yōu)選地,預(yù)先對基材進(jìn)行預(yù)處理,隨后再復(fù)合所述的高溫梯度耐磨涂層;
53.所述的預(yù)處理步驟為:將基材用砂輪機(jī)進(jìn)行打磨去除表面銹跡和氧化膜,再用砂紙打磨平整,最后用無水乙醇洗凈并干燥備用;進(jìn)行涂層制備前,在惰性氣體保護(hù)下進(jìn)行預(yù)熱處理,預(yù)熱溫度為150~200℃。
54.本發(fā)明一種更具體的梯度耐磨涂層材料的制備方法,包括以下步驟:
55.步驟(a):上述底層、過渡層和耐磨層合金粉末按以下步驟獲得:
56.1)將純金屬粉末(或碳化物粉末)按照所設(shè)計的成分比例與成型劑、輔助劑一同進(jìn)行濕式球磨,獲得混合均勻料漿;優(yōu)選地,步驟1)中球磨介質(zhì)為無水乙醇,球料比為(4~8):1,由于采用滾筒球磨機(jī)出料量多,優(yōu)選采用滾筒球磨機(jī)進(jìn)行球磨,球磨轉(zhuǎn)速為100~150r/min,球磨時間為72h~96h。優(yōu)選地,步驟1)中成型劑可為石蠟、peg、pvb,成型劑添加量為混合料總質(zhì)量的2~4%。所述的輔助劑為b和si單質(zhì)粉末;
57.2)混合料漿依次經(jīng)噴霧造粒、反應(yīng)燒結(jié)后獲得球形度良好、流動性佳、具有一定強(qiáng)度的合金粉末。優(yōu)選地,造粒原料的反應(yīng)燒結(jié)采用氫氣燒結(jié)、氬氣燒結(jié)或真空燒結(jié),最終燒結(jié)溫度為800-850℃,燒結(jié)時間1-2h。
58.步驟(b):基材預(yù)處理:
59.將基材用砂輪機(jī)進(jìn)行打磨去除表面銹跡和氧化膜,再用砂紙打磨平整,最后用無水乙醇洗凈并干燥備用。進(jìn)行涂層制備前,在惰性氣體保護(hù)下進(jìn)行預(yù)熱處理,預(yù)熱溫度為150~200℃。其中步驟(a)和步驟(b)可以按任意先后順序進(jìn)行;
60.步驟(c):涂層制備:
61.利用激光熔覆同步送粉技術(shù)在預(yù)處理好的基材上依次進(jìn)行底層、過渡層和耐磨層的制備,全程通入高純氬氣進(jìn)行保護(hù)。其中,底層制備時控制為15%~20%的大稀釋率,激光熔覆工藝參數(shù)為:光斑直徑為2-5mm,激光功率為900~1200w,掃描速度為400~800mm/min;過渡層和耐磨層制備時保證為5%~10%的小稀釋率,激光熔覆工藝參數(shù)為:光斑直徑為2-5mm,激光功率為600~1000w,掃描速度為400~700mm/min。
62.步驟(d):硫化處理:
63.對步驟c)中的涂層進(jìn)行硫化處理。
64.步驟(e):涂層硬化處理:
65.將涂層進(jìn)行回火處理,即可獲得具有高硬度和高耐磨性的金屬間化合物和碳化物復(fù)合強(qiáng)化高溫梯度耐磨涂層。
66.優(yōu)選地,步驟b)中需大規(guī)模進(jìn)行制備涂層時,基材可用噴砂處理清理表面。
67.優(yōu)選地,步驟d)中硫化處理采用以h2s氣體為硫源的真空低溫處理。真空度控制為5~10pa,滲流溫度為250~350℃,真空室內(nèi)充入h2s氣體,流量控制為100~200sccm,硫化時間為5~10h。
68.優(yōu)選地,步驟e)中回火處理在500~650℃下進(jìn)行,回火時間為20~60min?;鼗鹂赏ㄟ^回火爐、感應(yīng)線圈或低功率激光束和離子弧掃描進(jìn)行。作為進(jìn)一步的優(yōu)選,回火處理在真空回火爐中進(jìn)行。
69.本發(fā)明技術(shù)方案,得益于所述的高溫梯度耐磨涂層的成分以及結(jié)構(gòu)的聯(lián)合,可以有效改善耐磨材料的高溫耐磨性,可以將其應(yīng)用于任意要求高溫耐磨穩(wěn)定性的領(lǐng)域。
70.與現(xiàn)有技術(shù)相比,本發(fā)明具有如下有益效果:
71.1、本發(fā)明研究發(fā)現(xiàn),所述的底層、過渡層、耐磨層和硫化層的層級以及成分多梯度的聯(lián)合控制,能實現(xiàn)協(xié)同,能夠顯著改善涂層的高溫耐磨性。
72.2、在所述的涂層層級控制創(chuàng)新基礎(chǔ)上,進(jìn)一步控制各層的成分特點,有助于進(jìn)一步協(xié)同改善涂層的高溫耐磨穩(wěn)定性。
73.例如,本發(fā)明優(yōu)選的方案,所述的梯度涂層強(qiáng)化相為原位生成的a7b6及ab2型金屬間化合物和外加硬質(zhì)耐磨碳化物相,其中a7b6型金屬間化合物例如為fe7mo6、co7mo6、fe7w6、co7w6,ab2型金屬間化合物例如為fe2nb、fe2ti。所述金屬間化合物原位彌散析出,與基體存在對應(yīng)位向關(guān)系,強(qiáng)烈阻礙位錯,有著更強(qiáng)的熱穩(wěn)定性和抗聚集能力,使材料具備高硬度、出色的熱硬性及紅硬性,可保證優(yōu)良的高溫耐磨性能。所述硬質(zhì)耐磨碳化物相包括wc、tic、nbc和tac的一種或幾種的組合,具備高耐磨性,通過與上述金屬間化合物進(jìn)行復(fù)合強(qiáng)化,可保障涂層材料高溫下依然具有高耐磨性,特別是當(dāng)溫度高于600℃。
74.3.本發(fā)明設(shè)計底層低合金成分且具有大稀釋率,確保其與基材形成良好的冶金結(jié)合,保證高結(jié)合強(qiáng)度;同時,從底層到耐磨層的物理化學(xué)性能呈梯度分布,有效地降低不同層之間的熱應(yīng)力和界面應(yīng)力,對裂紋萌生和擴(kuò)展起到抑制作用,可最大程度避免熔覆過程開裂,提高工藝穩(wěn)定性。
75.4.本發(fā)明在梯度涂層表面硫化處理,獲得一層具有六方結(jié)構(gòu)的fes、mos2固體潤滑層,形成以高硬度和高耐磨的涂層為支撐的表面潤滑層復(fù)合結(jié)構(gòu),實現(xiàn)同時具有高耐磨、低摩擦系數(shù)和減磨的效果。
76.5.預(yù)先采用粉末燒結(jié)工藝,制得構(gòu)建各層的原料粉末,隨后配合所述的激光熔覆工藝,可以降低層級之間的應(yīng)力,有助于降低裂紋,成功制備所述的涂層材料,并改善制得的涂層的高溫耐磨性能。
附圖說明
77.圖1為實施例1和對比例4摩擦系數(shù)隨時間變化關(guān)系圖;
78.圖2為實施例1的45鋼基材與底層結(jié)合處顯微組織圖;
79.圖3為實施例1的過渡層與耐磨層顯微組織圖;
具體實施方式
80.為了更好的解釋本發(fā)明,以便于理解,下面通過以下實施例對本發(fā)明的技術(shù)方案和效果作詳細(xì)描述。
81.以下案例中,除特別聲明外,所述的百分比均指重量百分比;
82.實施例1
83.按設(shè)計方案配取原料:其中,底層成分及比例為12%co、6%mo、3%w,0.5%ni、1%ti、1%nb、1%cr,其余為fe;過渡層成分及比例為20%co、12%mo、3%w、2%wc、1%tic、0.5%ni、1%ti、1%nb、0.5%cr,其余為fe;耐磨層成分及比例為22%co、12%mo、4%w、6%wc、2%tic、0.5%ni、1%ti、1%nb、0.5%cr、其余為fe。分別將原料粉末、0.5%b(以各層成分重量為基準(zhǔn))、0.5%si(以各層成分重量為基準(zhǔn))、3%石蠟(以各層的成分重量為基準(zhǔn))放入滾筒球磨機(jī)進(jìn)行濕磨,球磨介質(zhì)為無水乙醇,球料比為5:1,球磨時間為72h,球磨轉(zhuǎn)速為150r/min。將球磨后的漿料進(jìn)行噴霧造粒獲得80~150μm粉末,經(jīng)最高溫度820℃真空燒結(jié)2h后得到球形度良好、流動性佳的預(yù)合金粉末。
84.以45鋼為基材,首先將基材用砂輪機(jī)進(jìn)行打磨去除表面銹跡和氧化膜,再用砂紙打磨平整,最后用無水乙醇洗凈并干燥;熔覆前將基材置于150℃真空烘箱中預(yù)熱30min。利用激光熔覆技術(shù)在高純氬氣保護(hù)下依次制備底層、過渡層和耐磨層,工藝參數(shù)分別為:底層:光斑直徑為5mm,激光功率為1000w,掃描速度為500mm/min;過渡層和耐磨層:光斑直徑為5mm,激光功率為800w,掃描速度為600mm/min。將制備的涂層置于真空度為5pa的腔室內(nèi),加熱至300℃并保溫,通入h2s氣體進(jìn)行硫化處理,氣體流量為150sccm,硫化時間為8h。最后,將硫化處理的涂層在真空回火爐中進(jìn)行回火處理,回火溫度為580℃,回火時間為1h。制得的底層、過渡層、耐磨層和硫化層的厚度分別為1.2mm、1.0mm、1.5mm和0.2mm。
85.實施例2
86.按設(shè)計方案配取原料:其中,底層成分及比例為10%co、4%mo、1%w,0.5%ni、1%
ti、1%nb、0.5%cr,其余為fe;過渡層成分及比例為15%co、9%mo、1%w、1%wc、1%tic、0.5%ni、1%ti、1%nb、0.5%cr,其余為fe;耐磨層成分及比例為15%co、9%mo、1%w、4%wc、1%tic、0.5%ni、1%ti、1%nb、0.5%cr,其余為fe。分別將原料粉末、0.5%b(以各層成分重量為基準(zhǔn))、0.5%si(以各層成分重量為基準(zhǔn))、3%石蠟(以各層的成分重量為基準(zhǔn))放入滾筒球磨機(jī)進(jìn)行濕磨,球磨介質(zhì)為無水乙醇,球料比為5:1,球磨時間為72h,球磨轉(zhuǎn)速為150r/min。將球磨后的漿料進(jìn)行噴霧造粒獲得80~150μm粉末,經(jīng)最高溫度820℃真空燒結(jié)2h后得到球形度良好、流動性佳的預(yù)合金粉末。
87.以45鋼為基材,首先將基材用砂輪機(jī)進(jìn)行打磨去除表面銹跡和氧化膜,再用砂紙打磨平整,最后用無水乙醇洗凈并干燥;熔覆前將基材置于150℃真空烘箱中預(yù)熱30min。利用激光熔覆技術(shù)在高純氬氣保護(hù)下依次制備底層、過渡層和耐磨層,工藝參數(shù)分別為:底層:光斑直徑為5mm,激光功率為1000w,掃描速度為500mm/min;過渡層和耐磨層:光斑直徑為5mm,激光功率為800w,掃描速度為600mm/min。將制備的涂層置于真空度為5pa的腔室內(nèi),加熱至300℃并保溫,通入h2s氣體進(jìn)行硫化處理,氣體流量為150sccm,硫化時間為8h。最后,將硫化處理的涂層在真空回火爐中進(jìn)行回火處理,回火溫度為590℃,回火時間為1h。制得底層、過渡層、耐磨層和硫化層的厚度分別為1.1mm、1.1mm、1.4mm和0.2mm。
88.實施例3
89.按設(shè)計方案配取原料:其中,底層成分及比例為15%co、8%mo、2%w,2%ni、2%ti、2%nb、2%cr,其余為fe;過渡層成分及比例為25%co、15%mo、5%w、4%wc、1%tic、2%ni、2%ti、2%nb、2%cr,其余為fe;耐磨層成分及比例為25%co、15%mo、5%w、4%wc、4%nbc、2%tic、2%ni、2%ti、2%nb、2%cr,其余為fe。分別將原料粉末、0.5%b(以各層成分重量為基準(zhǔn))、0.5%si(以各層成分重量為基準(zhǔn))、3%石蠟(以各層的成分重量為基準(zhǔn))放入滾筒球磨機(jī)進(jìn)行濕磨,球磨介質(zhì)為無水乙醇,球料比為5:1,球磨時間為72h,球磨轉(zhuǎn)速為150r/min。將球磨后的漿料進(jìn)行噴霧造粒獲得80~150μm粉末,經(jīng)最高溫度830℃真空燒結(jié)2h后得到球形度良好、流動性佳的預(yù)合金粉末。
90.以45鋼為基材,首先將基材用砂輪機(jī)進(jìn)行打磨去除表面銹跡和氧化膜,再用砂紙打磨平整,最后用無水乙醇洗凈并干燥;熔覆前將基材置于150℃真空烘箱中預(yù)熱30min。利用激光熔覆技術(shù)在高純氬氣保護(hù)下依次制備底層、過渡層和耐磨層,工藝參數(shù)分別為:底層:光斑直徑為5mm,激光功率為1000w,掃描速度為500mm/min;過渡層和耐磨層:光斑直徑為5mm,激光功率為800w,掃描速度為600mm/min。將制備的涂層置于真空度為5pa的腔室內(nèi),加熱至300℃并保溫,通入h2s氣體進(jìn)行硫化處理,氣體流量為150sccm,硫化時間為10h。最后,將硫化處理的涂層在真空回火爐中進(jìn)行回火處理,回火溫度為600℃,回火時間為1h。制得底層、過渡層、耐磨層和硫化層的厚度分別為1.2mm、1.0mm、1.3mm和0.2mm。
91.實施例4
92.按設(shè)計方案配取原料:其中,底層成分及比例為12%co、6%mo、3%w,0.5%ni、1%ti、1%nb、1%cr,其余為fe;過渡層成分及比例為20%co、12%mo、3%w、2%wc、1%tic、0.5%ni、1%ti、1%nb、0.5%cr,其余為fe;耐磨層成分及比例為22%co、12%mo、4%w、6%wc、2%tic、0.5%ni、1%ti、1%nb、0.5%cr,其余為fe。分別將原料粉末、0.5%b(以各層成分重量為基準(zhǔn))、0.5%si(以各層成分重量為基準(zhǔn))、3%石蠟(以各層的成分重量為基準(zhǔn))放入滾筒球磨機(jī)進(jìn)行濕磨,球磨介質(zhì)為無水乙醇,球料比為6:1,球磨時間為84h,球磨轉(zhuǎn)速為
150r/min。將球磨后的漿料進(jìn)行噴霧造粒獲得80~150μm粉末,經(jīng)最高溫度820℃真空燒結(jié)2h后得到球形度良好、流動性佳的預(yù)合金粉末。
93.以45鋼為基材,首先將基材用砂輪機(jī)進(jìn)行打磨去除表面銹跡和氧化膜,再用砂紙打磨平整,最后用無水乙醇洗凈并干燥;熔覆前將基材置于150℃真空烘箱中預(yù)熱30min。利用激光熔覆技術(shù)在高純氬氣保護(hù)下依次制備底層、過渡層和耐磨層,工藝參數(shù)分別為:底層:光斑直徑為3mm,激光功率為1200w,掃描速度為600mm/min;過渡層和耐磨層:光斑直徑為3mm,激光功率為900w,掃描速度為600mm/min。將制備的涂層置于真空度為5pa的腔室內(nèi),加熱至300℃并保溫,通入h2s氣體進(jìn)行硫化處理,氣體流量為150sccm,硫化時間為8h。最后,將硫化處理的涂層在真空回火爐中進(jìn)行回火處理,回火溫度為590℃,回火時間為1h。制得底層、過渡層、耐磨層和硫化層的厚度分別為1.3mm、1.1mm、1.2mm和0.2mm。
94.實施例5
95.按設(shè)計方案配取原料:其中,底層成分及比例為12%co、6%mo、3%w,0.5%ni、1%ti、1%nb、1%cr,其余為fe;過渡層成分及比例為20%co、12%mo、3%w、2%wc、1%tic、0.5%ni、1%ti、1%nb、0.5%cr,其余為fe;耐磨層成分及比例為22%co、12%mo、4%w、6%wc、2%tic、0.5%ni、1%ti、1%nb、0.5%cr,其余為fe。分別將原料粉末、0.5%b(以各層成分重量為基準(zhǔn))、0.5%si(以各層成分重量為基準(zhǔn))、3%石蠟(以各層的成分重量為基準(zhǔn))放入滾筒球磨機(jī)進(jìn)行濕磨,球磨介質(zhì)為無水乙醇,球料比為6:1,球磨時間為84h,球磨轉(zhuǎn)速為140r/min。將球磨后的漿料進(jìn)行噴霧造粒獲得80~150μm粉末,經(jīng)最高溫度840℃真空燒結(jié)2h后得到球形度良好、流動性佳的預(yù)合金粉末。
96.以45鋼為基材,首先將基材用砂輪機(jī)進(jìn)行打磨去除表面銹跡和氧化膜,再用砂紙打磨平整,最后用無水乙醇洗凈并干燥;熔覆前將基材置于150℃真空烘箱中預(yù)熱30min。利用激光熔覆技術(shù)在高純氬氣保護(hù)下依次制備底層、過渡層和耐磨層,工藝參數(shù)分別為:底層:光斑直徑為3mm,激光功率為1100w,掃描速度為700mm/min;過渡層和耐磨層:光斑直徑為3mm,激光功率為700w,掃描速度為700mm/min。將制備的涂層置于真空度為5pa的腔室內(nèi),加熱至300℃并保溫,通入h2s氣體進(jìn)行硫化處理,氣體流量為150sccm,硫化時間為8h。最后,將硫化處理的涂層在真空回火爐中進(jìn)行回火處理,回火溫度為580℃,回火時間為0.75h。制得底層、過渡層、耐磨層和硫化層的厚度分別為1.1mm、1.1mm、1.25mm和0.2mm。
97.對比例1
98.和實施例1相比,區(qū)別僅在于,缺少過渡層和耐磨層,也即是,按實施例1的工藝,在基材上依次形成底層和硫化層。
99.對比例2
100.和實施例1相比,區(qū)別僅在于,缺少耐磨層,也即是,按實施例1的方法依次在基底上形成底層、過渡層和硫化層。
101.對比例3
102.和實施例1相比,區(qū)別僅在于,缺少底層和過渡層,也即是,按實施例1的工藝和參數(shù)在基底上依次形成耐磨層和硫化層。制備的涂層開裂,制備失敗。
103.對比例4
104.和實施例1相比,區(qū)別僅在于,未進(jìn)行硫化處理。
105.對比例5
106.和實施例1相比,區(qū)別僅在于,底層、過渡層和耐磨層的化學(xué)成分除碳化物形成梯度外,其他成分相同(均為底層成分),主要步驟在于:
107.例如,底層成分及比例為12%co、6%mo、3%w,0.5%ni、1%ti、1%nb、1%cr,其余為fe;過渡層成分及比例為12%co、6%mo、3%w,0.5%ni、1%ti、1%nb、1%cr、2%wc、1%tic,其余為fe;耐磨層成分及比例為12%co、6%mo、3%w,0.5%ni、1%ti、1%nb、1%cr、6%wc、2%tic;其余為fe。
108.其他制備參數(shù)同實施例1.
109.對比例6
110.和實施例1相比,區(qū)別僅在于,過渡層和耐磨層成分中未添加碳化物,主要步驟在于:
111.例如,底層成分及比例為12%co、6%mo、3%w,0.5%ni、1%ti、1%nb、1%cr,其余為fe;過渡層成分及比例為20%co、12%mo、3%w、0.5%ni、1%ti、1%nb、0.5%cr,其余為fe;耐磨層成分及比例為22%co、12%mo、4%w、0.5%ni、1%ti、1%nb、0.5%cr,其余為fe。
112.其他制備參數(shù)同實施例1。
113.對比例7
114.和實施例1相比,區(qū)別僅在于,過渡層和耐磨層成分中添加碳化物含量未形成梯度,均為8%:
115.例如,底層成分及比例為12%co、6%mo、3%w,0.5%ni、1%ti、1%nb、1%cr,其余為fe;過渡層成分及比例為20%co、12%mo、3%w、6%wc、2%tic、0.5%ni、1%ti、1%nb、0.5%cr,其余為fe;耐磨層成分及比例為22%co、12%mo、4%w、6%wc、2%tic、0.5%ni、1%ti、1%nb、0.5%cr,其余為fe。
116.其他制備參數(shù)同實施例1。制備的涂層開裂,制備失敗。
117.將上述實施例和對比例制備的涂層樣品在相同實驗條件下進(jìn)行高溫摩擦磨損實驗。實驗設(shè)備為ht-1000高溫摩擦磨損試驗機(jī),實驗條件為:實驗溫度700℃,載荷30n,頻率5hz,對磨材料si3n4球。平均摩擦系數(shù)和磨損率實驗結(jié)果如表1所示。實施例1和對比例4的摩擦系數(shù)隨實驗時間變化曲線如圖1所示。
118.表1實施例和對比例的700℃摩擦磨損測試平均摩擦系數(shù)和磨損率結(jié)果
[0119][0120]
可以看出,與基材相比,實施例1-5磨損率大幅下降,表明具有優(yōu)異的高溫耐磨性能;同時與對比例4對比可知,經(jīng)硫化處理后得到的表面硫化層具有出色的潤滑減磨性能,使得平均摩擦系數(shù)從0.551下降至0.232。技術(shù)特征:
1.一種高溫梯度耐磨涂層,其特征在于,包括底層、過渡層、耐磨層,以及在耐磨層表面硫化形成的硫化層;所述的底層包括馬氏體基體以及彌散在其中的金屬間化合物;所述的過渡層、耐磨層均包括馬氏體基體以及彌散分布在其中的金屬間化合物和碳化物;其中,過渡層、耐磨層中的金屬間化合物的含量大于底層的金屬間化合物的含量;耐磨層中的碳化物的含量大于過渡層中的碳化物的含量;且所述的金屬間化合物包含a7b6金屬間化合物。2.如權(quán)利要求1所述的高溫梯度耐磨涂層,其特征在于,所述的a7b6型金屬間化合物中的元素為fe、mo、co和w中的兩種及以上,優(yōu)選包含fe、mo、co和w;進(jìn)一步優(yōu)選包括fe7mo6、co7mo6、fe7w6、co7w6以及其四者之間相互形成的具有一定固溶度的金屬間化合物;優(yōu)選地,各層的金屬間化合物中,還包含ab2型金屬間化合物,優(yōu)選地,ab2型金屬間化合物的元素包括fe、ni、ti、nb和mo中的兩種及以上,進(jìn)一步優(yōu)選包括fe、mo、ti和nb;優(yōu)選地,所述的金屬間化合物中還包含cr元素相關(guān)的金屬間化合物。3.如權(quán)利要求2所述的高溫梯度耐磨涂層,其特征在于,底層中,按質(zhì)量百分比計,co:10~15%、mo與w元素總量:5~10%,其中w元素含量不超過5%,ni:0.5~2%、ti:1~2%、nb:1~2%,cr:0.5~2%,余量為fe。4.如權(quán)利要求2所述的高溫梯度耐磨涂層,其特征在于,過渡層中,按質(zhì)量百分比計,co:15~25%、mo與w總量:10~20%,其中w含量不超過10%,ni:0.5~2%、ti:1~2%、nb:1~2%,cr:0.5~2%,碳化物:2~5%,其余為fe。5.如權(quán)利要求2所述的高溫梯度耐磨涂層,其特征在于,耐磨層中,按質(zhì)量百分比計,co:15~25%、mo與w總量:10~20%,其中w含量不超過10%,ni:0.5~2%、ti:1~2%、nb:1~2%,cr:0.5~2%,碳化物:5~10%,其余為fe。6.如權(quán)利要求1~5任一項所述的高溫梯度耐磨涂層,其特征在于,所述的碳化物為wc、tic、nbc和tac中的至少一種。7.一種權(quán)利要求1~6任一項所述的高溫梯度耐磨涂層的制備方法、其特征在于,包括以下步驟:步驟(1):各層原料處理將各層的原料分別和成型劑、輔助劑進(jìn)行濕式球磨,獲得料漿;將料漿進(jìn)行噴霧造粒、反應(yīng)燒結(jié),分別制得底層前驅(qū)粉末、過渡層前驅(qū)粉末和耐磨層前驅(qū)粉末:步驟(2):采用激光熔覆工藝,依次形成底層、過渡層和耐磨層;步驟(3):對步驟(2)制得的耐磨層進(jìn)行硫化處理;隨后進(jìn)行回火處理,即得。8.如權(quán)利要求7所述的制備方法、其特征在于,步驟(1)中,球磨介質(zhì)為無水乙醇;優(yōu)選地,球磨過程中,球料比為(4~8):1;優(yōu)選地,球磨時間為72h~96h;優(yōu)選地,成型劑可為石蠟、peg、pvb中的至少一種;優(yōu)選地,成型劑添加量為各層原料總質(zhì)量的2~4%;
優(yōu)選地,所述的輔助劑為b和si;優(yōu)選地,輔助劑中,b的添加量為各層原料總質(zhì)量的0.5~2wt.%;si的添加量為各層原料總質(zhì)量的0.5~2wt.%;優(yōu)選地,反應(yīng)燒結(jié)為氫氣燒結(jié)、氬氣燒結(jié)或真空燒結(jié);最終燒結(jié)溫度為800-850℃,燒結(jié)時間1-2h;優(yōu)選地,激光熔覆處理階段在保護(hù)性氣氛下進(jìn)行:底層制備時控制為15%~20%的大稀釋率,激光熔覆工藝參數(shù)為:光斑直徑為2-5mm,激光功率為900~1200w,掃描速度為400~800mm/min;過渡層和耐磨層制備時保證為5%~10%的小稀釋率,激光熔覆工藝參數(shù)為:光斑直徑為2-5mm,激光功率為600~1000w,掃描速度為400~700mm/min;優(yōu)選地,硫化處理采用以h2s氣體為硫源的真空低溫處理;真空度控制為5~10pa,滲流溫度為250~350℃,真空室內(nèi)充入h2s氣體,流量控制為100~200sccm,硫化時間為5~10h;優(yōu)選地,回火處理的溫度為500~650℃;回火時間為20~60min。9.一種梯度耐磨涂層材料,其特征在于,包括基材,以及在所述基材表面制備的權(quán)利要求1~6任一項所述的高溫梯度耐磨涂層,其中,所述的底層與基材表面呈冶金結(jié)合;優(yōu)選地,所述的基材為鋼材基材。10.一種權(quán)利要求9所述的梯度耐磨涂層材料的制備方法,其特征在于,采用權(quán)利要求7或8所述的制備方法,在基材表面制備所述的高溫梯度耐磨涂層;優(yōu)選地,預(yù)先對基材進(jìn)行預(yù)處理,隨后再制備所述的高溫梯度耐磨涂層;所述的預(yù)處理步驟為:將基材用砂輪機(jī)進(jìn)行打磨去除表面銹跡和氧化膜,再用砂紙打磨平整,最后用無水乙醇洗凈并干燥備用;進(jìn)行涂層制備前,在惰性氣體保護(hù)下進(jìn)行預(yù)熱處理,預(yù)熱溫度為150~200℃。
技術(shù)總結(jié)
本發(fā)明耐磨材料領(lǐng)域,具體公開了一種高溫梯度耐磨涂層,包括底層、過渡層、耐磨層,以及在耐磨層表面硫化形成的硫化層;所述的底層包括馬氏體基體以及彌散在其中的金屬間化合物;所述的過渡層、耐磨層均包括馬氏體基體以及彌散分布在其中的金屬間化合物和碳化物;其中,過渡層、耐磨層中的金屬間化合物的含量大于底層的金屬間化合物的含量;耐磨層中的碳化物的含量大于過渡層中的碳化物的含量。本發(fā)明還包括所述的涂層的制備和應(yīng)用,以及形成有所述涂層的耐磨材料及其制備。本發(fā)明研究發(fā)現(xiàn),所述的金屬間化合物以及碳化物雙梯度控制的層級涂層具有優(yōu)異的協(xié)同性,可以顯著改善涂層的高溫(如700℃)耐磨性能。溫(如700℃)耐磨性能。溫(如700℃)耐磨性能。
技術(shù)研發(fā)人員:謝豐偉 陳帥鵬 康希越 張乾坤 陳豫章
受保護(hù)的技術(shù)使用者:長沙市薩普
新材料有限公司
技術(shù)研發(fā)日:2022.01.20
技術(shù)公布日:2022/6/4
聲明:
“高溫梯度耐磨涂層及其制備和應(yīng)用的制作方法” 該技術(shù)專利(論文)所有權(quán)利歸屬于技術(shù)(論文)所有人。僅供學(xué)習(xí)研究,如用于商業(yè)用途,請聯(lián)系該技術(shù)所有人。
我是此專利(論文)的發(fā)明人(作者)